Unveiling the Profound Influence of Composites Across Diverse Job Sectors
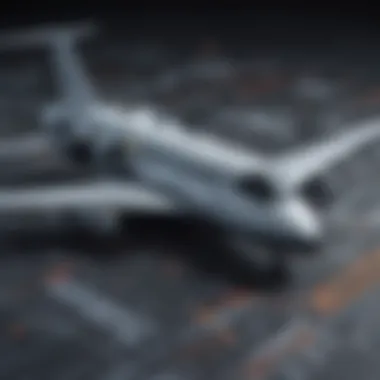
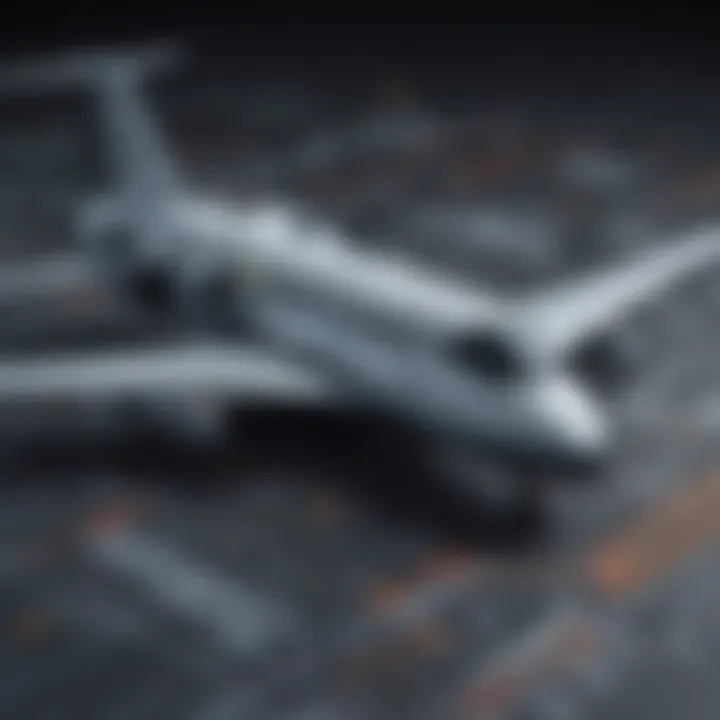
Tech Trend Analysis
In the realm of modern job industries, a noticeable shift towards the utilization of composites has been observed. These innovative materials, characterized by their lightweight, durable, and versatile properties, are revolutionizing sectors such as aerospace and automotive. The current trend showcases a growing preference for composites due to their ability to enhance performance while reducing overall weight. This transition not only impacts manufacturers but also has far-reaching implications for consumers.
Predictions for the future indicate a continued surge in the integration of composites across various industries. As technology advances and manufacturing processes evolve, composites are poised to play an even more substantial role, offering solutions that prioritize efficiency and sustainability. This transformative trend represents a significant paradigm shift in how industries approach materials, shaping the job landscape for professionals seeking to adapt to these innovative changes.
Industry Updates
Recent developments in the tech industry have underscored the pivotal role of composites in driving market trends and consumer preferences. Manufacturers are increasingly focusing on the integration of composite materials to meet the demand for lightweight, high-performance products. This strategic shift not only addresses evolving consumer needs but also reflects a broader recognition of the benefits that composites bring to various sectors. A comprehensive analysis of market trends reveals a growing momentum towards composite adoption, with businesses leveraging these advanced materials to gain a competitive edge in the market.
The impact of these industry updates extends beyond the realm of manufacturing, influencing how businesses operate and engage with consumers. As industries embrace composites to enhance product offerings and streamline operations, job requirements are evolving to accommodate the demand for professionals skilled in the application of composite technologies. The implications of these developments resonate across job industries, shaping the skill sets and expertise that are increasingly sought after in today's dynamic market.
Introduction to Composites
Composites have revolutionized modern job industries by providing lightweight, durable, and versatile solutions. The integration of composite materials in various sectors such as aerospace, automotive, and construction has significantly impacted the way industries operate. Their unique properties, including high strength-to-weight ratio and corrosion resistance, make them a preferred choice across different applications. As industries evolve, the demand for composites continues to grow, prompting the need for skilled workforce proficient in composite fabrication and design engineering.
Definition and Components
Composite materials are a combination of two or more constituents with distinct properties that, when combined, create a material with enhanced characteristics. In general, composites consist of a matrix material that binds reinforcement fibers or particles together. The matrix material can be polymer-based, metal-based, or ceramic-based, depending on the desired properties of the final composite. Reinforcements such as carbon fibers, glass fibers, or ceramic particles impart specific mechanical, thermal, or electrical properties to the composite, making it suitable for diverse applications.
Types of Composites
Polymer Matrix Composites
Polymer matrix composites are widely used in industries due to their versatility and ease of fabrication. These composites consist of a polymer resin matrix reinforced with fibers like carbon or glass. The key characteristic of polymer matrix composites is their excellent corrosion resistance and high impact strength, making them ideal for applications requiring lightweight and durable materials. Despite their benefits, polymer matrix composites may suffer from limitations such as lower temperature resistance compared to metal or ceramic composites.
