Understanding Six Sigma: A Quality Management Guide


Intro
Six Sigma is a quality management framework that emphasizes the importance of data in decision-making processes. It originated in the manufacturing sector but has transcended industry boundaries over the years. Companies today use Six Sigma principles to improve efficiency, minimize errors, and enhance customer satisfaction. This article will delve into the nuances of Six Sigma, its methodologies, and its applications in various industries.
By understanding Six Sigma, newcomers and experts alike can appreciate its potential to drive organizational change. This framework is more than just a set of tools; it is a philosophy that encourages a culture of continuous improvement.
In what follows, we will break down the essential components of Six Sigma, including its origins, key methodologies, and practical applications in a business environment, arming you with the knowledge to navigate and implement Six Sigma strategies effectively.
Tech Trend Analysis
Overview of the current trend
In recent years, the demand for data-driven management practices has surged. Six Sigma fits seamlessly into this trend, as it combines statistical analysis with quality management techniques. Organizations are now increasingly recognizing the value of utilizing data to inform their operational strategies. The focus has shifted toward a culture that values precision and measurable outcomes, aligning perfectly with Six Sigma's core principles.
Implications for consumers
As businesses adopt Six Sigma methodologies, consumers stand to benefit significantly. Enhanced quality control leads to better products and services, which ultimately improves the overall consumer experience. Companies using Six Sigma can identify defects more quickly, reduce waste in production processes, and foster a more reliable supply chain. These improvements can translate into lower costs and higher value for consumers.
Future predictions and possibilities
Looking ahead, it is likely that Six Sigma will continue to evolve in response to technological advancements. Tools like big data analytics and machine learning can integrate with Six Sigma methodologies, making it even more effective. Companies may leverage these technologies to gain deeper insights into their processes, enabling them to react swiftly to changing market conditions and consumer preferences. This evolution could expand Six Sigma's applicability beyond traditional manufacturing and into sectors like healthcare, finance, and retail.
"The continual pursuit of analytics in decision-making processes is indicative of a larger trend toward operational excellence. Six Sigma embodies these principles, making it a relevant framework for modern business practices."
Principles of Six Sigma
Six Sigma is based on several key principles that guide its implementation. Understanding these principles is essential for anyone looking to grasp the framework fully:
- Customer focus: At its core, Six Sigma aims to meet or exceed customer expectations. Improving quality increases customer satisfaction and loyalty.
- Data-driven decisions: Decisions based on hard data improve the accuracy of outcomes. Statistical analysis distinguishes useful information from noise, aiding in effective decision-making.
- Prevention over detection: Rather than only finding faults, Six Sigma seeks to find ways to prevent defects from occurring in the first place.
- Collaboration and teamwork: Successful Six Sigma initiatives often depend on cross-functional teamwork, fostering a culture of collaboration and shared goals.
By internalizing these principles, organizations can effectively implement Six Sigma strategies.
Methodologies in Six Sigma
Several methodologies form the backbone of the Six Sigma framework. Most notably, the DMAIC and DMADV approaches are used for process improvement and design, respectively.
DMAIC
DMAIC stands for Define, Measure, Analyze, Improve, and Control. This methodology is often applied to existing processes to enhance performance. Here's how it breaks down:
- Define: Identify the problem and project goals.
- Measure: Collect relevant data to understand current performance.
- Analyze: Examine data to pinpoint root causes of defects.
- Improve: Develop and implement solutions to address identified issues.
- Control: Monitor improvements to ensure sustained performance over time.
DMADV
DMADV is primarily focused on designing new processes or products. It consists of:
- Define: Outline project objectives and customer requirements.
- Measure: Gather data on customer needs and specifications.
- Analyze: Compare and explore different design options.
- Design: Create and test designs that meet requirements.
- Verify: Ensure designs fulfill customer expectations through verification.
Both methodologies are crucial for organizations at various stages of operational maturity.
Finale
Understanding Six Sigma is vital for organizations aiming to enhance quality and efficiency. By embracing its principles and methodologies, businesses can drive meaningful changes in their operations. The future for Six Sigma looks promising, as its principles remain relevant in a rapidly evolving technological landscape.
Intro to Six Sigma
The introduction of Six Sigma serves as a critical foundation for understanding its relevance in quality management. This article aims to present not only the processes that Six Sigma entails but also its broad impact on organizations seeking to refine their operations. Emphasis is placed on how this framework harmonizes various methodologies to achieve excellence in operational efficiency.
