Unveiling the Wonders of Lincoln Plating: An In-Depth Exploration

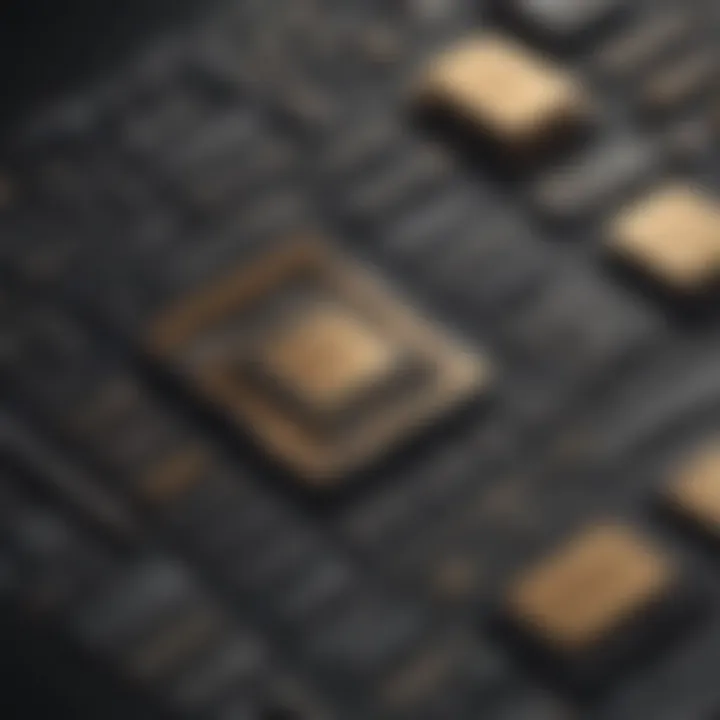
Tech Trend Analysis
Lincoln plating has emerged as a pivotal technology in various industries, including aerospace and automotive, due to its unparalleled durability and performance-enhancing capabilities. Manufacturers are increasingly adopting Lincoln plating to enhance the longevity and reliability of their products, reflecting a current trend towards utilizing advanced surface coating technologies. This trend signifies a shift towards more sustainable and efficient manufacturing practices, benefiting both companies and consumers.
Product Reviews
When delving into the realm of Lincoln plating, one cannot overlook its diverse range of features and specifications. From corrosion resistance to thermal conductivity, Lincoln-plated products boast exceptional properties that make them stand out in the market. A detailed performance analysis reveals that these products maintain their quality over extended periods, showcasing the effectiveness of Lincoln plating in ensuring longevity. However, like any technology, there are pros and cons to consider. While the durability of Lincoln-plated products is commendable, the initial investment cost may act as a barrier for some consumers. Despite this, the overall recommendation leans heavily towards the advantages Lincoln plating offers, making it a worthwhile investment for those seeking quality and longevity in their products.
How-To Guides
Introducing individuals to the intricacies of Lincoln plating requires a systematic approach. Step-by-step instructions are essential to grasp the application process and the nuances of maintaining Lincoln-plated surfaces. By providing tips and tricks on optimizing the benefits of Lincoln plating, users can harness its full potential in their respective industries. Troubleshooting common issues that may arise with Lincoln plating further enhances the user experience, ensuring a seamless integration of this technology into various applications.
Industry Updates
The landscape of the tech industry is constantly evolving, and Lincoln plating continues to make significant strides in innovation. Recent developments have focused on enhancing the sustainability of Lincoln plating processes, aligning with the industry-wide push towards eco-friendly solutions. Market trends indicate a growing demand for products incorporating Lincoln plating technologies, highlighting the impact it has on businesses and consumers alike. As companies adapt to these changes, the implications of Lincoln plating on the overall market dynamics are becoming more pronounced, presenting both challenges and opportunities for industry stakeholders.
Introduction to Lincoln Plating
Lincoln Plating is a revolutionary technique that has transformed the landscape of industrial surface treatments. Its significance lies in its ability to provide unparalleled durability and performance enhancements across various sectors. This article aims to delve into the intricate world of Lincoln Plating, shedding light on its applications, benefits, and technological advancements. By understanding the core principles and advantages over traditional plating methods, readers will gain a deeper insight into why Lincoln Plating has become a preferred choice in the manufacturing realm.
