Revolutionizing Manufacturing: Breakthrough in 3D Printing Large Objects in Segments
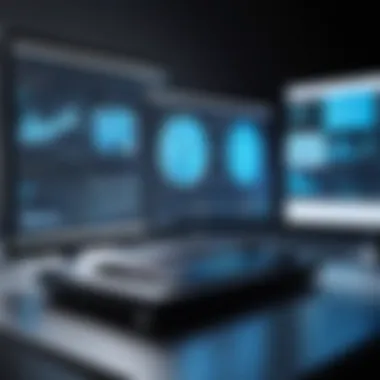
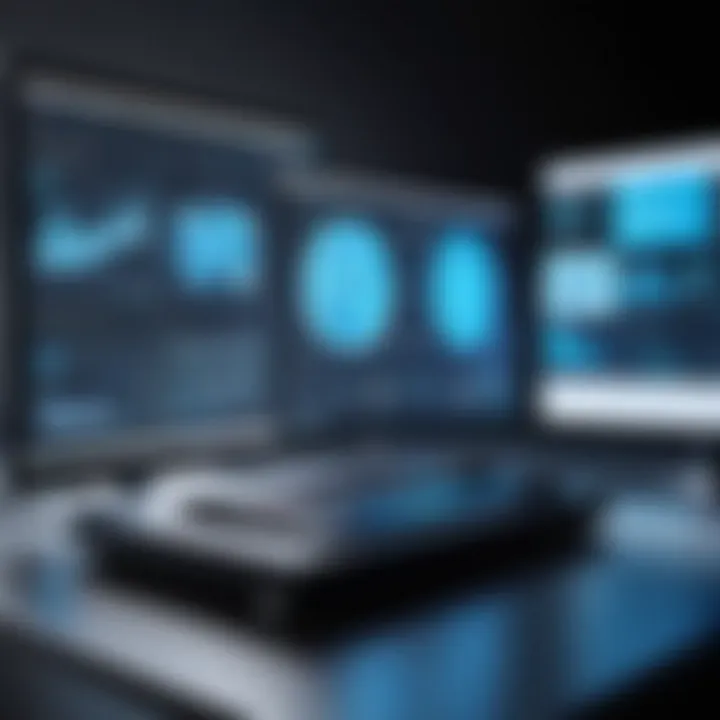
Tech Trend Analysis
The modern landscape of manufacturing is witnessing a remarkable shift towards the groundbreaking technique of 3D printing large objects in segmented parts. This innovative approach has captivated the attention of industry players and enthusiasts alike, sparking curiosity and excitement for the endless possibilities it presents. Offering a cost-effective and efficient solution to conventional manufacturing limitations, 3D printing in parts not only revolutionizes production processes but also opens up new creative avenues for designers and engineers.
Product Reviews
In the realm of additive manufacturing, the concept of printing large objects in segmented parts introduces a paradigm shift in product development and fabrication. By dissecting complex structures into manageable components, manufacturers can streamline production workflows and reduce costs significantly. The key features and specifications of 3D printers designed for large-scale object printing are essential for understanding their capabilities and limitations. Performance analysis delves into the intricacies of output quality, assembly precision, and material compatibility, while evaluating the overall feasibility and practicality of implementing this method in different industrial settings.
How-To Guides
Embarking on the journey of 3D printing large objects in parts necessitates a comprehensive understanding of the fundamental principles and protocols involved in this transformative process. An introduction to the topic serves as the gateway to exploring the intricacies of segmentation techniques, structural optimization, and assembly methodologies. Step-by-step instructions guide practitioners through the nuanced steps of preparing, printing, post-processing, and assembling segmented parts, emphasizing meticulous attention to detail and precision. Tips and tricks from experienced professionals offer invaluable insights and best practices for mitigating common challenges and enhancing efficiency in large-scale object production. Troubleshooting guidelines equip enthusiasts and industry professionals with the necessary skills to identify and resolve common issues that may arise during the printing and assembly stages, ensuring a smooth and successful workflow.
