Innovations in 3D Printing: Transforming Modern Industry
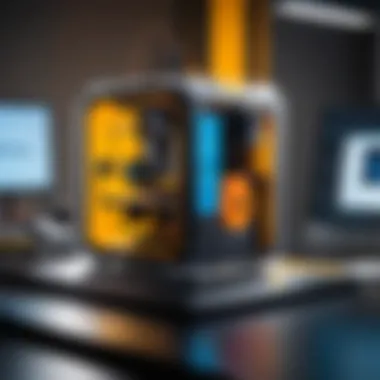
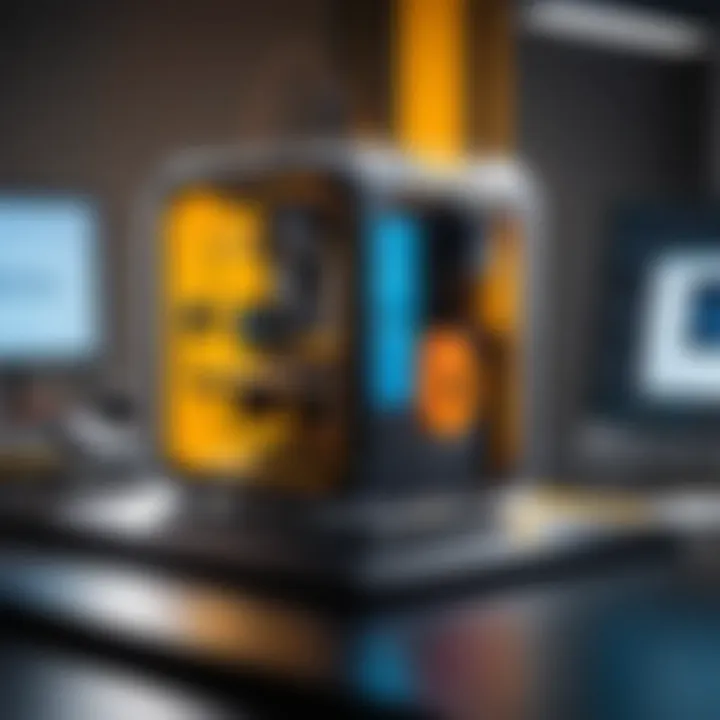
Intro
3D printing technology is leading a shift across many industries. This transformative method goes beyond traditional manufacturing. It offers new possibilities in healthcare, design, and many more fields. The potential application of 3D printing helps to shape a modern approach in various sectors. Understanding the innovations in this area can provide insights into future developments.
Recent advancements show a clear trend towards customizing products and production methods. Companies now seek flexibility and speed in creating objects. The implications are vast. Consumers benefit from more personalized options and reduced costs. It is crucial to analyze current trends, performance, and industry predictions. This foundation marks the start of digging deeper into what 3D printing means in today’s context.
Tech Trend Analysis
Overview of the current trend
The world of 3D printing today is marked by integration with digital technologies. Companies utilize sophisticated software and hardware solutions to enhance production capabilities. More advanced machines produce high-resolution outputs, enabling intricate designs. Integration with artificial intelligence is also on the rise. This use showcases 3D printing's evolution towards a more intelligent approach.
Implications for consumers
Consumers benefit greatly from 3D printing advancements. Customization is one of its primary advantages. Instead of fitting into generic molds, products can reflect unique preferences and specifications. For instance, in fashion and home design, consumers can have items made to their exact requests. Price reductions in prototype production also mean that companies can deliver superior value.
Future predictions and possibilities
Looking ahead, the trajectory for 3D printing appears positive. Forecasts suggest increased adoption across industries. Manufacturing will likely see shorter lead times and less waste. In medicine, possibilities such as organ printing may change transplant practices surprisingly. For design professionals, new tools may allow unprecedented creative freedom, continually pushing innovation boundaries.
"3D printing is no longer just about making prototypes; it's reshaping how we think about design and customization in products across various sectors."
