Cost Analysis of 3D Printed Houses: A Comprehensive Overview
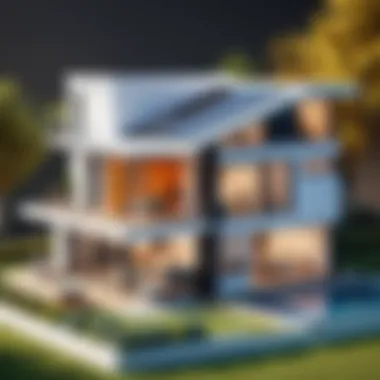
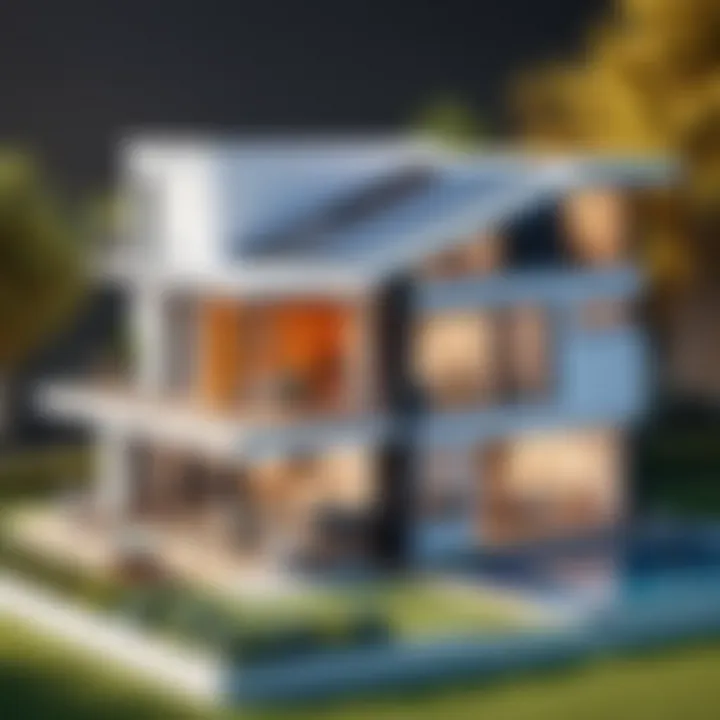
Intro
As the construction industry seeks innovative solutions to meet housing demands, 3D printing emerges as a transformative technology. This technique promises to reduce building time, cut costs, and create sustainable living options. But how do we assess the financial implications of such revolutionary methods? In this exploration of cost analysis, we will break down the essential elements influencing pricing in the realm of 3D printed houses.
Tech Trend Analysis
Overview of the current trend
The increasing adoption of 3D printing in construction reveals a shift towards more affordable housing options. Companies like ICON, Apis Cor, and SQ4D are leading the way, showcasing the viability of this technology. 3D printing allows for precise material usage, resulting in less waste. Moreover, these homes can often be printed on-site, eliminating many logistical challenges of traditional construction.
Implications for consumers
For consumers, understanding the cost structure is essential. The affordability of 3D printed homes hinges on various factors such as material choice, design, and location. This transparency can help potential buyers make educated decisions regarding their investments. As the market matures, financing options may also become accessible, making homeownership a reality for a larger demographic.
Future predictions and possibilities
Looking ahead, as technology advances, production costs are expected to decline. Innovations in materials and construction techniques could minimize expenses further, making 3D printed houses even more appealing. This, coupled with environmentally conscious design, indicates a significant potential for growth in sustainable housing.
Cost Breakdown
Materials
The materials used in 3D printing largely dictate the costs incurred. 3D-printed structures often utilize concrete, which is generally cheaper than traditional building materials. However, specialty materials, such as thermoplastics and bio-based materials, can drive up costs. Understanding the range of material options and their implications on price is crucial for prospective homeowners.