Industry Updates
The dynamic landscape of the tech industry is constantly evolving, with recent developments in additive manufacturing technologies reshaping the conventional paradigms of production and design. Analyzing market trends and industry updates provides crucial insights into the current state of 3D printing applications, emerging materials, and innovative approaches driving progress in the manufacturing sector. The impact of these advancements on businesses and consumers underscores the transformative potential of 3D printing large objects in parts, heralding a new era of customization, efficiency, and creativity across diverse industries.
Introduction
In the realm of modern manufacturing, a groundbreaking shift has emerged: the revolutionary technique of 3D printing large objects in segmented parts. This article embarks on a detailed exploration of this innovative approach, shedding light on its inherent benefits and wide-ranging applications. By dissecting the traditional manufacturing process into manageable segments, manufacturers can now achieve remarkable results in creating complex and sizable structures, pushing the boundaries of what was once deemed impossible.
Understanding 3D Printing
History of 3D Printing
Unraveling the historical tapestry of 3D printing unveils a rich tapestry of technological evolution. From its nascent stages to the present day, the history of 3D printing underscores the gradual progression towards precision and efficiency in manufacturing. The key characteristic of this historical journey lies in the gradual democratization of advanced manufacturing technologies, offering a transformative path for economies and industries alike.
Basic Principles of 3D Printing
Delving into the fundamental principles of 3D printing illuminates the core essence of this cutting-edge technology. The intricate interplay of design, material selection, and printing processes forms the bedrock of efficient 3D production. Recognizing the pivotal role of these basic principles underscores their significant contribution to optimizing manufacturing processes and enhancing product quality.
Evolution of 3D Printing Technology
The dynamic evolution of 3D printing technology heralds a new era in manufacturing possibilities. Advancements in additive manufacturing techniques, materials science, and design methodologies have revolutionized the landscape of production. This evolution showcases the relentless pursuit of innovation to tackle complex challenges and drive continuous improvement in manufacturing practices.
Challenges of 3D Printing Large Objects
Limitations in Size and Scale
Navigating the constraints posed by size and scale in 3D printing unveils a myriad of engineering challenges. Balancing design intricacies with structural stability remains a critical consideration in manufacturing large objects. The key characteristic of managing size limitations underscores the importance of creative solutions and strategic planning for optimal production outcomes.
Structural Integrity Concerns
Addressing concerns regarding structural integrity delves into the core principles of material science and engineering precision. Ensuring the durability and robustness of printed components demands meticulous attention to detail and rigorous quality control measures. The unique feature of structural integrity underscores the critical importance of meeting stringent industry standards and safety protocols.
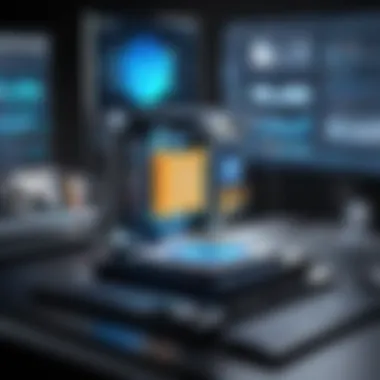
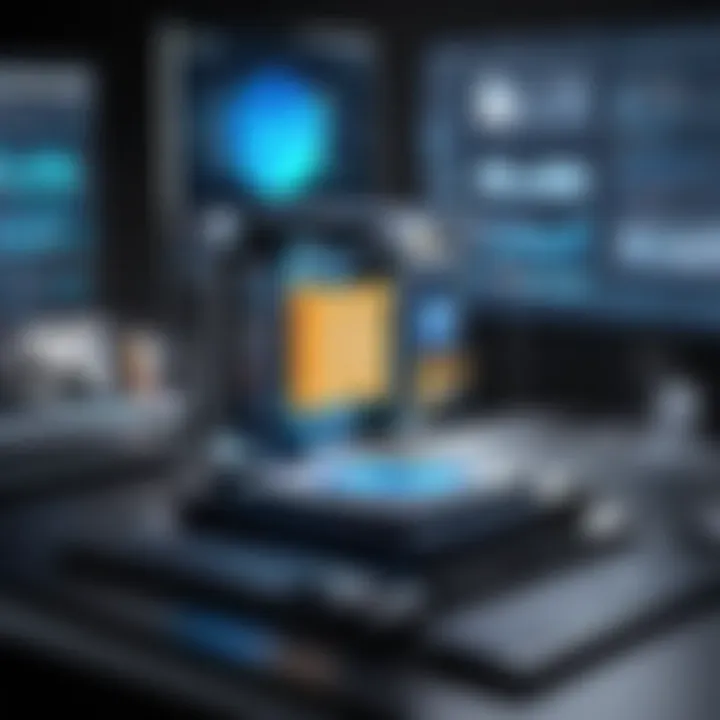
Time and Cost Implications
Nurturing a comprehensive understanding of the time and cost implications associated with 3D printing is imperative for informed decision-making. Balancing production timelines with financial considerations forms the cornerstone of sustainable manufacturing practices. The focal point of time and cost implications emphasizes the need for efficiency optimization and cost-effective strategies to maximize operational effectiveness.