While the future is uncertain, ongoing research and investment suggest that current technology has only scratched the surface. Innovations in materials and printing methods also hint at countless possibilities.
Industry Updates
Recent developments in the tech industry
Numerous companies have announced breakthroughs in the field. Step-by-step machinery advances promise greater efficiency. These updates include improved filament materials that are stronger and lighter. Demand for sustainable options rises. As processing capabilities grow, some manufacturers pivoted to eco-friendly practices.
Analysis of market trends
The market indicates clear signs of expansion through sectors. Healthcare applications, such as medical implants and surgical tools, show a marked increase. Similarly, sectors like construction explore concrete printing. Trends show venture capitalists are keen on investing in innovative startups, fueling further R&D advancements.
Impact on businesses and consumers
For businesses, adopting 3D printing minimizes costs while maximizing efficiency. It also fosters innovation in product development. For consumers, transparency and accessibility increase. Education on functionality leads to a more informed market. Additionally, it offers everything from rapid production to unique products tailored to personal needs.
Prelims to 3D Printing
3D printing has seen remarkable advancements in recent years. This topic is vital as it touches upon various industries which are reshaping modern manufacturing methods. The advent of 3D printing is not merely a technological breakthrough, but it also brings about a paradigm shift in how entities approach production and design. Companies can create complex parts that were once difficult or expensive to produce. This section provides a foundation to understand subsequent discussions on technologies and applications in the field.
Definition of 3D Printing
3D printing, often referred to as additive manufacturing, is a process that constructs three-dimensional objects by layering materials based on digital models. This process contrasts sharply with traditional manufacturing methods, which often involve cutting away material from a solid block. The ease of creating intricate designs with precise dimensions makes 3D printing attractive. It accommodates various materials, including plastics, metals, and even biological tissues, thus marking a new era in customization and innovation.
Historical Context
Understanding the history of 3D printing provides insights into present developments. The journey began in the early 1980s with Chuck Hull’s invention of stereolithography, the first 3D printing technology. Initially conceptualized for prototyping, the use of 3D printing expanded significantly over the decades. In the 1990s, companies started applying it in more than just product development.
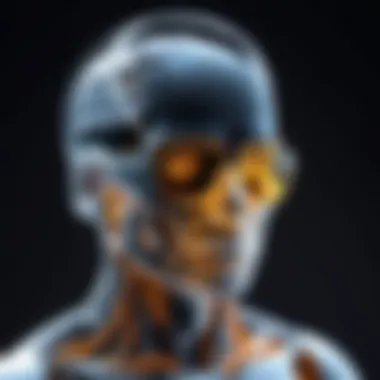
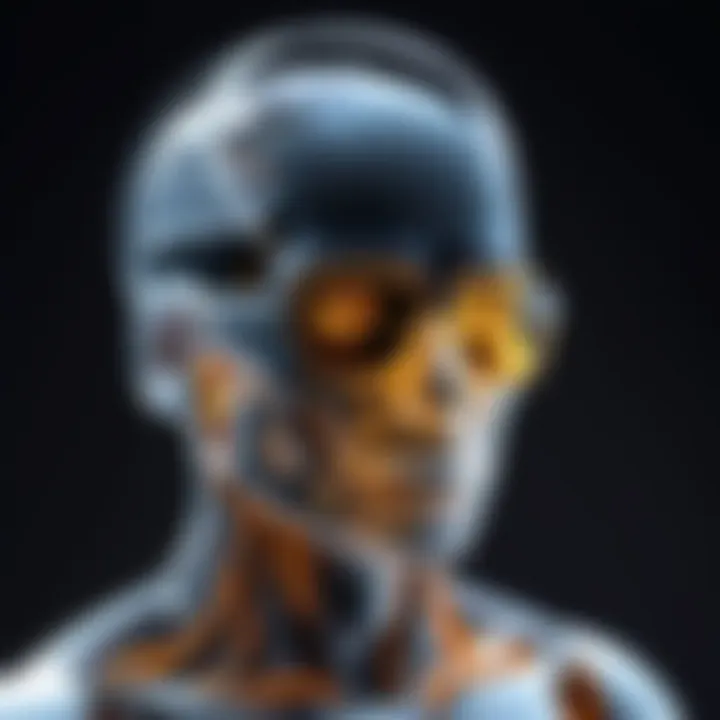
In the early 2000s, as patents expired, a surge of new techniques emerged, each providing unique advantages within specific industries. Today, sectors such as healthcare and aerospace utilize 3D printing not only for prototyping but also for producing end-use products. This long journey from industrial novelty to widespread application demonstrates how far technology has come and sets the stage for future innovations.
