Unlocking the Potential of Lean Six Sigma in Lean Manufacturing for Enhanced Efficiency and Continuous Improvement
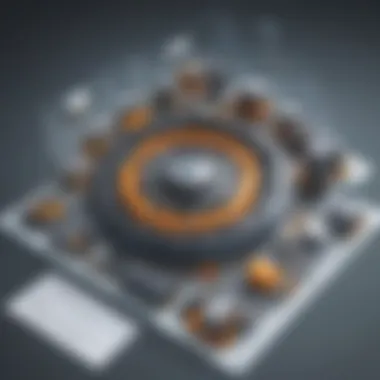
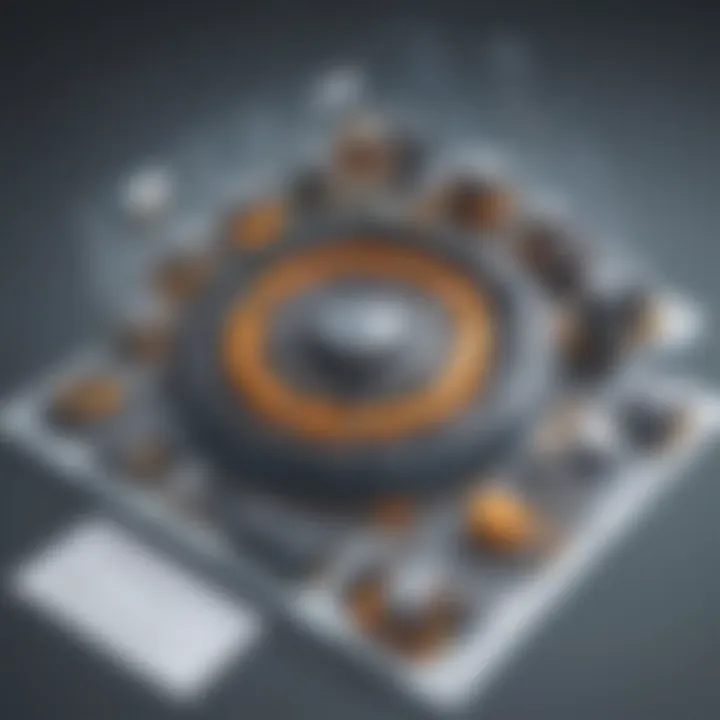
Tech Trend Analysis
The world of Lean Six Sigma in Lean Manufacturing is constantly evolving with new trends emerging. Currently, companies are focusing on integrating digital technologies into their processes, such as automation and data analytics. This trend has significant implications for consumers as it allows for improved product quality, reduced lead times, and enhanced customization. Looking into the future, there is a strong possibility of Artificial Intelligence (AI) playing a more prominent role in optimizing lean processes, further enhancing efficiency and decision-making within manufacturing settings.
Product Reviews
Delving into the realm of Lean Six Sigma tools applied in Lean Manufacturing, one can find a variety of innovative products designed to streamline operations. These tools come with a range of features and specifications tailored to specific manufacturing environments. Performance analysis of these products demonstrates a notable improvement in project outcomes, with reduced defects and increased customer satisfaction. However, it is essential to consider both the pros and cons of each tool to make an informed decision. After thorough assessment, a recommendation can be provided based on the specific needs and goals of the organization.
How-To Guides
Introducing individuals to the core concepts of Lean Six Sigma in Lean Manufacturing is crucial for successful implementation. By offering step-by-step instructions on how to apply the principles of Lean Six Sigma, organizations can effectively optimize their processes and drive continuous improvement. Furthermore, providing tips and tricks on overcoming common challenges in Lean Manufacturing can aid in smoothening the implementation journey. Troubleshooting guides can also be invaluable in addressing issues that may arise during the implementation phase, ensuring a seamless transition to a leaner operational model.
Industry Updates
Staying abreast of the latest developments in Lean Manufacturing is essential for companies seeking to maintain a competitive edge. Recent updates in the industry highlight a shift towards sustainability and eco-friendly practices, driven by consumer demand and regulatory pressures. Analyzing market trends reveals a growing emphasis on circular economy principles and the integration of green technologies in manufacturing processes. These developments have a significant impact on businesses, influencing their strategies, product offerings, and overall operation in alignment with changing market dynamics and societal expectations.