The Concept of Printing in Parts
Benefits of Printing Large Objects in Parts
Unveiling the advantages of printing large objects in segmented parts showcases a transformative approach to manufacturing complex structures. Embracing modular construction methodologies enhances flexibility and customization possibilities, catering to diverse production requirements. The key characteristic of segmenting large objects underscores the practical benefits of reduced wastage and enhanced design adaptability.
Optimizing Design for Part Printing
Fine-tuning design strategies for part printing elevates the production process to new heights of precision and efficiency. Leveraging advanced design software and optimization tools streamlines the manufacturing workflow, enhancing product quality and consistency. The essence of optimizing design for part printing lies in unlocking innovative design potentials and unleashing creative freedom in product development.
Assembly and Integration Strategies
Crafting seamless assembly and integration strategies embodies the art of harmonizing individual components into a cohesive whole. Meticulous planning and execution play a crucial role in ensuring precision alignment and structural integrity in the final product. The unique feature of assembly and integration strategies underscores the significance of strategic planning and collaborative efforts in achieving manufacturing excellence.
Benefits of Printing Large Objects in Parts
Delving into the realm of revolutionizing manufacturing, the process of 3D printing large objects in segmented parts unveils a groundbreaking approach that challenges traditional production norms. By dissecting the creation of these monumental objects into manageable components, manufacturers can attain unparalleled results, culminating in the metamorphosis of the conventional manufacturing landscape. Embracing this innovative technique opens doors to intricate designs and intricate structures previously deemed unattainable. The strategic division of large objects into parts brings forth enhanced customization, flexibility, precision, quality, cost-efficiency, and scalability. Each element plays a pivotal role in reshaping the manufacturing domain, offering a paradigm shift in production methodologies.
Enhanced Customization and Flexibility
Tailoring Designs to Specific Requirements
Within the scope of tailoring designs to specific requirements lies the crux of customizability. This facet of the 3D printing process caters to precise specifications, allowing for the adaptation of designs to meet unique demands and characteristics. The ability to tailor the structure seamlessly weaves innovation with practicality, resulting in bespoke creations that transcend traditional boundaries. Tailoring designs to specific requirements grants manufacturers the freedom to craft objects with meticulous attention to detail, facilitating the realization of intricate shapes and functionalities. While the process embodies a transformative approach to manufacturing, it also poses challenges in terms of scalability and material considerations, underscoring the intricacies involved in achieving tailored perfection.
Iterative Prototyping Possibilities
Navigating the terrain of iterative prototyping possibilities presents a realm of continuous refinement and iteration. This aspect of the 3D printing methodology enables manufacturers to engage in a cyclical process of design enhancement, fostering creativity and innovation at every stage. Iterative prototyping signifies a progressive approach to product development, allowing for rapid adjustments and modifications based on real-time feedback. As a cornerstone of efficiency and precision, this practice elevates the quality standards of manufacturing processes, albeit not without complexities regarding resource allocation and time management. Harnessing the potential of iterative prototyping paves the way for dynamic product evolution and adaptation, heralding a new era of agility and adaptability within the manufacturing sphere.