Understanding the Concept of Lincoln Plating
Historical Evolution
The historical evolution of Lincoln Plating traces back to its roots in addressing the limitations of conventional plating methods. Over time, continuous advancements have led to the development of more efficient and cost-effective techniques. The key characteristic of this evolution is its emphasis on improving surface finish quality and corrosion resistance. This evolution aligns with the ever-evolving demands of industrial processes, making Lincoln Plating a beneficial choice for modern applications. Its unique feature lies in the ability to enhance product longevity and performance, showcasing clear advantages over traditional plating methods.
Core Principles
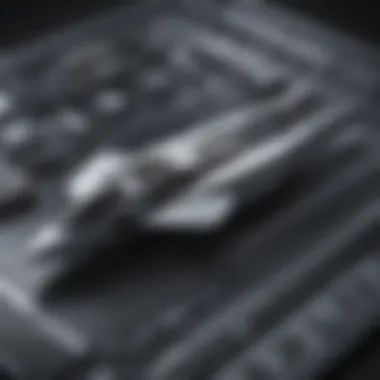
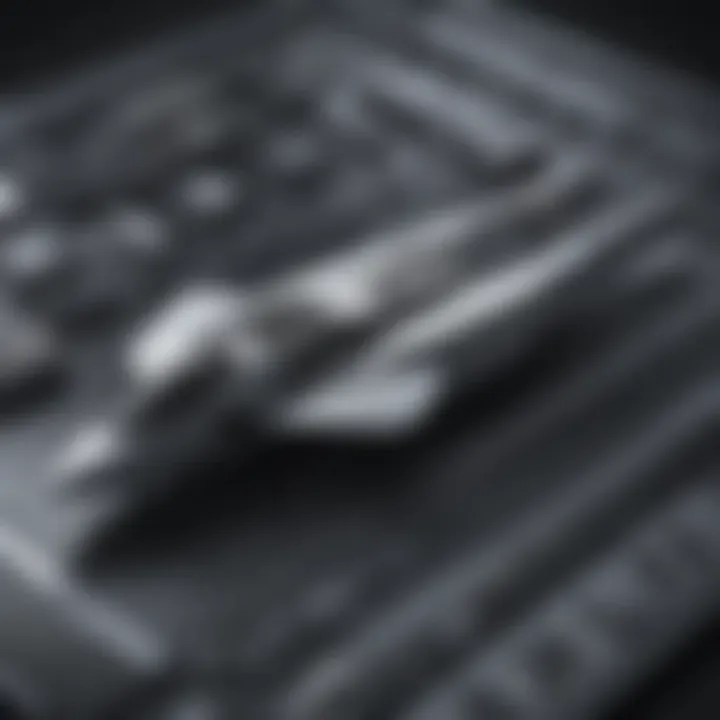
At the core of Lincoln Plating are principles grounded in precision and innovation. These principles drive the technique's efficacy in providing superior coating thickness control and adhesion properties. The key characteristic of these core principles is their focus on optimizing the plating process for maximum efficiency and quality. This approach proves to be a popular choice for industries seeking high-performance surface treatments. The unique feature of these core principles is their ability to tailor coatings to specific requirements, offering a level of customization that traditional methods lack.
Advantages Over Traditional Plating Methods
One of the standout features of Lincoln Plating is its superior advantages over traditional plating methods. By harnessing innovative technologies and processes, Lincoln Plating surpasses industry standards in terms of durability, corrosion resistance, and overall performance. The key characteristic here is the ability to achieve uniform coating thickness and coverage, ensuring optimal protection for various substrates. This advantage positions Lincoln Plating as a highly sought-after option for industries prioritizing longevity and quality in their products.
Applications Across Industries
Aerospace Sector
In the aerospace sector, Lincoln Plating plays a critical role in enhancing the structural integrity and longevity of components. Its ability to withstand extreme conditions and resist corrosion makes it a valuable asset in aerospace manufacturing. The key characteristic of Lincoln Plating in this sector is its lightweight yet robust coating that meets stringent industry standards. This benefit positions it as a popular choice for aerospace applications, offering unmatched protection and performance.
Automotive Industry
Within the automotive industry, Lincoln Plating finds extensive use in improving the durability and aesthetics of vehicle parts. Its excellent wear resistance and thermal management properties make it ideal for withstanding the rigors of automotive operations. The key characteristic here is its enhancement of overall product lifespan and performance under challenging environments. This advantage positions Lincoln Plating as a preferred choice for enhancing both the functionality and appearance of automotive components.