Labor Costs
Labor costs for 3D printed houses are significantly lower when compared to traditional methods. The automated nature of 3D printing reduces the need for skilled labor. However, specialized technicians are still necessary for initial setup and maintenance.
Regional Variations
Cost varies widely by region. In areas with higher demand for housing, prices may increase, even in the presence of 3D printing technology. Local building codes and land prices also affect the overall cost.
Design Complexity and Features
Design intricacy plays a vital role in the ultimate cost. Simple designs are generally more affordable. Adding complexity or unique features, however, increases the material use and production time, which can inflate expenses.
Industry Updates
Recent developments in the tech industry
Recent advancements involve ongoing research and development into alternative materials that could be used for 3D printing. Innovations in solar-energy integration within the construction of these homes are also being explored, aiming to reduce long-term energy costs for residents.
Analysis of market trends
The market for 3D printed houses is gradually becoming competitive. As more players enter the industry, consumers may benefit from price reductions and enhanced service offerings.
Impact on businesses and consumers
For businesses, this technology signifies a pivot towards efficiency. Companies leveraging 3D printing can potentially improve their profit margins while offering lower costs to consumers. On the consumer end, it addresses significant needs for affordable housing amidst rising property prices.
Ending
This article provides a lens to assess the financial realities surrounding 3D printed houses. From materials and labor costs to market implications, understanding these factors is pivotal for anyone considering this alternative housing option. As the technology evolves, it promises to reshape the future of home construction in a practical and financially savvy manner.
Prelims to 3D Printed Houses
The emergence of 3D printing technology in the construction industry has ushered in a new paradigm in how we think about housing. Understanding this topic is crucial, as it intertwines innovative technology with economic considerations, redefining the traditional construction landscape. The significance of 3D printed houses lies not just in their construction method but also in their potential to address widespread housing shortages and affordability issues.
What is 3D Printing?
3D printing, or additive manufacturing, is a process that creates three-dimensional objects from a digital file. It involves layering materials to form structures, rather than subtracting material as in conventional methods. In the context of construction, 3D printing has the potential to drastically reduce the time and cost associated with building homes. The various materials used in this process can include concrete, plastics, or even bio-materials designed for durability and sustainability.
This technology is not limited to simple shapes; it allows for intricate designs that were previously challenging or impossible to achieve. It also enables rapid prototyping, which can streamline design and construction phases significantly.
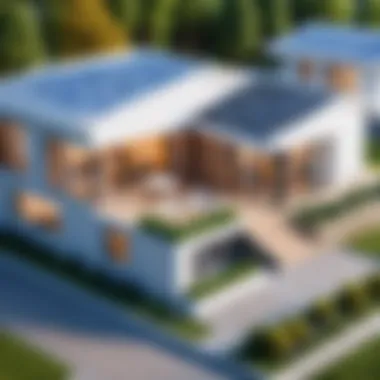
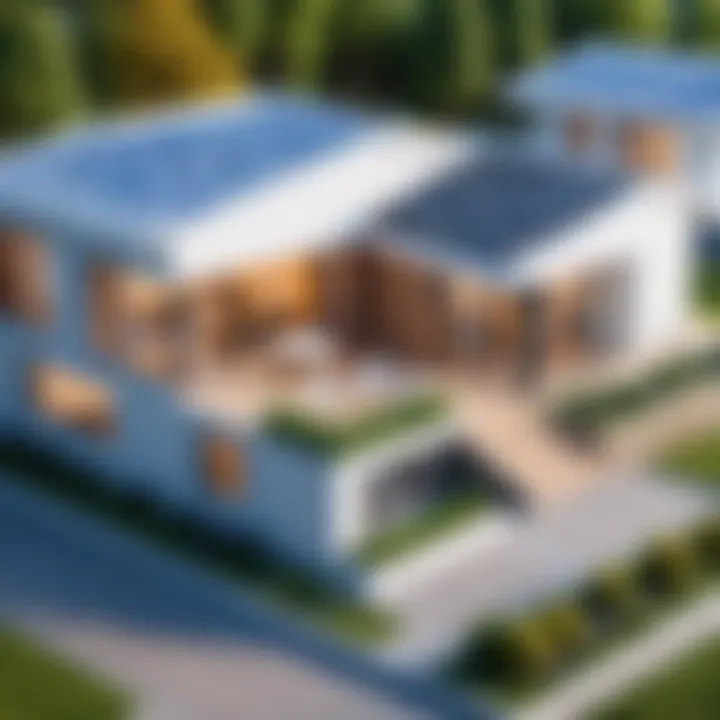
History and Evolution of 3D Printing in Construction
The concept of 3D printing dates back to the 1980s, but its application in construction is a more recent development. Early experiments with 3D printing in building construction took place in the late 1990s. However, it wasn't until the last decade that significant advancements were made. Improved materials and enhanced printing techniques have opened new avenues for architecture and construction.