Introduction
In the realm of modern manufacturing, the amalgamation of Lean Six Sigma methods has revolutionized operational processes, propelling organizations towards greater efficiency and quality outcomes. The union of Lean principles, focusing on waste reduction and streamlined workflows, with the meticulous statistical approach of Six Sigma, dedicated to minimizing defects and variability, offers a robust framework for sustainable advancement. Understanding the synergy between Lean Six Sigma and Lean Manufacturing is paramount for businesses striving to optimize their operations and foster a culture of continuous improvement.
As we embark on dissecting the essence of Lean Six Sigma in Lean Manufacturing, it becomes evident that this integration is not merely a trend but a strategic necessity in today's competitive landscape. By embracing Lean Six Sigma, companies can unlock the full potential of their processes, paving the way for enhanced productivity, cost savings, and customer satisfaction. This article aims to delve deep into the intricacies of leveraging Lean Six Sigma principles within the realm of Lean Manufacturing, shedding light on the critical nuances that drive operational excellence and organizational success.
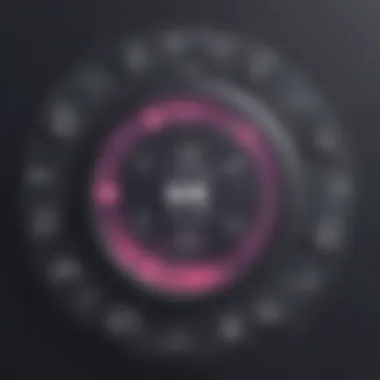
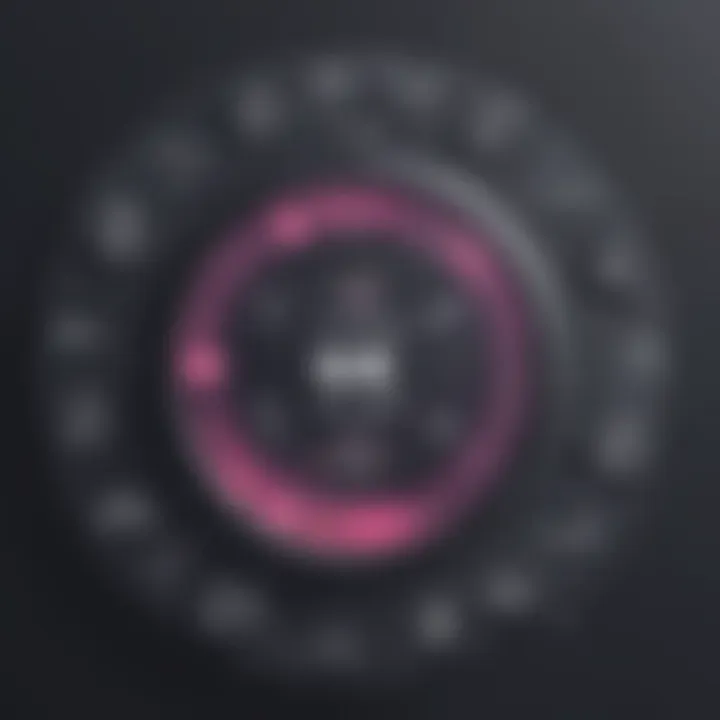
Delving into the core principles and methodologies of Lean Six Sigma, we will unravel the intricate web of tools and techniques that underpin this transformative approach. By exploring the origins of Lean Manufacturing and the foundational concepts of Six Sigma, we can grasp the evolution of these methodologies and their application in modern-day manufacturing scenarios. Moreover, we will delve into the DMAIC methodology, a hallmark of Six Sigma, focusing on Define, Measure, Analyze, Improve, and Control, which serves as a structured roadmap for process improvement and problem-solving.
Through a narrative woven with real-world examples and case studies, we will highlight the profound impact of Lean Six Sigma in enhancing process efficiency, driving innovation, and fostering a culture of continuous learning within organizations. By showcasing practical implementation strategies and success stories, readers will gain tangible insights into the transformative power of Lean Six Sigma when integrated synergistically with Lean Manufacturing. Moreover, we will address the common challenges faced during implementation and provide pragmatic solutions to mitigate risks and ensure successful adoption of these methodologies.
Understanding Lean Manufacturing
In the realm of Lean Six Sigma and Lean Manufacturing integration, a robust grasp of Lean Manufacturing is pivotal. Understanding the foundational principles and methodologies of Lean Manufacturing is essential to comprehend how this methodology synergizes with Six Sigma to drive operational excellence. Lean Manufacturing focuses on eliminating waste, optimizing processes, and enhancing overall efficiency within organizations. By embracing Lean Manufacturing practices, companies can minimize costs, improve product quality, and respond more swiftly to customer demands, thereby gaining a competitive edge in the market.