Medical Devices
The medical devices sector benefits greatly from Lincoln Plating's capability to provide biocompatible and sterile coatings. Its corrosion resistance and precise thickness control make it suitable for critical medical applications. The key characteristic of Lincoln Plating in this field is its ability to ensure product safety and reliability, meeting stringent regulatory requirements. This advantage highlights Lincoln Plating as a trusted solution for enhancing the longevity and performance of medical devices.
Technological Innovations in Lincoln Plating
Nanostructured Coatings
The introduction of nanostructured coatings in Lincoln Plating has revolutionized surface treatment technology. These coatings offer enhanced hardness and wear resistance, making them ideal for demanding industrial applications. The key characteristic of nanostructured coatings is their ability to provide superior protection at the nanoscale level, ensuring longevity and performance. This advantage positions nanostructured coatings within Lincoln Plating as a cutting-edge solution for industries requiring next-level surface treatments.
Enhanced Corrosion Resistance
Enhanced corrosion resistance is a hallmark of Lincoln Plating, achieved through advanced coating formulations and deposition techniques. This feature ensures the longevity and reliability of coated components in highly corrosive environments. The key characteristic of enhanced corrosion resistance is its ability to mitigate the impact of external factors on substrate materials, preserving their integrity over extended periods. This advantage solidifies Lincoln Plating as a top choice for industries facing challenging corrosion issues.
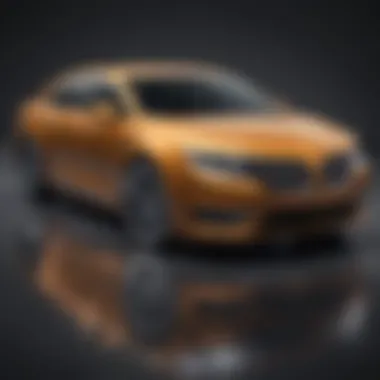
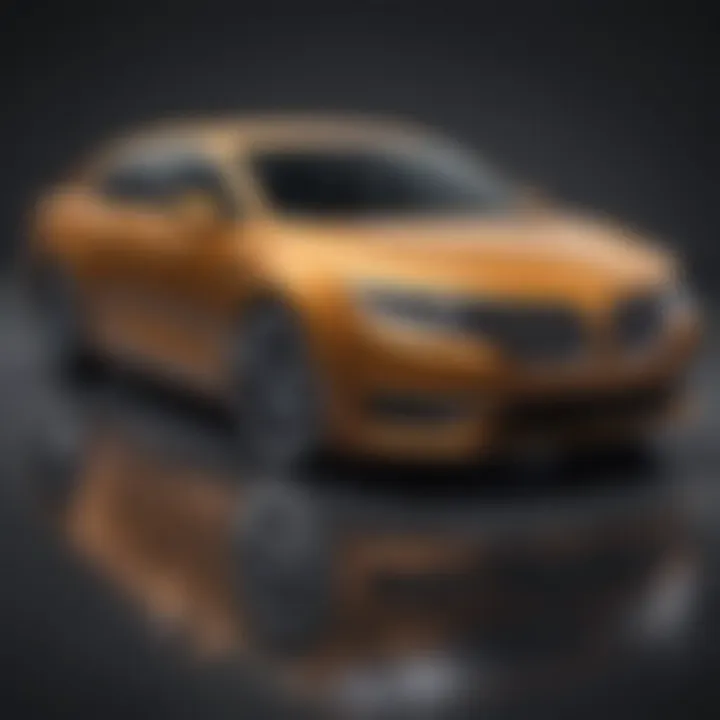
Electroless Plating Techniques
Electroless plating techniques represent a breakthrough in the field of surface treatments, offering efficient and uniform coating deposition without the need for an external power source. This innovation minimizes waste and maximizes coating integrity, enhancing the overall quality of plated components. The key characteristic of electroless plating techniques is their ability to coat complex geometries evenly and consistently, ensuring complete surface coverage. This advantage positions electroless plating techniques as a versatile and cost-effective solution within the realm of Lincoln Plating.
This meticulous exploration of Lincoln Plating showcases its intricate details, highlighting its unparalleled benefits and diverse applications across industries. By embracing technological innovations and optimizing core principles, Lincoln Plating continues to push the boundaries of surface treatment capabilities, paving the way for a more resilient and efficient manufacturing landscape.