Modular Structures and Component Replacements
Exploring the realm of modular structures and component replacements unveils a realm of adaptability and versatility. This specific aspect of 3D printing underlines the modularity inherent in creating complex objects through interchangeable components, emphasizing flexibility and scalability. The construction of modular structures allows for seamless integration and assembly, enabling manufacturers to construct intricate objects with ease. By facilitating component replacements, this approach streamlines maintenance and repair processes, promoting sustainability and longevity. However, the implementation of modular structures and component replacements necessitates meticulous planning and design foresight to ensure seamless integration and optimal functionality.
Improved Precision and Quality
Reduced Material Waste
In the domain of reduced material waste lies a fundamental pillar of sustainability and efficiency. This particular facet of the 3D printing methodology emphasizes resource optimization and waste minimization, aligning production processes with environmentally conscious practices. By harnessing innovative techniques and design principles, manufacturers can significantly reduce material wastage while enhancing productivity and cost-effectiveness. The concept of reduced material waste champions responsible manufacturing practices, albeit with challenges related to material selection and process optimization. Embracing this aspect of precision manufacturing propels industries towards greener and more sustainable production paradigms, marking a paradigm shift towards conscientious manufacturing practices.
Minimized Defects and Errors
Navigating the realm of minimized defects and errors heralds a new era of quality assurance and reliability. This nuanced aspect of the 3D printing process prioritizes error prevention and defect mitigation, ensuring that each manufactured object meets stringent quality standards. By integrating advanced quality control measures and algorithms, manufacturers can detect and rectify errors in real-time, safeguarding production timelines and deliverable quality. Minimizing defects and errors signifies a commitment to excellence and precision in manufacturing, albeit presenting challenges in terms of technology integration and system complexity. This dedication to quality assurance underscores a commitment to customer satisfaction and product integrity, positioning manufacturers at the forefront of quality-driven production methodologies.
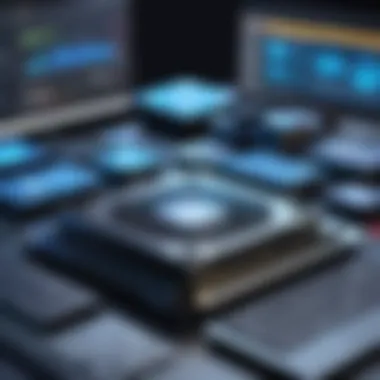
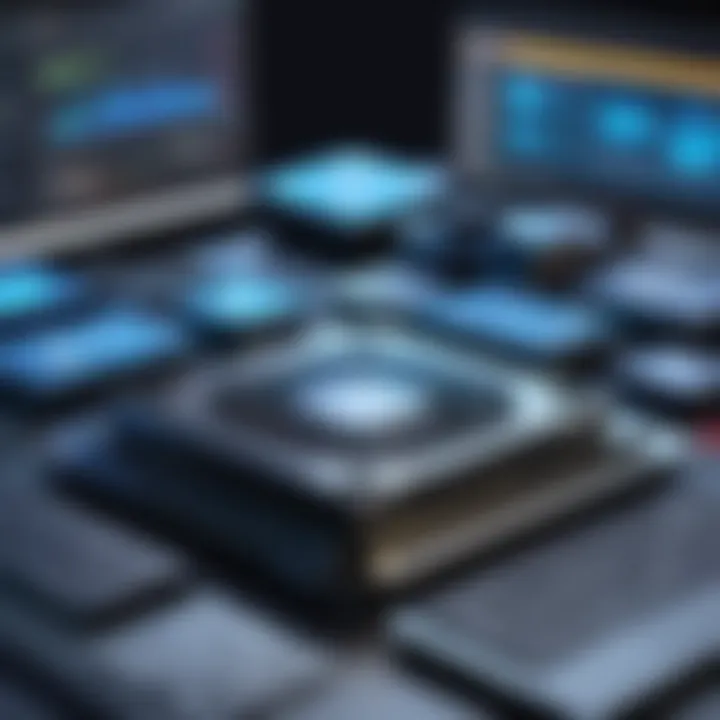
High-Quality Surface Finishes
Exploring the intricacies of high-quality surface finishes reveals the transformative impact of aesthetic appeal and functional excellence. This critical aspect of 3D printing underscores the significance of surface texture and finish quality in enhancing product aesthetics and performance. By leveraging advanced finishing techniques and post-processing methodologies, manufacturers can achieve immaculate surface quality and tactile satisfaction. The pursuit of high-quality surface finishes demands meticulous attention to detail and professional craftsmanship to ensure consistency and uniformity across all manufactured components. While the quest for perfection in surface finishes presents challenges related to time and resource allocation, the result is a testament to the dedication to excellence and visual appeal prevalent in contemporary manufacturing practices.