Definition of Six Sigma
Six Sigma is a data-driven approach for eliminating defects in any process. It uses a set of quality management methods and creates a special infrastructure for these methods. The goal is to improve the processes by identifying and removing the causes of defects. Six Sigma is often represented by a statistical term that measures how far a given process deviates from perfection. Specifically, it aims to limit errors to no more than 3.4 per million opportunities. This essentially means striving for near perfection in process performance.
Importance in Quality Management
The importance of Six Sigma in quality management cannot be overstated. It provides a systematic methodology for enhancing operational processes, which directly contributes to increased customer satisfaction. Effective application of Six Sigma can lead to significant cost reductions, as organizations streamline their processes and eliminate waste.
Furthermore, Six Sigma builds a culture of continuous improvement. It encourages teams to focus on measurable results and to utilize data in their decision-making processes. This data-driven approach allows organizations to adapt quickly to changes and maintains a high quality standard in products and services.
Six Sigma methodologies help transform an organization’s approach to quality by fostering a climate of accountability and insisting on data-informed decisions.
Historical Context
Understanding the historical context of Six Sigma is vital for comprehending its current applications and significance in quality management. This section outlines its origins, evolution, and how it shaped the modern understanding of operational efficiency and quality practices in various industries. It emphasizes the need to appreciate past developments that inform contemporary methodologies, providing a more rounded perspective for practitioners and scholars alike.
Origins of Six Sigma
Motorola and the inception
Motorola played a pivotal role in the inception of Six Sigma in the 1980s. This company faced intense competition and high defect rates in its products. To combat this, Motorola introduced a structured, data-driven approach to quality improvement. The key characteristic of this initiative was its focus on minimizing defects to a rate of 3.4 defects per million opportunities. This was revolutionary and set a new standard for quality in manufacturing. The uniqueness of Motorola's approach lies in its rigorous methodology, which combined statistical analysis with practical applications. The advantages of this strategy include enhanced operational efficiency and improved customer satisfaction. Nevertheless, there were also challenges in adopting such a comprehensive framework, primarily due to the required cultural shift within the organization.
Early adoption in the industry
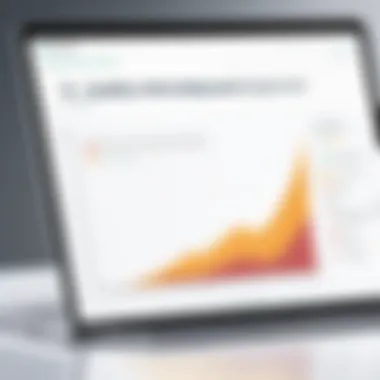

Following Motorola's initial success, other corporations began to adopt Six Sigma methodologies. Companies like General Electric expedited this trend, integrating Six Sigma principles into their operational processes. The notable characteristic of early adoption is the widespread recognition of the methodology as a significant driver of business transformation. This period marked the proliferation of Six Sigma as a key strategy for quality management across industries. Its unique feature was the adaptability of its principles to various sectors, from manufacturing to service-oriented businesses. The advantages included a broader scope of application, but the disadvantages included varying levels of commitment to training and implementation among companies.
Evolution of the Framework
Key milestones
The evolution of Six Sigma is characterized by several key milestones that demonstrate its growing importance in quality management. Initially, the methodology gained traction primarily in manufacturing sectors. However, over time, it reached various other domains such as healthcare and finance. Recognizing and celebrating these milestones is crucial, as they reflect the adaptive nature of Six Sigma. Each milestone has introduced new practices and refined existing ones, making it a continuous improvement strategy. A significant advantage of this evolution is the framework's ability to remain relevant in shifting market conditions. However, it can present challenges, as organizations may struggle to keep pace with evolving standards and practices.
Influential figures
Several influential figures have contributed to the development of Six Sigma, shaping its principles and broadening its application. Leaders like Jack Welch of General Electric championed its adoption, while experts such as W. Edwards Deming played a crucial role in advocating for statistical quality control. These figures not only demonstrated the effectiveness of Six Sigma but also influenced the mindset of many organizations. The key characteristic of these influencers lies in their ability to convey the importance of quality as a competitive advantage. Their contributions helped to cement Six Sigma's place in the modern business landscape. The unique feature of their involvement is their diverse backgrounds, showing that quality management is beneficial in various industries, although their methods might not yield immediate results.