Technologies Behind 3D Printing
The variety of technologies that underpin 3D printing play a fundamental role in shaping the practical applications of this innovation. Each technique offers distinct advantages, challenges, and material compatibilities, which can vastly affect the end-produced object. Understanding these technologies allows industry professionals and enthusiasts alike to discern the right approach for a given project.
Additive vs.
Subtractive Manufacturing
Additive manufacturing and subtractive manufacturing represent two pivotal production paradigms. In traditional subtractive manufacturing, material is removed from a solid block to create a part, employing processes such as milling, drilling, and turning. This efficacious method is time-tested, yet it often results in significant waste. On the contrary, additive manufacturing builds an object layer by layer. This method drastically cuts down on waste, fostering sustainability.
Besides waste reduction, additive manufacturing provides superior customizability. Each layer can be modified to cater to specific needs, allowing for intricate geometries and designs that are unattainable by subtractive means. Many industries are leaning toward additive methods given their efficiency and potential for rapid prototyping.
Material Extrusion Technologies
Material extrusion is perhaps the most recognized method of 3D printing. It involves the continuous deposition of material, through nozzels, to create objects progressively. Fused Deposition Modeling (FDM) falls under this category. In this case, thermoplastic filaments are heated, melted, and extruded to form desired shapes.
The success of material extrusion is partially due to its affordability, making it accessible to a wide range of users from hobbyists to professionals. However, it is not without its limitations. For instance, items created through FDM can exhibit weaker structural integrity and a lower resolution in fine details compared to other techniques, which may be a consideration for certain applications. Nevertheless, the versatility of materials like PLA, ABS, and PETG offers varied choices for users.
Powder Bed Fusion Techniques
Examples of powder bed fusion include Selective Laser Sintering (SLS) and Selective Laser Melting (SLM). These methods utilize lasers to fuse powder particles, constructing solid objects directly from digital models. These techniques excel in forming complex geometries and are popular in high-strength components, often found in industries such as aerospace and automotive.
The unique quality of powder bed fusion lies in the fundamental control of heat. Each layer is selectively sintered or melted, which ensures superior layer adhesion and structural integrity. Yet, there are downsides, including prolonged production time and higher equipment costs. Additionally, post-processing steps like powder removal and surface finishing can demand time and technical expertise.
Other Notable Techniques
Aside from the primary methods of material extrusion and powder bed fusion, various notable techniques exist each contributing to different application fields. One rising technique is Binder Jetting, where a binding agent is deposited onto a powder bed for layer formation. This approach enjoys versatility, working with a wide range of materials, including ceramics and metals.
Digital Light Processing (DLP) represents another exciting method. Here, light is projected onto photosensitive resin, solidifying it layer by layer. This allows for highly detailed resolutions, especially advantageous in applications such as jewelry-making and dental implants.
As these technologies advance, 3D printing continues to offer unprecedented potentials across varied sectors, affirming innovations in manufacturing processes.
Applications of 3D Printing in Industry
The applications of 3D printing in industry cannot be overstated. This technology has moved beyond simple prototyping and is reshaping many sectors by providing innovative solutions. It decreases production times, increases customization abilities, and leads to better sustainability practices.