Origins of Lean Manufacturing
The origins of Lean Manufacturing can be traced back to post-World War II Japan, particularly Toyota's renowned Toyota Production System (TPS). Toyota revolutionized manufacturing by introducing concepts like Just-in-Time production, Kanban systems, and continuous improvement through employee involvement. These principles aimed to reduce wastage, increase production flexibility, and enhance overall productivity. Drawing inspiration from Ford's assembly line and various quality management approaches, Lean Manufacturing emerged as a philosophy centered on efficiency, sustainability, and lean resource utilization.
Key Principles of Lean Manufacturing
Key principles of Lean Manufacturing revolve around identifying and eliminating non-value-adding activities, known as waste. These wastes include defects, overproduction, waiting time, unnecessary transportation, excess inventory, overprocessing, and underutilization of talent. By adhering to principles such as Kaizen (continuous improvement), Just-in-Time delivery, Jidoka (automation with a human touch), and Heijunka (production leveling), organizations can enhance process efficiency, minimize lead times, and improve overall product quality. Embracing a culture of continuous improvement and waste reduction lies at the core of Lean Manufacturing philosophy.
Tools and Techniques in Lean Manufacturing
Lean Manufacturing incorporates a range of tools and techniques to streamline processes and drive efficiency. Strategies like Value Stream Mapping help visualize process flows and identify areas of improvement. 5S, Poka-Yoke, Kanban systems, and Heijunka boards are practical tools that aid in standardizing operations, reducing errors, and fostering a visual workplace environment. Through practices like Root Cause Analysis and Gemba walks, organizations can delve deep into process inefficiencies, root out defects, and implement sustainable solutions to boost overall operational performance.
Exploring Six Sigma
In the realm of Lean Manufacturing, it is imperative to delve into the realm of Six Sigma, the enhancement partner essential for quality management. Understanding the implications of Six Sigma within the premises of this article is crucial for optimizing operations and quality control mechanisms. Exploring Six Sigma involves delving into its foundational principles, methodologies, and pervasive benefits that intertwine with Lean Manufacturing to cultivate a robust operational framework.
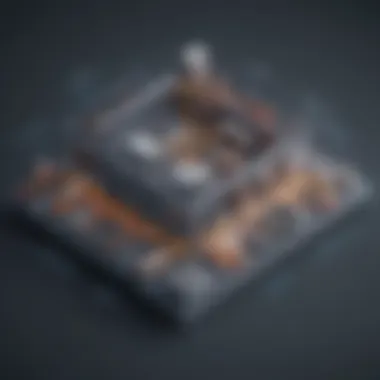
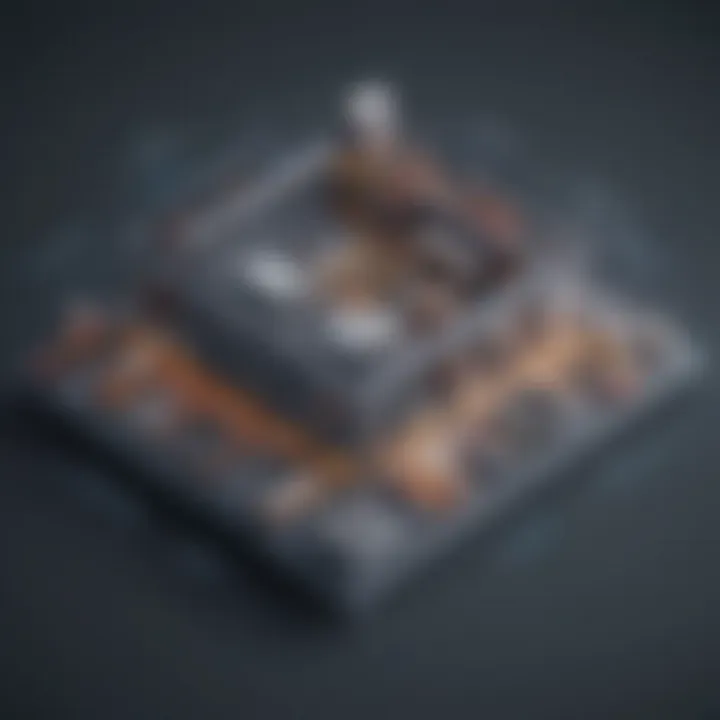
Foundations of Six Sigma
The bedrock of Six Sigma lies in its meticulous attention to statistical data analysis and process improvement methodologies. By adhering to statistical methods, organizations can pinpoint areas of variation and inefficiencies, paving the way for precise problem-solving strategies. Foundationally, Six Sigma instills a data-driven approach that aligns seamlessly with the principles of Lean Manufacturing, fostering a culture of continual enhancement and sustainable growth.