Core Principles of Six Sigma
Understanding the core principles of Six Sigma is instrumental for anyone looking to implement effective quality management strategies. Six Sigma emphasizes the need for organizations to concentrate not just on reducing defects, but also on improving the processes that lead to those defects. Adopting these principles can facilitate a systematic approach to quality assurance, ensuring that organizations meet their goals and achieve customer satisfaction.
Focus on Customer Requirements
At the heart of Six Sigma lies a relentless focus on customer requirements. This principle underscores the importance of understanding what customers truly want and need from a product or service. Companies that prioritize customer input are better equipped to design processes that not only meet expectations but also exceed them.
Understanding customer requirements can be achieved through various methods including surveys, feedback forms, and direct interviews. When organizations incorporate this feedback into their processes, they can minimize waste and enhance value delivery.
"Customer satisfaction is the ultimate measure of a product's success."
Key aspects of focusing on customer needs include:
- Defining Critical to Quality (CTQ): Identifying specific attributes that are vital for customer satisfaction.
- Regular feedback loops: Continuously gathering and analyzing customer feedback to refine processes.
- Engaging stakeholders: All team members should understand customer needs and be engaged in meeting those needs.
Data-Driven Decision Making
In the realm of Six Sigma, decisions must be rooted in comprehensive data analysis. This data-driven approach allows organizations to make informed decisions rather than relying on intuition or anecdotal evidence. Collecting relevant data enables professionals to identify trends and patterns, contributing to a more accurate understanding of process performance.
Data can come from various sources such as:
- Operational databases
- Customer feedback mechanisms
- Market research findings
Organizations employ statistical tools such as control charts and predictive analysis to interpret data effectively. By leaning on quantitative metrics, businesses can pinpoint problem areas more accurately and implement solutions that are proven to work.
Process Improvement
The essence of Six Sigma is its dedication to continuous process improvement. By scrutinizing current systems and identifying inefficiencies, organizations can streamline their operations and enhance overall performance. This principle promotes an organizational culture where everyone is encouraged to seek ways to improve.
There are several methodologies that aid in sustained process improvement, including:
- DMAIC (Define, Measure, Analyze, Improve, Control): A structured problem-solving process used when current processes need enhancement.
- DMADV (Define, Measure, Analyze, Design, Verify): Focused on designing new processes or products to meet customer needs from the outset.
Implementing these methodologies helps organizations to:
- Reduce waste and inefficiencies
- Increase customer satisfaction
- Enhance employee engagement
Continuous improvement involves regular training and involvement of all employees, fostering a culture of quality that permeates the organization.
By integrating these core principles, organizations can advance their quality management practices and realize significant benefits. Focus on customer requirements, a commitment to data-driven decision making, and a dedication to process improvement are fundamental for any effective Six Sigma implementation.
Methodologies of Six Sigma
The methodologies of Six Sigma represent systematic approaches to quality management and improvement. Each focuses on enhancing efficiency and customer satisfaction. They guide organizations in analyzing processes, identifying issues, and implementing solutions. Understanding these methodologies is crucial for anyone seeking to leverage Six Sigma for operational excellence.
DMAIC Framework
The DMAIC framework is a fundamental aspect of Six Sigma. It stands for Define, Measure, Analyze, Improve, and Control. This structured approach is typically utilized for projects aimed at improving existing processes.
Define
The Define phase establishes the focus of the project. It seeks to outline the problem, project goals, and customer requirements. This phase is essential to ensure alignment among stakeholders. By clearly defining objectives, teams can avoid scope creep and stay focused on solutions. The key characteristic of Define is its emphasis on clarity and precision, enhancing project success.
Advantages include effective communication of objectives, while a challenge can be the difficulty in reaching consensus among all parties involved.
Measure
In the Measure phase, critical data related to the current process is collected. This data provides the basis for analysis. It is crucial because accurate measurements allow teams to understand performance levels and identify variations. A key characteristic of Measure is its focus on quantitative analysis. This is beneficial because it relies on factual data rather than assumptions. The unique feature of this stage is that it often employs various data collection techniques and tools, such as surveys or statistical software. While measurement is powerful, obtaining high-quality data can sometimes be resource-intensive.