Today, several companies and research institutions are pioneering efforts in 3D printed homes. For instance, ICON, a technology startup based in Austin, Texas, has made headlines for its Vulcan printer, which can construct a house in just a few days. Another notable example is the Apis Cor company, which successfully printed a structure on-site in just 24 hours. These developments illuminate the evolutionary path of 3D printing in the construction sector, showcasing both its practicality and market potential.
3D printing technology is rapidly being integrated into various segments of construction, promising not only enhanced efficiency but also sustainability. The capability to minimize waste and utilize local materials may revolutionize how housing is produced globally. Understanding both the historical context and the current advancements provides a solid foundation for analyzing the costs involved in 3D printed houses.
Understanding the Cost Structure
Understanding the cost structure of 3D printed houses is vital for anyone interested in this emerging construction method. It impacts overall project feasibility and helps potential buyers evaluate their investment against traditional housing options. This section focuses on key elements that shape the cost of 3D printed homes. By dissecting these elements, buyers can make informed decisions while also understanding the broader implications for the housing market.
Base Material Costs
Base material costs form the foundation of any construction project, including 3D printed houses. This refers to the expenses associated with obtaining raw materials necessary for printing. Common materials used in 3D printing of houses include concrete, polymers, and sometimes even composites. Each material has its own unique cost factors. For instance, concrete generally provides a good balance between price and structural integrity. The emerging use of sustainable materials like recycled plastics can lead to decreased costs in some instances, but research and development expenses may initially raise overall prices.
Factors influencing material costs might include local availability and sourcing logistics. If a particular material is abundant in a region, it could lead to lower prices. Conversely, challenging logistics may inflate costs, particularly if components must be shipped from distant suppliers. Additionally, investing in high-quality materials may enhance durability and reduce long-term maintenance costs, creating a more favorable overall financial picture.
Labor Costs: A Different Perspective
The expertise needed for operating the technology, designing the prints, and ensuring proper installation should be acknowledged. Many regions lack skilled labor specifically trained in 3D printing techniques, which can lead to higher costs as demand outstrips supply. A workforce trained in specialized technology can command premium wages, which affects the overall cost of the build.
Moreover, while the speed of construction increases with 3D printing, unforeseen complications might arise. This could result in additional labor time and expenses that need to be factored into the total cost structure. Ultimately, buyers should consider both the direct labor costs and the value of skilled labor when assessing the overall financial implications of a 3D printed house.
Regional Pricing Variations
Understanding the regional pricing variations of 3D printed houses is crucial for potential buyers and investors alike. The location of a project has a direct influence on costs, including labor, materials, and regulatory compliance. Recognizing these variations promotes informed decision-making and helps estimate budgets accurately. As the technology continues to evolve, local market dynamics also play a pivotal role in shaping the financial landscape of 3D printed architecture.