Manufacturing Components
In the manufacturing sector, 3D printing allows for the production of complex components that were once impossible to create through traditional methods. With techniques like selective laser sintering and fused deposition modeling, manufacturers can produce components with intricate designs. This ability significantly cuts down on the need for assembly parts. Furthermore, 3D printing enables rapid iteration of component designs, resulting in shorter product development cycles. Companies such as GE are leading the way in using 3D printing for aerospace components, allowing for lightweight and durable parts that improve fuel efficiency in jets.
Healthcare Innovations
The impact of 3D printing on healthcare is extraordinary. This technology paves new avenues for customized prosthetics and implants. It provides a huge benefit in producing tailored medical devices, creating a personal fit for each patient. Moreover, advances in bioprinting are showing promising results. Researchers at institutions like Wake Forest Institute for Regenerative Medicine are working on printing human tissues and organs which may change transplant methods drastically. This customization enhances patient satisfaction and often leads to better outcomes.
Architectural Prototyping
In architecture, 3D printing simplifies the prototyping process. Design iterations can be printed quickly, moving from a concept to a physical model in no time. Tools like the Vertico 3D Concrete Printer allow architects to create detailed, large-scale models that represent the final ideas effectively. This is advantageous for stakeholder presentations and also for urban planning services. It saves time and reduces waste, leading to a more sustainable process.
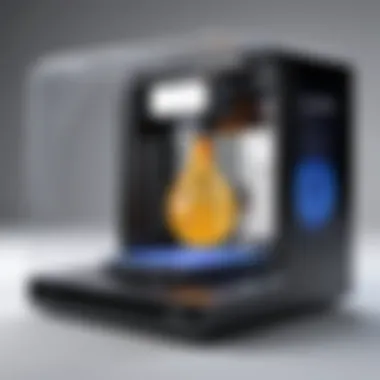
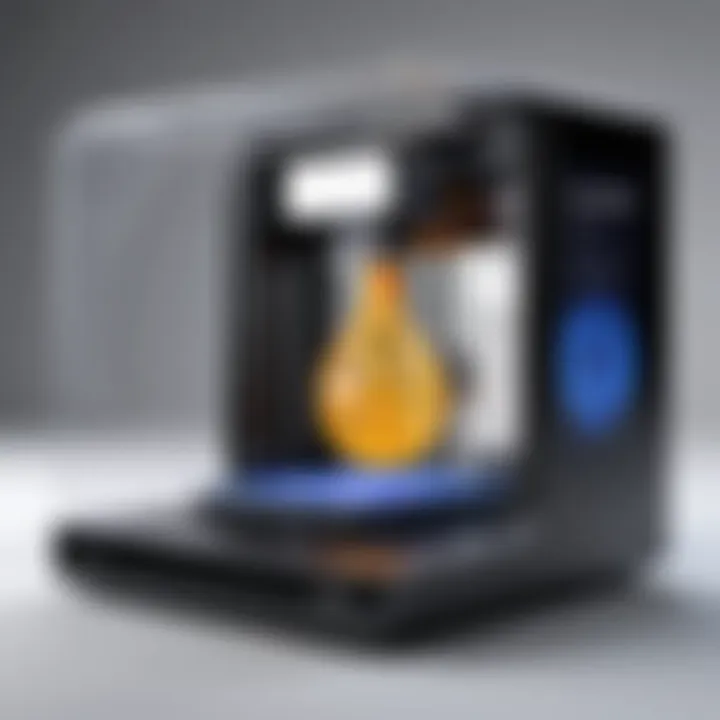
Fashion and Design
The fashion industry is gradually accepting 3D printing to challenge conventional methods. Designers can use 3D printing to produce unique clothing, accessories, and even shoes. Brands like Adidas and Nike are experimenting with this technology to customize products without the lengthy traditional fabric supply chains. By employing 3D printing, they reduce excess fabric that'll potentially go to waste, showing a promising move towards environmental consciousness. This method enables accessibility in the fashion space, allowing smaller designers to bring their innovative creations to market.