Analyze
During the Analyze phase, the collected data is scrutinized to uncover root causes of defects. This stage is vital for understanding the factors that lead to variations. The key characteristic of Analyze is its reliance on statistical tools and techniques. This popular choice aids in identifying patterns and trends that may not be evident otherwise. Unique features include the use of tools like Pareto charts, which help prioritize issues effectively. However, a disadvantage can be the time required to conduct thorough analyses.
Improve
The Improve phase focuses on developing solutions. Teams brainstorm ideas to address identified issues and enhance processes. A central characteristic of Improve is its emphasis on creativity and innovation. This makes it a beneficial part of the DMAIC framework. The unique feature here is the use of pilot tests for proposed solutions before full implementation. This minimizes risks before broad changes are made. However, capturing and implementing all potential solutions can sometimes lead to overcomplication.
Control
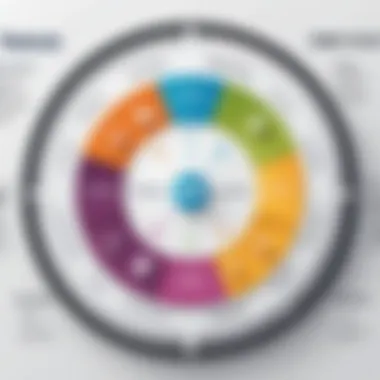

The final phase, Control, involves maintaining improvements over time. It ensures that any new processes are implemented consistently and successfully. A significant characteristic of Control is its focus on sustaining gains. This ensures that the benefits from the Improve phase do not diminish. Unique features include the development of standard operating procedures (SOPs) and monitoring systems. A disadvantage, however, is that it can require ongoing training and commitment from staff to maintain these improvements.
DMADV Framework
The DMADV framework focuses on designing new processes or products. It is particularly useful for creating high-quality products that meet customer demands. DMADV stands for Define, Measure, Analyze, Design, and Verify, guiding teams through a structured process for innovation.
Define
Define in the DMADV framework involves clarifying project objectives very early. This phase establishes consumer needs and long-term goals. Its key characteristic is its orientation towards customer satisfaction. This makes it a beneficial choice for companies looking to innovate. Its unique feature is the emphasis on collecting maximum information about market demands. However, failure to properly define needs can lead to misalignment with customer expectations.
Measure
Measure in this context focuses on quantifying customer needs and specifications. It seeks to gather data that can help in the design process. A key characteristic is that it involves deep market research. This is a beneficial choice, as it prioritizes a customer-centric approach. Unique features include using customer surveys and focus groups for direct feedback. Challenges may arise from interpreting data accurately or managing varying customer opinions.
Analyze
The Analyze phase evaluates the data gathered during measurement. It seeks to identify potential solutions for meeting customer requirements. The key characteristic of Analyze here is that it explores various design alternatives. This is beneficial because it fosters creative problem-solving. Unique features include brainstorming sessions and simulations. The disadvantage can stem from the complexity of analyzing numerous options thoroughly.
Design
Design involves creating the process or product that meets all outlined requirements. It incorporates feedback gathered in previous phases. A key characteristic of Design is its iterative nature. This is beneficial for refining ideas based on testing. The unique aspect includes incorporating prototype testing before finalizing a design. However, constant iterations might lead to fatigue among design teams if overdone.
Verify
Verify confirms that the final design meets customer needs and specifications. The aim is to ensure that what has been built or designed fits the expectations. The key characteristic is thorough validation practices, which are beneficial for quality assurance. Unique features include rigorous testing and validation processes. The challenge can be in the thoroughness; potential over-testing can delay project timelines.
Tools and Techniques
The implementation of Six Sigma hinges on the appropriate selection of tools and techniques. These tools are not merely supplementary; they are fundamental to understanding and analyzing processes. They provide a structured way to collect, measure, and interpret data, ensuring that quality improvement efforts yield meaningful results. Each tool comes with its own specific applications, and recognizing these can help organizations address their unique challenges effectively.
Statistical Tools
Statistical tools form the backbone of many Six Sigma initiatives, enabling teams to make data-driven decisions informed by solid evidence.
Control charts
Control charts are a powerful method for monitoring process variations over time. This tool allows teams to visualize whether a process is in control or not, providing immediate feedback on performance. A key characteristic of control charts is their ability to differentiate between common cause variation and special cause variation, which is essential for maintaining quality over time.
Control charts are often considered a beneficial choice for Six Sigma practitioners because they facilitate early detection of deviations from quality standards. A unique feature of control charts is the incorporation of upper and lower control limits, which help identify when a process may need intervention.