Impact of Location on Cost
Location impacts numerous elements that contribute to the final cost of constructing a 3D printed home. Factors such as transportation costs for materials, availability of skilled labor, and local market demand must be considered. For example, urban areas may exhibit higher material costs due to increased demand and limited supply chains. Conversely, rural areas may have lower costs, but they could face challenges with access to specialized equipment or knowledgeable workers.
Another consideration is the regulatory environment. Some regions have stringent building codes, which can increase compliance costs. In contrast, regions with more lenient regulations may result in lower overall expenses. These regional trends should be accounted for when estimating budgets.
"Location is not merely a geographical consideration, but a complex web of economic, regulatory, and logistical factors that dictate the overall cost of 3D printed houses."
Comparative Analysis: Urban vs Rural
The difference in cost between urban and rural settings is significant and worth analyzing. In urban locations, 3D printed houses may correspond with higher costs in several areas:
- Land Acquisition: Urban land prices can be exorbitant, affecting the overall budget.
- Labor Costs: Skilled labor is often more available but can also come with a higher price tag due to increased living costs in cities.
- Material Availability: While urban areas might have better access to diverse construction resources, the high demand often inflates prices.
On the other hand, rural areas provide different advantages and disadvantages:
- Lower Land Costs: Generally, the cost of land is more affordable.
- Access to Resources: However, material availability might be limited in less populated areas, impacting both price and timeline for construction.
- Labor Pool: There may be fewer trained professionals, which can mean higher travel costs or delays in hiring the right people.
Factors Influencing the Cost of 3D Printed Houses
Understanding the factors that influence the cost of 3D printed houses is crucial for potential buyers and industry stakeholders. These factors are multifaceted, impacting not just the price but also the feasibility and appeal of 3D printed homes. By recognizing these determinants, stakeholders can make informed decisions regarding investments in this innovative technology.
Several key elements shape the cost structure of 3D printed houses, among which are design complexity, customization options, technological advancements, and the materials selected for construction. Each of these aspects contributes to the overall investment needed and reflects the growing versatility and potential of 3D printing in the housing market.
Design Complexity and Customization
Design complexity is a significant factor that influences the cost of a 3D printed house. The more intricate the design, the higher the production costs. Complex designs may require specialized software for modeling and additional time for printing, thus increasing the overall budget.
Customization also plays a role. Many consumers desire unique homes tailored to their personal preferences. Customization leads to additional costs, as it requires more labor and sophisticated technology.
- Higher design complexity: More layers and detailed features can lengthen printing time and require more material.
- Customization: Unique features, like specific layouts or physical structures, demand advanced printing techniques.
- Standardization vs. Bespoke: Standard models may offer cost savings, while bespoke designs elevate expenses but cater to distinct tastes.
Ultimately, striking a balance between desired aesthetics and cost efficiency is essential for buyers.
Technological Advancements and Their Costs
Technological advancements in 3D printing are both a boon and a challenge for cost management. The evolution of printing technology has significantly impacted the cost of 3D printed houses. Recent innovations have made it possible to print faster, use less material, and improve build quality. However, these modern technologies often come with a steep price tag.

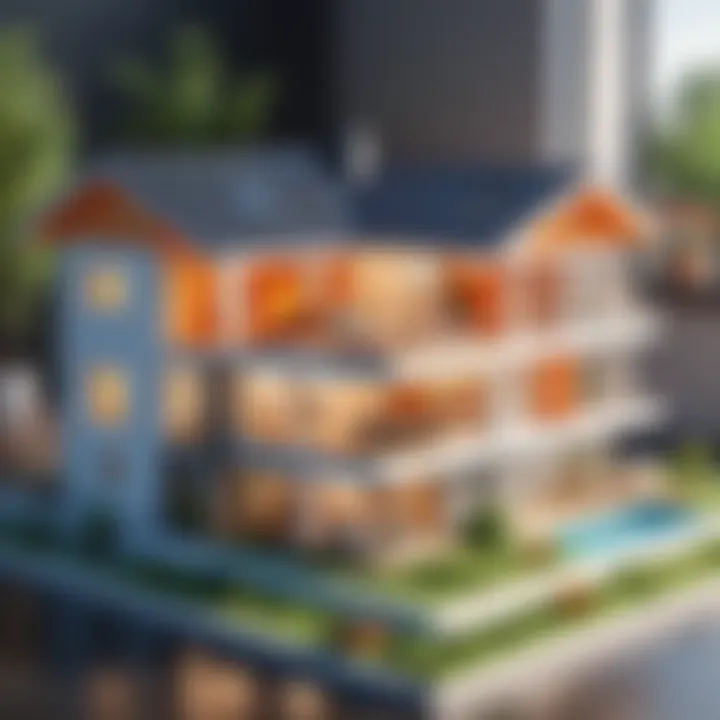
- Investment in technology: Newer, more efficient printers can be costly, affecting the initial set-up costs for manufacturers and builders.