Through these applications, 3D printing is not just a technological novelty; it is a transformative force that enhances efficiency, encourages creativity, and contributes to sustainability across industries.
Looking at the broader context, the applications are reflections of how technology converges with user demands. As industries continue to develop, it will be exciting to watch how 3D printing can innovate traditional practices further.
Benefits of 3D Printing
The significance of benefits attributed to 3D printing cannot be understated. This transformative technology presents multiple advantages for industries by reshaping traditional processes and introducing new opportunities. Specifically, three pivotal aspects highlight the superiority of 3D printing over conventional manufacturing: cost efficiency, customization and flexibility, and reduced waste.
Cost Efficiency
Cost efficiency is one of the most compelling advantages of 3D printing. Traditional manufacturing methods often require large setups, extensive labor, and costly materials. In contrast, 3D printing eliminates some of those expenses. Production can begin from digital designs, allowing for shorter lead times and reduced overall costs.
- Lower Material Waste: With additive manufacturing, materials are used only where needed. This significantly offsets costs related to raw materials.
- Tooling Expenses: 3D printing often reduces the need for specific tools and molds. This brings substantial savings, particularly in small-batch production scenarios.
- Rapid Prototyping: Enterprises can test designs faster and for less money, enabling a quicker move from concept to market.
Customization and Flexibility
Another pinnace of 3D printing benefits is the customization it enables. Traditional production processes are limited when it comes to tailoring products for individual desires. Meanwhile, 3D printing fosters a new level of personalization.
- Bespoke Solutions: Companies can manufacture unique items adapted to client demands. This capability is crucial in niches such as healthcare for patient-specific devices.
- Rapid Iteration: Adjustments in design can be made swiftly, which permits innovation and responsiveness to market trends.
- Variety of Design Possibilities: The technology allows for intricate designs incompatible with traditional production methods, eliciting fresh creative possibilities in various fields such as fashion and architecture.
Reduced Waste
Environmental considerations are increasingly vital, and 3D printing offers solutions that align with sustainable practices. This manufacturing technique promotes eco-friendly approaches through the concept of reduced waste.
- Minimal Material Loss: Additive manufacturing primarily uses only the required materials, significantly cutting down on excess scraps. This directly decreases waste processing costs.
- Energy-Saving Production: The reduced material input also often leads to lower energy consumption, which carves out improvements not just in costs but in environmental impact as well.
Investing in 3D printing technology collectively enhances economic viability while fostering innovations that travel beyond waste limitations and customization.
Challenges and Limitations
Understanding the challenges and limitations of 3D printing is essential for a comprehensive view of its current position in modern industry. While 3D printing offers significant advantages, it does not come without obstacles that hinder its growth and implementation. These factors can influence decision-making in industries looking to adopt this technology. It is crucial for stakeholders to consider materials, production speeds, and regulatory frameworks as they evaluate the viability of 3D printing solutions in their operations.
Material Limitations
One of the primary challenges in 3D printing is related to material limitations. The ideal materials for 3D printing must have certain properties such as durability, tensile strength, and heat resistance. Here are key issues:
- Some printable materials do not possess the mechanical properties necessary for heavy-duty applications.
- Certain industries encounter issues with material availability. Not all materials can be easily sourced or might be inflated in price due to low supply.
- Compatibility between printer technology and materials can also be a concern. Not all printers support the diverse range of materials, which limits flexibility in production.
Advancements in material development are necessary to address these limitations, but it still remains a work in the progress.
Speed of Production
Another critical aspect is the speed of production. The production time for complex designs using 3D printing can be longer than traditional manufacturing methods, especially with high-resolution prints. Factors influencing print speed include:
- Layer height and aesthetic detail can significantly extend printing duration.
- Complex geometries can require additional support structures, further delaying the process.