However, their effectiveness can be limited if data is not collected accurately or if users misinterpret the results. Maintaining the integrity of the data is critical for control charts to be truly effective in a quality management framework.
Process capability analysis
Process capability analysis assesses how well a process meets specified limits or criteria. This form of analysis quantifies the ability of a process to produce output consistently within these specifications. The key characteristic here is the capability indices, such as Cp and Cpk, which provide clear metrics for understanding process performance.
It is a beneficial tool for Six Sigma because it provides a quantitative measure of process capability, enabling teams to set realistic goals for improvement. One unique feature of process capability analysis is its focus on potential performance versus actual performance. This is crucial for continuous improvement efforts.
The drawback can be related to the necessity of having stable processes before analysis can yield meaningful insights. If a process is bumpy due to excessive variabilities, the capability indices may present an unrealistic picture of performance.
Quality Management Tools
Quality management tools complement statistical methods, giving insights on how to optimize processes while meeting customer satisfaction.
Pareto analysis
Pareto analysis is a technique used to identify the most significant factors in a dataset. The principle behind this tool is that a small number of causes often account for a large portion of the problem. A key feature of Pareto analysis is the creation of a Pareto chart, which visually represents the frequency or impact of problems in descending order.
This method is popular because it directs efforts to the areas that will yield the largest improvements, thus saving time and resources. The unique feature here lies in its emphasis on distinguishing the "vital few" from the "trivial many." However, its major disadvantage is that it might overlook less frequent issues that could also be significant over time.
Fishbone diagrams
Fishbone diagrams, also known as Ishikawa diagrams, are a visual tool used to systematically identify and present potential causes of a problem. They allow teams to delve deep into understanding the root causes of quality issues. A notable aspect of the fishbone diagram is its structured format, which arranges causes into categories—such as people, processes, materials, and environment.
This tool is beneficial because it encourages extensive brainstorming sessions, ensuring that all potential factors are considered. Its unique feature is that it not only displays the cause-and-effect relationships but also facilitates collaborative problem-solving among team members. On the downside, fishbone diagrams can become overly complicated if too many factors are included, which may overwhelm those involved in the analysis.
In summary, the choice of tools and techniques in Six Sigma will directly impact the quality management outcomes. Understanding their capabilities, limitations and applications ensures effective quality improvements.
Implementation of Six Sigma
The implementation of Six Sigma is crucial to the successful application of this quality management methodology. It encompasses several steps and considerations that ensure the framework is adopted effectively within an organization. By focusing on specific elements such as assessing organizational readiness and examining case studies, businesses can gain insights into the practical application of Six Sigma principles. The benefits of implementing Six Sigma include improved operational efficiency, higher customer satisfaction, and a culture centered on data-driven decisions. Understanding these elements allows organizations to harness the full potential of Six Sigma.
Organizational Readiness
Assessing culture
Culture plays a pivotal role in any organizational change. When assessing culture in the context of Six Sigma, leaders must recognize the attitudes and behaviors that pervade the workplace. A culture that embraces continuous improvement is essential for Six Sigma to thrive. This characteristic is beneficial as it fosters engagement and enthusiasm for quality initiatives. Organizations demonstrating strong support for change tend to adopt Six Sigma methods more readily.
One unique feature of assessing culture is the necessity for open communication. It creates transparency and encourages feedback among team members. The advantages here include enhanced teamwork and more effective problem-solving, while potential disadvantages might involve resistance from employees accustomed to traditional ways of working.
Training and certification
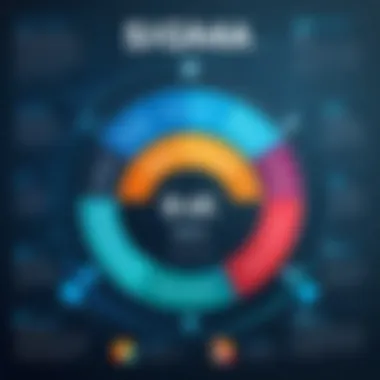

Training and certification are foundational aspects of implementing Six Sigma. Proper training ensures that team members possess the right skills to apply Six Sigma methodologies effectively. This characteristic is popular because it establishes a baseline competency among employees, which can lead to more successful project outcomes. Organizations that invest in training also tend to have higher engagement levels, as employees feel more empowered in their roles.