- Ongoing training: As technology evolves, personnel may require training to operate new equipment, adding to expenses.
- Material innovation: New materials developed for enhanced durability or energy efficiency can also lead to higher costs but may provide long-term savings through reduced maintenance.
Price Range Expectations
Understanding the price range for 3D printed houses is pivotal for anyone considering this innovative construction method. This segment highlights the financial implications associated with 3D printing, from basic costs to some of the more opulent designs. By grasping the expected costs, buyers can make informed decisions that align with their budgets and needs. Knowing the price range helps in evaluating the viability, accessibility, and benefits of 3D printed homes compared to traditional construction.
Typical Costs of 3D Printed Homes
The costs of 3D printed homes can vary widely based on several factors including size, location, and design choices. On average, 3D printed houses can range from $10,000 to upwards of $300,000. The price depends largely on material selection and the complexity of the build.
- Basic Models: Smaller, simple designs can be printed for relatively low costs. A one-bedroom, no-frills house might stand around $10,000 to $20,000 depending on the materials used and the location of the project.
- Standard Units: More spacious configurations with basic finishes tend to fall in the $50,000 to $150,000 range. Features like enhanced insulation or energy-efficient systems can impact costs, providing a more sustainable living environment.
- High-End Structures: Large homes with intricate designs start at $150,000 and can exceed $300,000. Customizations play a significant role in driving the costs higher, especially if luxury materials or unique architectural designs are involved.
Overall, typical costs present a diverse landscape, making it essential for buyers to analyze what fits their budget while matching their desired specifications.
Luxury vs Budget Options
When exploring the price range of 3D printed houses, it is vital to distinguish between luxury and budget options.
Budget Options:
- Designed for affordability, these homes prioritize cost-effective materials and efficient building methods.
- Common choices in this category include basic concrete mixtures and lesser-known design techniques, which contribute to lower overall expenses.
- Maintenance and design might not go beyond fundamental structures and finishes, appealing to first-time home buyers or those in need of low-cost housing.
Luxury Options:
- High-end 3D printed houses often embrace advanced materials and cutting-edge technology.
- Utilizing premium materials leads to better aesthetics and longer durability but significantly raises construction costs.
- These homes can incorporate smart technologies, luxury appliances, and bespoke design features, appealing to affluent individuals seeking unique living experiences.
The divergence in pricing between luxury and budget structures is vast, so prospective buyers should assess their personal values and needs before pursuing a particular option.
Regulatory Considerations
The construction of 3D printed houses is not only a pioneering venture in technology but also a complex landscape of regulations and compliance requirements. As the industry evolves, it is critical to recognize the impact of these regulations on the overall cost of building and the feasibility of projects. Regulatory considerations encompass various elements, including building codes, zoning laws, and environmental standards.
Understanding regulatory frameworks is vital for investors and builders. Non-compliance can lead to delays and additional costs, ultimately affecting the economic viability of a 3D printed home. By navigating these regulations effectively, stakeholders can mitigate financial risks and ensure their projects proceed smoothly.