Applications of 3D Printing Large Objects in Parts
In the realm of modern manufacturing, the concept of 3D printing large objects in segmented parts has emerged as a revolutionary technique with profound implications. This article delves into the significance of incorporating this advanced approach, shedding light on its intricate elements, benefits, and critical considerations. By dissecting the conventional manufacturing process into manageable segments, manufacturers can unlock a plethora of advantages, pushing the boundaries of what is achievable in the industry.
Aerospace and Automotive Industries
Prototyping Complex Components
Delving into the intricacies of prototyping complex components within the aerospace and automotive industries unveils a realm of innovation and efficiency. The meticulous process of prototyping intricate parts serves as a driving force behind the overall goal of elevating manufacturing standards. The defining characteristic of prototyping complex components lies in its ability to streamline the product development phase significantly, offering manufacturers a rapid and accurate method for testing new designs. This strategic choice proves highly beneficial in the context of this article, as it expedites the production timeline while ensuring precision and performance standards are met. Despite its advantages, it is essential to acknowledge potential drawbacks, such as increased costs associated with intricate prototypes.
Customizable Tooling and Fixtures
The integration of customizable tooling and fixtures marks a pivotal advancement within the aerospace and automotive sectors, fostering agility and adaptability in the production process. A key attribute of customizable tooling and fixtures is their versatility, allowing manufacturers to tailor production setups to specific requirements swiftly. This flexibility proves instrumental in the context of the article, as it paves the way for enhanced customization and efficiency. However, it is crucial to note that while customization offers manifold benefits, complex adjustments may lead to operational disruptions if not executed meticulously.
Lightweight Structural Elements
The realm of lightweight structural elements stands at the forefront of innovation within aerospace and automotive applications, emphasizing efficiency and performance. The primary allure of lightweight structures lies in their ability to reduce overall weight burdens without compromising structural integrity, thus enhancing fuel efficiency and overall performance metrics. In the scope of this article, the emphasis on lightweight structural elements underscores a paradigm shift towards sustainable and high-performance design solutions. While the advantages are clear, it is important to navigate potential challenges related to material limitations and cost implications effectively.
Architecture and Construction
Creating Large-Scale Models
The creation of large-scale models represents a cornerstone in architectural and construction endeavors, offering a tangible representation of complex designs. Large-scale models serve as invaluable tools for visualizing architectural concepts on a grand scale, enabling stakeholders to grasp spatial relationships and intricate details effectively. Within this article, the significance of creating large-scale models lies in its ability to foster clear communication and design validation, streamlining the construction process. Despite its benefits, challenges may arise concerning time constraints and resource allocation, underscoring the need for meticulous planning and execution.
On-Site Assembly and Integration
The integration of on-site assembly and integration methodologies reshapes traditional construction paradigms, emphasizing efficiency and coherence in project execution. The key characteristic of on-site assembly and integration is its capacity to synchronize multiple construction phases seamlessly, minimizing delays and optimizing resource utilization. This strategic choice aligns closely with the narrative of this article, highlighting the importance of efficient assembly strategies in enhancing overall project outcomes. It is vital to acknowledge that while on-site assembly offers remarkable advantages, logistical complexities and site-specific challenges may demand adept problem-solving skills to navigate successfully.
Architectural Detailing and Ornamentation
Architectural detailing and ornamentation present a realm of creative opportunities within architectural and construction domains, accentuating aesthetic appeal and design sophistication. The prominent feature of architectural detailing and ornamentation is its ability to infuse spaces with character and visual interest, elevating architectural narratives to new heights. In the context of this article, the emphasis on architectural detailing and ornamentation underscores the significance of bespoke design elements in captivating and inspiring built environments. While the advantages are compelling, considerations must be made regarding material durability and long-term maintenance to ensure design integrity is upheld.