A unique feature of training and certification programs is their structured approach. They often include different levels, such as Yellow Belt, Green Belt, and Black Belt, each corresponding to specific skills and responsibilities. The advantages include providing clear pathways for career advancement, while disadvantages can arise when organizations do not offer enough support for continuous learning, thus leading to potential stagnation in skills.
Successful Case Studies
Examples from industry
Examples from various industries highlight the impact of Six Sigma on performance. Companies like General Electric and Toyota have successfully implemented Six Sigma solutions to improve their processes and operational efficiency. These cases exhibit the versatility of the method across sectors, from manufacturing to service industries. Such characteristics demonstrate Six Sigma’s applicability, making it a beneficial study topic for organizations seeking to enhance their own processes.
A unique feature of these real-world examples is their ability to showcase tangible results, such as reduced waste and increased quality. The advantages include learning from others’ successes and failures. However, disadvantages may stem from assuming that what worked for one company will automatically translate to different contexts.
Lessons learned
The lessons learned from Six Sigma implementations provide invaluable insights. Organizations can gain perspective on common challenges and effective strategies. This characteristic enhances the understanding of Six Sigma as a dynamic framework rather than a rigid set of instructions.
A unique feature of these lessons is their emphasis on the importance of sustained commitment. Without ongoing dedication to Six Sigma principles, initial gains can diminish quickly. The advantages of these insights include identifying pitfalls early and adapting strategies accordingly. Conversely, organizations must be cautious of overgeneralizing lessons, as each situation may yield different results and require tailored approaches.
Challenges and Limitations
Understanding the challenges and limitations of Six Sigma is crucial for achieving a successful implementation. Despite being a powerful framework designed to enhance quality and efficiency, Six Sigma is not without its obstacles. Identifying these hurdles is essential for organizations aiming to leverage the methodology effectively. It can prevent the misallocation of resources and support strategic planning.
One of the key aspects of this section is to highlight the potential barriers that can obstruct the successful use of Six Sigma. These barriers are not merely technical. They often encompass cultural, organizational, and psychological dimensions that can undermine efforts to instill a data-driven mindset. Moreover, the evolving landscape of industries presents its own set of challenges that organizations must navigate to integrate Six Sigma effectively.
Common Barriers to Implementation
Implementing Six Sigma can be met with multiple barriers that range from resistance among employees to insufficient leadership commitment. Some barriers are:
- Cultural Resistance: Employees might view Six Sigma as an additional burden, complicating their daily tasks rather than improving processes. This resistance can stem from a lack of understanding or fear of job loss.
- Limited Training: A common oversight is underestimating the need for training. If employees are not properly trained in Six Sigma methodologies, they may struggle to apply concepts in real-world scenarios.
- Inadequate Resources: Organizations might not allocate sufficient resources, be it time, capital, or personnel, to implement Six Sigma initiatives. This can lead to half-hearted applications that do not yield the desired results.
- Lack of Leadership Support: Without strong support from upper management, Six Sigma projects may not receive the necessary attention and prioritization, threatening their sustainability.
Addressing these barriers requires a committed approach along with a clear communication strategy that articulates the value of Six Sigma to both individuals and the organization as a whole.
Evolving Business Environments
The landscape in which organizations operate is continually changing. This evolution can significantly impact the application of Six Sigma. The emergence of new technologies, shifts in market dynamics, and changes in customer expectations mean that businesses must remain adaptable. Some important considerations are:
- Technological Disruption: As new technologies such as automation and artificial intelligence become integral to business operations, the principles of Six Sigma must adapt. Organizations may find that traditional data gathering methods are inadequate, necessitating the integration of advanced analytical tools.
- Dynamic Customer Demands: With the rise of instant gratification through digital platforms, customer expectations are evolving. Companies may have to modify their Six Sigma processes to remain competitive, often leading to more complex implementations.
- Globalization: Operating in a global market increases the complexity of process standardization. Variability in cultural norms, regulations, and business practices across regions can pose challenges to maintaining a consistent Six Sigma approach.
Adapting Six Sigma practices to these evolving conditions requires ongoing assessment and flexibility. Organizations must cultivate a mindset that anticipates change and embraces continuous improvement to effectively utilize the framework.
"Challenges and limitations are often the catalysts for innovation within Lean Six Sigma methodologies."