Building Codes and Compliance Costs
Building codes dictate the standards for construction and safety. For 3D printed houses, these codes may vary significantly by region. Compliance costs can include assessments, modifications to designs, or even additional materials needed to meet local regulations.
The cost of compliance often hinges on specific factors:
- Location: Different cities or states have unique building codes, leading to varying compliance costs.
- Material Standards: Some locales may mandate specific materials or construction techniques, affecting the initial cost of sourcing materials.
- Inspections: Regular inspections may be required during the construction phase, generating additional labor costs.
These elements can drive up overall project costs, making it essential for builders to integrate compliance considerations into their financial planning early on.
Permitting Process and its Financial Implications
Acquiring the necessary permits is a fundamental step in any construction project. For 3D printed houses, the permitting process can often be convoluted and time-consuming. The financial implications of this process can be significant for several reasons.
- Timeline Delays: Lengthy permitting processes can push back construction timelines, resulting in additional carrying costs and potential lost revenue.
- Application Fees: Local governments often require fees for permit applications, which can accumulate and impact budget allocation.
- Unforeseen Modifications: Sometimes, revisions to designs or methods may be required to satisfy permit conditions, leading to increased costs and time.
Overall, the permitting process and related financial implications must be meticulously planned and executed to ensure that the project remains economically viable and compliant with all local laws.
Understanding the complexities of regulatory considerations is essential for anyone considering investing in 3D printed housing.
Financing Options for 3D Printed Houses
The financing landscape for 3D printed houses is evolving as the technology gains more traction in the construction industry. Understanding financing options is crucial for potential homeowners looking to invest in a 3D printed home. The costs associated with these homes can differ significantly from traditional building methods. Therefore, adequate financial planning becomes essential. In this section, we will explore two primary avenues for financing: traditional mortgages and alternative financing methods that could better suit the unique needs of 3D printed housing projects.
Traditional Mortgages vs Alternative Financing
Traditional mortgages, while recognizable, may not always accommodate the specifics involved in 3D printed housing. Many lenders require standard appraisals and property valuations based on traditional homes, which can create complications. 3D printed houses may not always fit neatly into these categories, leading to potential hurdles in obtaining conventional loans.
However, some lenders are beginning to recognize the advancements in construction technology. They are starting to adjust their underwriting processes to include aspects unique to 3D printed homes. This adaptation can include evaluating the design and materials used, as opposed to strictly adhering to conventional valuation methods. Borrowers need to do thorough research to find lenders who are friendly towards innovative housing solutions.
On the other hand, alternative financing options offer unique benefits that may align better with the needs of buyers interested in 3D printed houses. Here are a few examples:
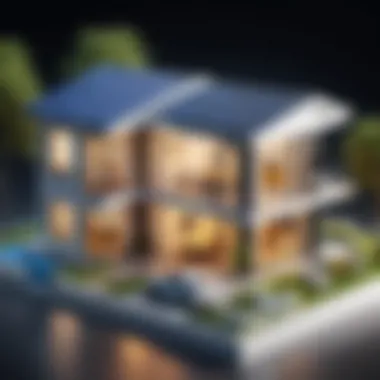
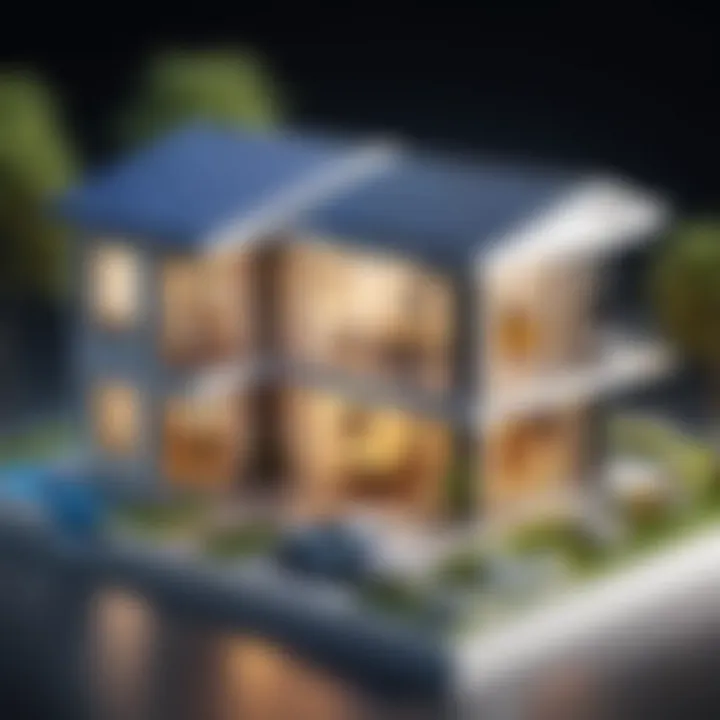
- Personal Loans: Some buyers may choose to finance their homes through personal loans. This option allows for individual negotiations regarding terms.