Medical and Healthcare Sector
Patient-Specific Implants
The realm of patient-specific implants heralds a new era of customization and precision within the medical and healthcare sector, catering to individual patient needs with unparalleled accuracy. The key characteristic of patient-specific implants lies in their tailored design, ensuring optimal fit and functionality for each patient's unique anatomy. This targeted approach significantly enhances patient outcomes and comfort levels, reflecting a patient-centric model of care. Within the context of this article, the focus on patient-specific implants underscores the transformative impact of 3D printing technology in personalized healthcare solutions. While the benefits are noteworthy, challenges may arise concerning regulatory compliance and quality assurance protocols, necessitating stringent adherence to industry standards.
Customized Prosthetics
The integration of customized prosthetics exemplifies a paradigm shift in prosthetic design and production, emphasizing individualized solutions for patients with limb differences. The defining feature of customized prosthetics lies in their tailor-made construction, precisely conforming to the user's unique limb structure and functional requirements. This bespoke approach offers users enhanced comfort, mobility, and functionality, enhancing their quality of life significantly. In the purview of this article, the spotlight on customized prosthetics underscores the human-centric ethos driving advancements in medical technology. However, considerations must be made regarding scalability and access to ensure widespread adoption and affordability of customized solutions.
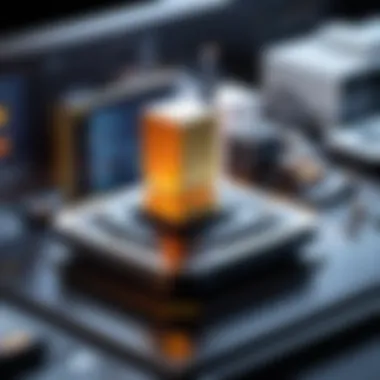
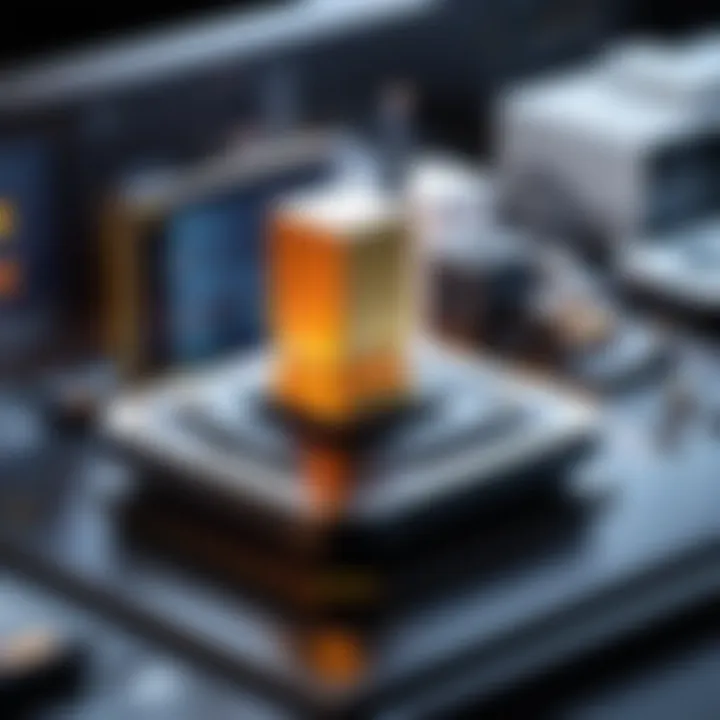
Biomedical Research Models
The utilization of biomedical research models stands as a cornerstone in advancing scientific discovery and medical innovation, providing researchers with accurate representations for experimentation and analysis. The crucial characteristic of biomedical research models is their fidelity to physiological structures, enabling researchers to simulate complex biological functions and pathologies effectively. This sophisticated modeling approach accelerates research initiatives, leading to breakthroughs in medical treatments and therapies. Within the narrative of this article, the emphasis on biomedical research models underscores the invaluable role of 3D printing in pushing the frontiers of medical knowledge. Despite the undeniable advantages, challenges may surface in terms of scalability and ethical considerations, necessitating ethical frameworks and attention to data privacy and security.