Future Trends in Six Sigma
Future Trends in Six Sigma emerging in today's fast-paced business world highlight a transformation that seeks to adapt and evolve the framework to current market demands. As organizations wrestle with increasing complexities, integrating new methodologies becomes crucial. Understanding these trends helps businesses to stay relevant and competitive. This section focuses on two significant aspects: Integration with Agile Practices and the Role of Technology in Six Sigma.
Integration with Agile Practices
The alignment of Six Sigma with Agile Practices signifies a crucial evolution in methodology. Agile focuses on flexibility, collaboration, and rapid iteration, while Six Sigma emphasizes data-driven decision-making and process improvement. Merging these philosophies enables organizations to respond quickly to changes in the market and customer needs without sacrificing quality.
- Agile methodologies encourage iterative improvements, while Six Sigma provides a robust framework for identifying and solving problems.
- This synergy allows teams to adapt their processes dynamically while utilizing Six Sigma's DMAIC or DMADV frameworks.
Businesses that integrate these practices often report enhanced project delivery speed and increased customer satisfaction. Agile teams can use Six Sigma tools, such as root cause analysis and process mapping, to identify inefficiencies within their sprints. This cross-utilization can lead to more precise and effective project outcomes.
Furthermore, involving cross-functional teams fosters a culture of quality that benefits from continuous feedback and learning. This transparency not only facilitates problem-solving but also nurtures innovation within organizations. Businesses may find that this combined approach offers a more comprehensive path to achieving operational excellence.
Role of Technology in Six Sigma
Technology is forging new paths for Six Sigma's implementation and effectiveness. The rise of data analytics, artificial intelligence, and automation is transforming traditional quality management practices. These advancements present opportunities to enhance decision-making processes.
- Advanced analytics can quickly process large datasets, providing insights that inform strategy and process design.
- Predictive analytics enhance Six Sigma's capability to foresee problems before they escalate, creating a proactive environment for quality management.
Toolsets such as cloud computing allow teams to collaborate in real-time, regardless of location. This accessibility ensures that all stakeholders can contribute valuable insights into the quality management process.
Machine learning algorithms can analyze patterns and recommend optimizations which further streamline processes. Thus, technology not only amplifies the capabilities of Six Sigma but also aligns them with modern organizational needs. As the integration of technology continues to evolve, firms that embrace these trends can drive significant improvements in their quality management efforts.
"Innovation and technology are key drivers in the evolution of Six Sigma, enabling organizations to maximize efficiency and quality through data-driven insights."
In summary, the future of Six Sigma lies in its adaptability through integration with Agile practices and increasing reliance on advanced technologies. Organizations that embrace these trends will be better positioned to navigate the complexities of modern business environments.
Epilogue
The conclusion of this article serves as a vital component in summarizing the essential ideas related to Six Sigma. It encapsulates the various insights gained from understanding the framework, emphasizing the significance it holds in today’s business operations. By reinforcing the key elements covered throughout the sections, the conclusion provides clarity on the important aspects of Six Sigma, including its methodologies, principles, and the integral tools that facilitate its successful implementation.
Summation of Key Insights
In this article, key insights about Six Sigma emerged, highlighting its nature as a data-driven approach to quality management. The importance of focusing on customer requirements, coupled with the necessity for data-driven decision-making, cannot be overstated. Organizations that incorporate these principles often experience improved operational efficiency and enhanced product quality.
Moreover, the methodologies, including DMAIC and DMADV, provide structured frameworks to tackle process improvement and innovation respectively. The diversity of tools like control charts and Pareto analysis supports organizations in identifying areas for improvement and tracking progress efficiently. Understanding these tools enables industry professionals to apply Six Sigma effectively in their businesses.
Final Thoughts on Six Sigma
Six Sigma stands as a potent framework in the realm of quality management. Its ability to adapt to various industries and circumstances underscores its versatility. As businesses continuously strive for greater efficiency and quality, the principles of Six Sigma remain relevant and critical. The future of Six Sigma may involve integration with agile practices and advancing technologies, ensuring that it evolves with the changing landscape of industry demands. Thus, for professionals committed to quality management, embracing Six Sigma not only enhances their organizational capabilities but also ensures they are well-positioned for future challenges in their respective fields.
"Embracing Six Sigma is not just about quality control; it is about fostering a culture of continuous improvement and operational excellence."
This framework offers a comprehensive guide to navigating the complexities of quality management, making it a necessary aspect for any organization aiming to excel.