- Crowdfunding: Platforms for crowdfunding have emerged as a viable means of raising capital for housing projects. This method allows for investment from numerous sources, relieving the financial burden from a single entity.
- Partnerships with Developers: Collaborating directly with developers who specialize in 3D printed homes may open additional financing avenues. These partnerships can lead to cost-sharing arrangements.
Government Incentives and Grants
Governments are often keen to promote innovative building methods, especially those that offer sustainability and cost-efficiency. As a result, numerous government incentives and grants are available for 3D printed housing projects. These programs aim to reduce construction costs while encouraging new technology in the market.
Several incentives may reduce the overall financial burden. For instance:
- Tax Credits: Buyers may qualify for tax credits that lower their overall tax burden, making the purchase more affordable.
- Grants for Sustainable Practices: Some programs may provide grants to homeowners or builders who utilize eco-friendly materials or methods. This can also offset some of the initial costs of 3D printing technology.
- Low-Interest Loans: Certain government entities provide low-interest loans specifically for energy-efficient construction or innovative building technology. Accessing these funds can result in substantial savings over time.
Getting informed about available programs and grants can be beneficial. Checking with local housing authorities and governmental resources will enable potential buyers to gain insight into which financial assistance options may be accessible.
Future Trends in 3D Printed Housing
The future of 3D printed housing holds significant promise. As the technology evolves, it provides considerable benefits for the construction industry. Understanding these trends is crucial. Investing in this innovation will lead to better housing solutions. Technological advancements play a major role in shaping outcomes. Moreover, market dynamics will continually influence how 3D printed houses are perceived and adopted.
Technological Innovations on the Horizon
New technologies are emerging at a rapid pace. Developments in materials science are particularly noteworthy. Companies are working on stronger, more sustainable materials. For instance, innovations like bio-based polymers and composites will likely change how houses are constructed. These materials can reduce environmental impact and enhance durability.
Additionally, automated construction methods are becoming prevalent. Automation can lower labor needs and reduce overall costs. For example, robotic arms are now used in some projects to assist with material placement. This not only speeds up the process but also improves precision.
Other significant innovations include software advancements. Better design software helps architects create more complex structures. The push for customization in housing will grow. This aligns with consumer demand for unique living spaces. The integration of these technologies will pave the way for better-designed, better-built homes in the near future.
Predictions for Market Growth and Pricing
Market growth for 3D printed houses is projected to be substantial in the coming years. Analysts predict a significant increase in demand. This will be driven by the need for affordable housing solutions. The ability to create a house in a matter of days, rather than months, makes it an attractive option.
Pricing is another critical factor. As the technology becomes more mainstream, costs are expected to decline. Bulk production of the materials will lead to price reductions. Moreover, as more companies enter the market, competition will help to lower costs. This is beneficial not only for builders but also for consumers looking for affordable housing options.