Future Trends and Innovations
In the realm of 3D printing, future trends and innovations play a pivotal role in steering the course of manufacturing towards greater efficiency and sophistication. Embracing advancements in material science, integration of Io T, and AI technologies, along with global adoption and standardization, propels the industry towards unprecedented possibilities. One of the key drivers of evolution within this domain is the constant refinement and expansion of materials used in additive manufacturing processes, setting the stage for groundbreaking developments.
Advancements in Material Science
Development of High-Performance Polymers
The development of high-performance polymers marks a significant stride in enhancing the capabilities of 3D printing. These polymers offer exceptional durability, heat resistance, and mechanical strength, making them ideal for a wide array of industrial applications. Their versatility and resilience make them a preferred choice for creating intricate and resilient components in additive manufacturing. Despite their advantages, the challenge lies in optimizing printing parameters to maximize their properties without compromising print quality.
Metal and Composite Material Integration
The integration of metals and composites into 3D printing processes heralds a new era of manufacturing possibilities. By combining the strength of metal alloys with the design flexibility of composites, manufacturers can produce lightweight yet robust components with tailored properties. This integration opens doors to applications requiring high structural integrity and complex geometries, revolutionizing industries such as aerospace and automotive.
Bio-Compatible and Sustainable Options
Advancements in material science have paved the way for bio-compatible and sustainable materials to enter the 3D printing arena. These eco-friendly options reduce environmental impact while meeting stringent safety standards for medical and consumer applications. From biodegradable polymers to recycled composites, the adoption of sustainable materials aligns with the industry's shift towards eco-conscious practices, driving innovation towards a greener future.
Integration of Io
T and AI Technologies
Smart Manufacturing Processes
Incorporating Io T and AI technologies empowers smart manufacturing processes, enabling real-time data analysis, predictive maintenance, and adaptive production. The seamless connectivity between machines optimizes workflow, enhances efficiency, and ensures quality control at every stage of manufacturing. By harnessing the power of data analytics and machine learning, manufacturers can streamline operations, reduce downtime, and improve overall productivity.
Real-Time Monitoring and Quality Control
Real-time monitoring and quality control systems provide instant insights into production processes, allowing for quick decision-making and corrective actions. By monitoring key performance indicators in real-time, manufacturers can identify deviations from quality standards and implement necessary adjustments promptly. This proactive approach minimizes defects, reduces waste, and upholds product consistency, bolstering customer satisfaction and operational excellence.
Predictive Maintenance Techniques
Predictive maintenance leverages AI algorithms to forecast equipment failures before they occur, enabling preemptive maintenance interventions. By analyzing machine data and performance metrics, predictive maintenance systems can predict potential issues, schedule maintenance activities, and prevent costly breakdowns. This proactive maintenance approach maximizes equipment uptime, extends asset lifespan, and optimizes operational efficiency, fostering a reliable and sustainable manufacturing environment.
Global Adoption and Standardization
Regulatory Frameworks and Compliance
Adhering to regulatory frameworks and industry standards is imperative for ensuring product quality, safety, and compliance. Regulatory compliance guarantees that manufacturing processes meet legal requirements and adhere to quality standards, safeguarding consumer interests and industry reputation. By upholding regulatory mandates and certifications, manufacturers demonstrate their commitment to ethical practices, product integrity, and customer trust.
Industry Collaboration Initiatives
Collaborating with industry partners and stakeholders fosters innovation, knowledge sharing, and collective growth within the manufacturing ecosystem. Industry collaboration initiatives facilitate the exchange of ideas, resources, and best practices, fueling synergistic advancements and transformative developments. By engaging in strategic partnerships and collaborative projects, manufacturers can leverage collective expertise, drive technological advancements, and propel the industry towards continuous improvement.
Educational and Skill Development Programs
Investing in educational and skill development programs cultivates a knowledgeable and adept workforce capable of navigating technological advancements and industry complexities. By providing training initiatives, workshops, and upskilling opportunities, manufacturers equip their employees with the expertise and competencies essential for harnessing new technologies, driving innovation, and maintaining operational excellence. Empowering workers through educational programs ensures a seamless transition towards Industry 4.0 practices, fostering a culture of continuous learning and professional growth.