- In mass production environments, methods like injection molding are typically faster and more cost-effective than 3D printing, which can make it challenging to justify the immediacy of 3D printing for high volume production. To remain competitive, proponents must aim for continuous improvements in print technologies and methods to lessen production times effectively.
Regulatory Considerations
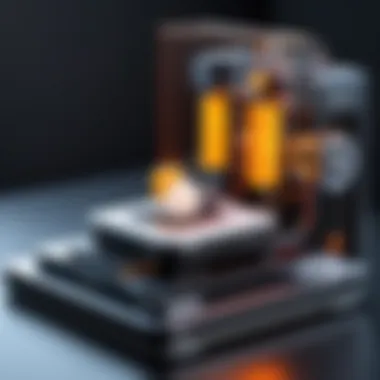
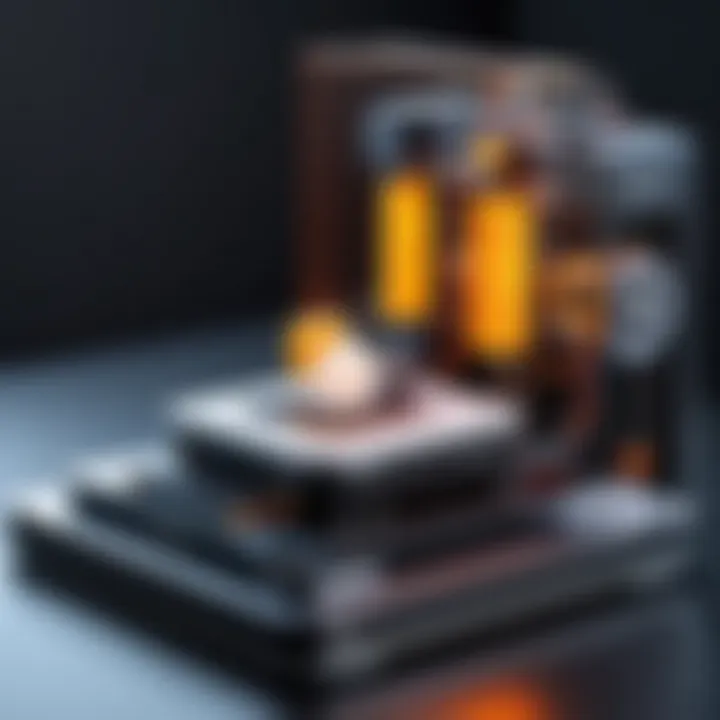
Finally, regulatory considerations add another layer of complexity. Since 3D printing falls within emerging technologies, regulatory frameworks are often unclear or undeveloped. Issues that arise in this area include:
- Intellectual property concerns as replication and modification of designs are simple with 3D printing.
- Safety standards for products created through 3D printing need to be established to ensure consumer protection across sectors like healthcare and manufacturing.
- Environmental regulations concerning material disposal and production methods may affect compliance.
Defining clear regulations and standards is essential for fostering industry confidence and sustaining innovation.
Addressing these challenges is not just fundamental; it’s imperative to harness the full potential of 3D printing. Each restriction plays a vital role in shaping the industry's approach to this transformative technology, and both developers and users must be aware of the limitations as they seek to implement it in future projects.
Future Trends in 3D Printing
In the rapidly evolving landscape of technology, the future trends in 3D printing emerge as crucial indicators of industry transformation. This section outlines the pivotal advancements expected in 3D printing, shedding light on their potential to enhance manufacturing processes, increase customization, and contribute to sustainability.
Emerging Materials and Techniques
The materials used in 3D printing are experiencing a significant evolution. Designers and engineers are increasingly exploring innovative substances.
- Biomaterials: These materials are biodegradable and compatible with living systems, thus dramatically influencing fields like healthcare. Organs and tissue constructs can potentially be created, revolutionizing surgical procedures.