In terms of geographical demand, urban areas will see more rapid adoption. The challenges of high construction costs in these regions make 3D printed solutions appealing. However, rural areas may experience a different trajectory. Accessibility and awareness of the technology will play a crucial role in adoption rates.
Overall, the evolving landscape of 3D printed housing is setting the stage for an exciting future.
"3D printing technology in construction is set to redefine how we think about building homes, paving the way for innovation and affordability."
Case Studies of 3D Printed Houses
Examining case studies of 3D printed houses sheds light on the practical implementation of this emerging technology in real-world scenarios. These examples highlight various projects that have successfully utilized 3D printing techniques, offering insights into the costs involved and the unique benefits that come from this innovative approach to construction. Through these studies, we can learn about the effectiveness of 3D printing in meeting housing needs, its impact on traditional building methods, and the scalability of the technology in various markets.
Such case studies are critical for understanding not only the financial implications but also the social and environmental factors contributing to the adoption of 3D printed housing.
Successful Projects and Their Costs
Several noteworthy projects have demonstrated the feasibility and cost-effectiveness of 3D printed houses. One prominent example is the Icon's 3D printed home in Austin, Texas. This project utilized concrete-based materials to construct a small house in less than 24 hours, resulting in a final cost that is significantly lower than traditional construction methods. The approximate cost of this unit was around $10,000, showcasing how 3D printing could drastically reduce housing expenses.
Another illustrative case is Apis Cor’s project, where they produced a 3D printed house in Russia within just 24 hours. The total investment for this project was notably low, illustrating the economic benefits of reduced labor and construction time.
Costs vary widely, of course, depending on factors like local materials, labor rates, and design specifications. Typical costs for 3D printed homes can range between $100,000 and $200,000, depending on size and design choices. This price point positions 3D printed houses as a competitive alternative in the affordable housing market.
Lessons Learned and Key Takeaways
From the analysis of successful case studies, several important lessons emerge regarding the 3D printing of houses:
- Cost Efficiency: One major takeaway is the significant cost savings associated with leveraging 3D printing technology. Reduced labor time and material waste are common benefits.
- Rapid Construction: Many projects report construction speeds of days rather than months. This efficiency addresses urgent housing shortages in various locations.
- Design Flexibility: 3D printed houses enable unique and customizable designs. This flexibility can meet specific needs and tastes without dramatically increasing costs.
- Sustainability: Many of these projects emphasize environmentally friendly materials and practices, making 3D printing a favorable option for environmentally conscious consumers.
"The potential of 3D printed houses lies not only in their affordability but also in their ability to address pressing housing crises with speed and efficiency."
In summary, case studies provide valuable data points that help industry stakeholders understand the cost dynamics and implications of adopting 3D printed housing solutions. By analyzing both successful projects and the lessons learned, one can gain a clearer picture of what to expect from this developing sector.
Finale
As we have seen, cost is influenced by many factors including materials, complexities of design, labor, and regional variations. Each of these elements plays a crucial role in the overall investment required for a 3D printed home. For potential homeowners and investors, comprehending these factors is vital in making informed decisions.
The benefits of 3D printed houses extend beyond mere cost considerations. They also introduce efficiency and sustainability to home construction. However, entering this market demands a clear grasp of both potential financial burdens and advantages. This knowledge can streamline the process of purchasing or financing a 3D printed house, allowing for better budget management.
Additionally, the future trends discussed earlier illustrate how market dynamics may evolve. Future predictions reveal that as technology progresses, costs may decline while the quality and variety of designs expand. This means that understanding current pricing structures can aid industry professionals in anticipating shifts that could affect their business models.
In closing, a careful analysis of costs associated with 3D printed houses provides a well-rounded view of what one should expect. It emphasizes the intersection of technology and construction, highlighting how developments in 3D printing could reshape housing options profoundly.
Your investment in understanding these facets could very well shape the housing market's future, offering not just opportunities but also challenges that require adequate preparation.