Advantages of Lincoln Plating
Lincoln Plating boasts a myriad of advantages that position it as a pioneer in the plating industry. The sheer importance of these advantages is unparalleled, especially in high-demand sectors like aerospace and automotive industries. One of the key elements that set Lincoln Plating apart is its remarkable durability and longevity, revolutionizing the lifespan of products that utilize this technique. Additionally, Lincoln Plating excels in enhancing performance metrics, such as thermal management and electrical conductivity, providing a significant edge to products coated with this innovative plating method.
Durability and Longevity
Impact on Product Lifespan
The impact on the product lifespan is a critical aspect of Lincoln Plating's allure. By significantly extending the lifespan of treated products, Lincoln Plating ensures long-term robustness and sustainability. This unique characteristic plays a pivotal role in the overall performance and reliability of components, making them an ideal choice for industries that prioritize longevity and resilience. The enhanced product lifespan offered by Lincoln Plating is unmatched, underscoring the profound advantages it presents.
Resistance to Wear and Tear
Moreover, Lincoln Plating's remarkable resistance to wear and tear stands out as a hallmark feature. The ability to withstand and combat the detrimental effects of everyday usage elevates the durability of coated products to new heights. This innate resistance not only prolongs the usability of components but also reduces maintenance costs and downtime, presenting a cost-effective solution for industries. The impeccable resistance to wear and tear is a testament to Lincoln Plating's commitment to offering enduring quality.
Enhanced Performance
Improved Thermal Management
Lincoln Plating's improved thermal management capabilities play a crucial role in optimizing heat dissipation and regulation within components. This enhanced feature ensures better efficiency and performance, making products more reliable under varying temperature conditions. The ability to manage thermal loads effectively showcases Lincoln Plating's dedication to enhancing product functionality and longevity through innovative solutions.
Optimized Electrical Conductivity
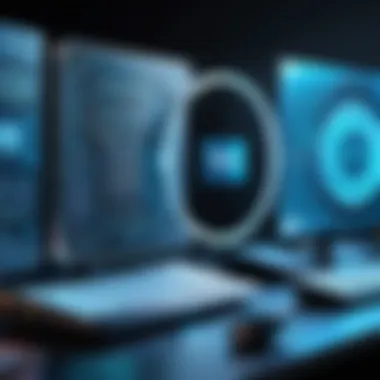
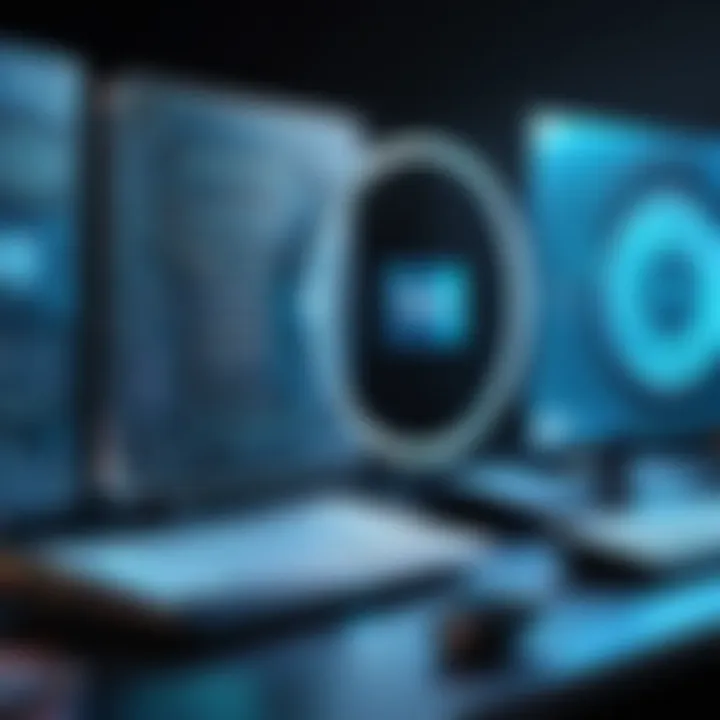
Furthermore, Lincoln Plating excels in optimizing electrical conductivity, a key factor in modern technology-driven industries. By enhancing the flow of electricity within coated components, Lincoln Plating improves overall performance and operational efficiency. This optimized electrical conductivity not only promotes better connectivity but also contributes to reducing energy loss, further solidifying Lincoln Plating's position as a frontrunner in the plating domain.