- Metal Alloys: Advanced metal 3D printing techniques have led to the production of intricate metal components. As a result, sectors such as aerospace and automotive are likely to reap the benefits of lightweight yet durable parts.
- Composite Materials: Combining different materials allows for enhanced characteristics, such as increased strength and reduced weight. Future printed objects can feature a blend of polymers, which expands design possibilities.
As these materials are further developed, efficiency and functionality will sustain better performance than conventional solutions. Companies must embrace these innovations to maintain a competitive edge.
Integration with AI and Automation
Integrating artificial intelligence with 3D printing could significantly boost operational capabilities and workflow efficiency. AI algorithms can enhance design processes, optimize production parameters, and predict maintenance needs. With autonomous systems, some of the following improvements are likely:
- Design Optimization: AI can analyze large datasets to generate optimized structures, ensuring that items fulfill performance criteria while minimizing material use.
- Predictive Maintenance: Using AI for monitoring machines helps in predicting when a technician is needed. This is pivotal for rapid production methods, allowing businesses to minimize downtime.
- Supply Chain Automation: Automating supply chains allows for just-in-time production, significantly reducing inventory costs. Companies can customize products swiftly, adapting to fresh market trends and consumer needs immediately.
The merger of AI with 3D printing can provide a level of customization and flexibility that the industries have not seen before.
Global Adoption and Impact
The 3D printing revolution is not limited to a single country or sector. Global adoption signifies a collective shift in manufacturing practices, allowing for transformative effects on international markets. Some noteworthy aspects include:
- Decentralization of Manufacturing: 3D printing facilitates local production, minimizing transportation costs and reducing carbon footprints. Manufacturing close to the consumer location could herald a new age in logistics.
- Job Creation: Contrary to fears that automation eliminates jobs, new roles are developing. Skilled technicians, design professionals, and software engineers are in demand to manage the growth of 3D printing tech.
- Global Collaboration: Innovation spreads rapidly across borders. Developing countries benefit by utilizing 3D printing for local initiatives, such as housing and infrastructure projects. This fosters global partnerships focused on sustainable development.
In summary, the future trends in 3D printing showcase a landscape of possibility, touching various aspects of society. Industry professionals must keep abreast of these changes to appreciate the plausible seismic shifts that could redefine how products are conceptualized and realized.
3D printing technology has the potential to transform the future of manufacturing, bringing unprecedented innovation across numerous fields.
Epilogue
The transformative nature of 3D printing holds significant implications in today's industrial landscape. Understanding this technology's impact helps tech enthusiasts and industry experts recognize its potential in reshaping various sectors. The conclusion here serves to encapsulate the core insights discussed throughout the article, emphasizing how innovations continue to drive progress and adaptability in manufacturing, healthcare, and design.
Summation of Key Points
3D printing has proven it is not a mere trend; rather, it interjects itself profoundly into the fabric of contemporary production methods. Key points from the article include:
- Diverse Applications: From creating complex components in aerospace to personalized healthcare solutions, the range of applications is vast.
- Cost Efficiency and Customization: This technology allows businesses to produce tailored products at lower costs, streamlining their operations.
- Challenges: Material constraints and regulatory frameworks still pose hurdles, yet they are being continuously addressed through innovation.
- Emerging Technologies: Advances in materials and AI integration await, paving the road for future possibilities and improvements.
_"The fundamental shift in how products are produced opens up avenues previously considered unattainable."
Call to Action for Further Exploration
Solving existing challenges in 3D printing requires continued research and public engagement. Tackling the barriers will demand more than what today's industry can provide. As technology enthusiasts or industry professionals, it is crucial to stay informed and engaged.
- Explore latest developments on platforms like Wikipedia
- Join discussions in communities dedicated to innovations such as Reddit
- Follow research and updates on industry platforms and forums.
Delve into academic papers, attend webinars, and participate in discussions to expand your understanding. Remaining curious about the ongoing advancements ensures we can all contribute to maximizing the efficacy and potential that 3D printing holds in shaping our future.