DMAIC Methodology
DMAIC, an acronym encapsulating Define, Measure, Analyze, Improve, and Control, epitomizes the structured approach of Six Sigma towards process optimization. This methodological framework provides a systematic pathway for identifying process bottlenecks, analyzing root causes of defects, and implementing targeted improvements. Through DMAIC, organizations can achieve tangible results by rigorously following each phase to drive operational excellence and elevate overall efficiency levels.
Key Concepts and Benefits of Six Sigma
The underlying concepts of Six Sigma revolve around achieving near-perfect processes by minimizing defects and deviations from the ideal state. By focusing on key concepts like statistical analysis, process standardization, and continuous monitoring, organizations can attain unparalleled levels of operational efficiency and quality control. The benefits of implementing Six Sigma methodologies include enhanced productivity, reduced waste, improved customer satisfaction, and heightened profitability โ all fundamental aspects that synergize harmoniously with the objectives of Lean Manufacturing.
The Synergy of Lean Six Sigma
In the realm of Lean Manufacturing, the integration of Lean Six Sigma constitutes a paramount juncture. This pivotal synergy brings together the core principles and methodologies of Lean Manufacturing and Six Sigma to create a powerhouse of process optimization and quality enhancement. By intertwining the streamlined efficiency of Lean techniques with the rigorous statistical analysis and defect reduction focus of Six Sigma, organizations can achieve unparalleled levels of operational excellence and continuous improvement. The significance of this integration lies in its ability to refine operations, eliminate waste, and foster a culture of relentless enhancement.
Integration Benefits
The fusion of Lean Six Sigma bestows manifold benefits upon organizations venturing down the path of process optimization. One of the primary advantages lies in the dual approach towards waste reduction and variation minimization. Lean tools like Value Stream Mapping and 5S complement Six Sigma's DMAIC methodology, offering a comprehensive toolkit to tackle inefficiencies and defects systematically. This amalgamation leads to substantial cost savings, improved product quality, and heightened customer satisfaction, positioning businesses for sustainable success in today's competitive landscape.
Common Goals and Objectives

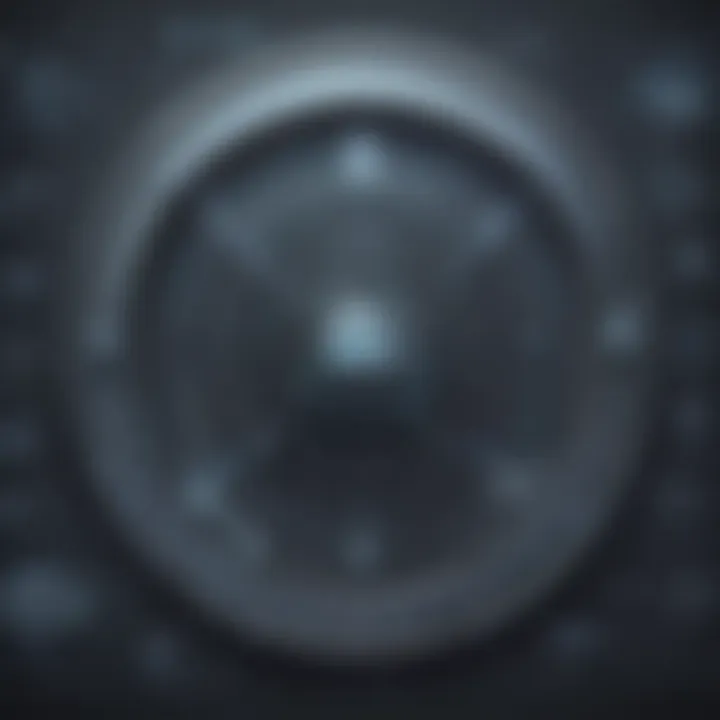
As organizations embark on the Lean Six Sigma journey, they align themselves towards common goals and objectives aimed at driving continuous improvement. Both methodologies share the overarching vision of maximizing value for customers through the relentless pursuit of waste elimination, process optimization, and variation reduction. By fostering a culture of data-driven decision-making, employee empowerment, and customer-centricity, businesses can synchronize their efforts towards achieving operational excellence and delivering exceptional quality outcomes.