Future Prospects and Developments
In the realm of Lincoln plating, looking ahead to the future prospects and developments unveils an array of exciting possibilities and advancements that are set to revolutionize various industries. The continuous evolution of Lincoln plating techniques opens doors to innovative applications and enhanced performance across sectors. These developments not only promise greater efficacy but also underline the significance of staying abreast of the latest advancements in material coating technologies for sustained growth and competitiveness.
Innovative Applications of Lincoln Plating
Emerging Industries
Exploring the realm of emerging industries within the scope of Lincoln plating reveals a compelling narrative of growth and adaptation. These burgeoning sectors, ranging from renewable energy to electronic manufacturing, propel the integration of advanced plating technologies to meet evolving demands for enhanced quality and performance in products. The distinctive feature of Lincoln plating in emerging industries lies in its ability to cater to the unique requirements of niche markets, ensuring tailored solutions for specific applications. Embracing Lincoln plating in these sectors not only enhances product reliability but also fosters a culture of innovation and efficiency, thereby positioning them as frontrunners in their respective domains.
Research and Development Trends
Delving into the dynamic landscape of research and development trends associated with Lincoln plating sheds light on the driving forces behind continual improvement and innovation. The emphasis on exploring novel plating methodologies, materials, and processes underscores the commitment to pushing boundaries and enhancing the overall efficacy of Lincoln plating applications. The key characteristic of research and development trends is their pivotal role in shaping the future trajectory of material coating technologies, driving industry-wide advancements and setting new benchmarks for performance and sustainability. Despite facing challenges such as resource constraints and technological complexities, the perseverance in research and development endeavors ensures a steady march towards excellence and breakthroughs in Lincoln plating applications for diverse industrial sectors.
Environmental Sustainability
Within the realm of environmental sustainability, Lincoln plating emerges as a beacon of eco-conscious practices and solutions, aligning with the global imperative of minimizing ecological footprint and promoting green technologies. The advent of green plating technologies ushers in a new era of environmentally friendly coating processes that reduce waste, energy consumption, and harmful emissions, contributing to a healthier planet and ecosystem. The key characteristic of green plating technologies lies in their ability to deliver high-performance coatings while preserving environmental integrity, offering a sustainable alternative to conventional plating methods. Embracing green plating not only fulfills regulatory requirements but also exemplifies corporate responsibility and ethics, setting a precedent for conscientious manufacturing practices that prioritize planet preservation.
Recycling and Waste Management
In the domain of recycling and waste management, the integration of Lincoln plating techniques underscores a holistic approach towards mitigating environmental impact and promoting circular economy principles. By implementing efficient recycling processes and waste management strategies, industries can effectively recover valuable resources, minimize waste generation, and reduce environmental pollution associated with plating operations. The unique feature of recycling and waste management in Lincoln plating lies in their dual benefit of cost savings and environmental stewardship, offering a viable solution to optimize resource utilization and mitigate the ecological footprint of manufacturing processes. Engaging in responsible waste management practices not only safeguards natural resources but also cultivates a culture of sustainability and resilience, fostering a greener and cleaner industrial landscape.
This comprehensive guide on Lincoln plating's future prospects, innovative applications, and environmental sustainability showcases the pivotal role of material coating technologies in driving progress, efficiency, and eco-conscious practices across diverse industries.
Conclusion
In bringing our exploration of Lincoln Plating to a close, it is essential to reflect on the significance of this groundbreaking technique in various industries. This article has shed light on the versatile applications and numerous advantages that Lincoln Plating offers, from its role in enhancing product durability to optimizing performance metrics such as thermal management and electrical conductivity. By delving into its historical evolution, core principles, and technological innovations, we have unraveled the intricate tapestry of Lincoln Plating, showcasing its superiority over traditional plating methods. The future prospects and developments surrounding Lincoln Plating indicate a promising trajectory, with innovative applications emerging across industries and an increasing focus on environmental sustainability through green plating technologies and efficient waste management practices.
Summarizing the Impact of Lincoln Plating
Key Takeaways
Exploring the key takeaways of Lincoln Plating reveals its substantial impact on product quality and longevity. The durability and resistance to wear and tear provided by this plating technique significantly extend the lifespan of components, offering manufacturers a cost-effective solution for enhancing product performance and reliability. The advanced corrosion resistance and specialized nanostructured coatings exemplify the cutting-edge nature of Lincoln Plating, making it a preferred choice for industries requiring high levels of reliability and performance optimization. These key characteristics underscore the indispensable nature of Lincoln Plating in a competitive manufacturing landscape, where quality and durability are paramount.