Enhancing Process Efficiency
At the heart of Lean Six Sigma lies the objective of enhancing process efficiency through a systematic approach to problem-solving and continuous improvement. By utilizing Lean tools for identifying and mitigating non-value-added activities and Six Sigma techniques for reducing defects and variations, organizations can streamline their operations, minimize lead times, and optimize resource utilization. This dual approach not only enhances productivity and competitiveness but also instills a culture of operational excellence and innovation, enabling organizations to adapt swiftly to market dynamics and customer demands.
Lean Six Sigma in Practice
Lean Six Sigma in practice plays a pivotal role in the realm of Lean Manufacturing, as it serves as the driving force behind operational excellence and quality enhancement within organizations. With a meticulous focus on eliminating defects and minimizing variability, Lean Six Sigma methodologies offer a systematic approach to process improvement. By integrating Lean principles of waste reduction with Six Sigma's data-driven problem-solving techniques, companies can achieve tangible results in terms of cost savings, increased productivity, and enhanced customer satisfaction.
Implementation Strategies
When embarking on Lean Six Sigma initiatives, organizations must carefully craft their implementation strategies to ensure successful outcomes. It is essential to start by clearly defining project goals and establishing key performance metrics to track progress effectively. By conducting a thorough assessment of current processes and identifying pain points, companies can prioritize improvement efforts that promise the most significant impact. Additionally, fostering a culture of continuous learning and empowering employees to participate in improvement projects are crucial aspects of a successful implementation strategy.
Case Studies and Success Stories
Examining real-world case studies and success stories can provide valuable insights into the practical application of Lean Six Sigma principles. By showcasing how organizations across various industries have leveraged Lean Six Sigma methodologies to drive efficiencies and achieve significant cost reductions, readers can gain a deeper appreciation for the transformative power of these methodologies. From improved cycle times to enhanced product quality, these case studies underscore the tangible benefits that come with embracing Lean Six Sigma practices.
Overcoming Challenges
While the benefits of Lean Six Sigma are substantial, organizations may encounter challenges during the implementation process. Common obstacles include resistance to change, lack of leadership support, and difficulty in sustaining improvement gains over time. To overcome these challenges, companies need to invest in robust training programs, establish clear communication channels, and involve stakeholders at all levels in the improvement journey. By proactively addressing potential roadblocks and building a resilient framework for continuous improvement, organizations can navigate challenges effectively and drive long-term success.
Future Trends and Innovations
In the realm of Lean Six Sigma and Lean Manufacturing, the exploration of Future Trends and Innovations holds paramount importance. This section elucidates the critical evolution and advancements anticipated in the integration of these methodologies, shaping the future of process optimization and quality management. As industries strive for continuous enhancement and adaptation to dynamic market demands, embracing emerging trends becomes instrumental. Understanding the direction in which Lean Six Sigma and Lean Manufacturing are heading is not merely insightful but also strategic for organizations seeking sustained relevance and competitiveness in a rapidly evolving landscape.
Diving deeper, the discourse on Future Trends and Innovations within the context of this article shines a spotlight on crucial elements shaping the future of operational excellence. By analyzing emerging technologies, such as Artificial Intelligence (AI), Internet of Things (IoT), and Big Data analytics, it becomes evident how these innovations are revolutionizing the application of Lean Six Sigma and Lean Manufacturing. The seamless integration of digital tools and data-driven insights presents unparalleled opportunities for organizations to optimize processes, identify inefficiencies, and elevate quality standards to unprecedented levels.
Moreover, the benefits derived from aligning with Future Trends and Innovations in Lean Six Sigma and Lean Manufacturing are multifaceted. From accelerated decision-making empowered by real-time data analytics to predictive maintenance strategies enhancing equipment reliability, the implementation of cutting-edge technologies propels efficiency and competitiveness. Noteworthy considerations regarding scalability, cybersecurity, and adaptability also feature prominently, underscoring the importance of aligning future-oriented strategies with core business objectives to ensure sustainable growth and resilience.