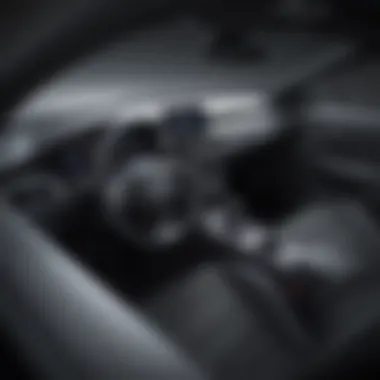
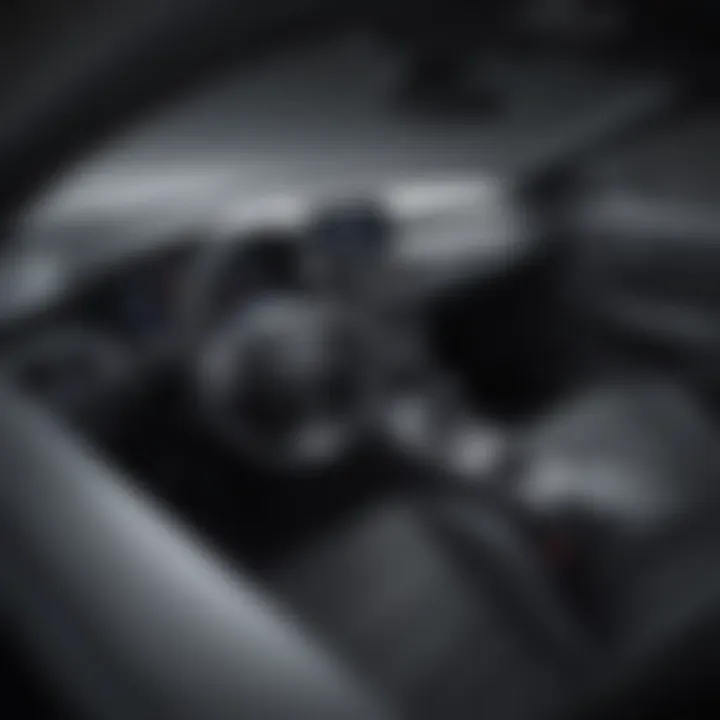
Metal Matrix Composites
Metal matrix composites involve a metal matrix reinforced with ceramic, metal, or polymer fibers. The primary advantage of metal matrix composites is their high thermal conductivity and superior strength at elevated temperatures. These composites find applications in components requiring heat dissipation and high structural integrity. However, the main drawback of metal matrix composites lies in their relatively higher cost of production compared to other types of composites.
Ceramic Matrix Composites
Ceramic matrix composites combine ceramic matrix materials with ceramic fibers or particles to achieve exceptional hardness and thermal resistance. The distinct feature of ceramic matrix composites is their ability to withstand extremely high temperatures and harsh environments, making them suitable for aerospace and industrial applications. Despite their excellent mechanical properties, ceramic matrix composites may face challenges related to brittleness and processing complexities, limiting their widespread adoption in certain industries.
Applications of Composites in Job Industries
Composites have revolutionized various job sectors by offering lightweight, durable, and versatile solutions, transforming the way industries operate. In the aerospace industry, composites are widely utilized for manufacturing aircraft structures and spacecraft components, providing exceptional strength-to-weight ratios and fuel efficiency. The automotive sector benefits from composites in vehicle body panels and engine components, enhancing performance and reducing overall weight. Additionally, the construction field leverages composites for building materials and infrastructure applications for their corrosion resistance and high strength properties, revolutionizing the construction industry.
Aerospace Industry
Aircraft Structures
Aircraft structures are integral components of airplanes that require high strength and durability while minimizing weight to improve fuel efficiency. Composites, such as carbon fiber and fiberglass, are favored for their superior strength-to-weight ratio, corrosion resistance, and design flexibility. These materials enable manufacturers to produce lighter aircraft structures that enhance overall performance and reduce operational costs.
Spacecraft Components
Spacecraft components play a crucial role in the construction and operation of space vehicles. Composites are preferred for spacecraft components due to their lightweight nature, thermal stability, and resistance to harsh space environments. By utilizing composites in spacecraft construction, manufacturers can achieve optimal weight distribution and ensure the durability required for space exploration missions.
Automotive Sector
Vehicle Body Panels
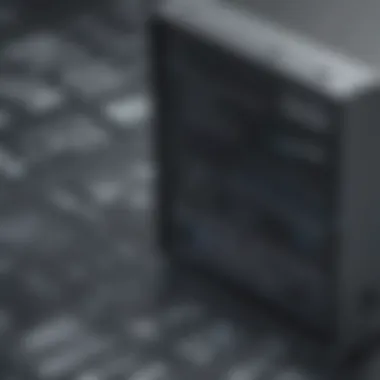
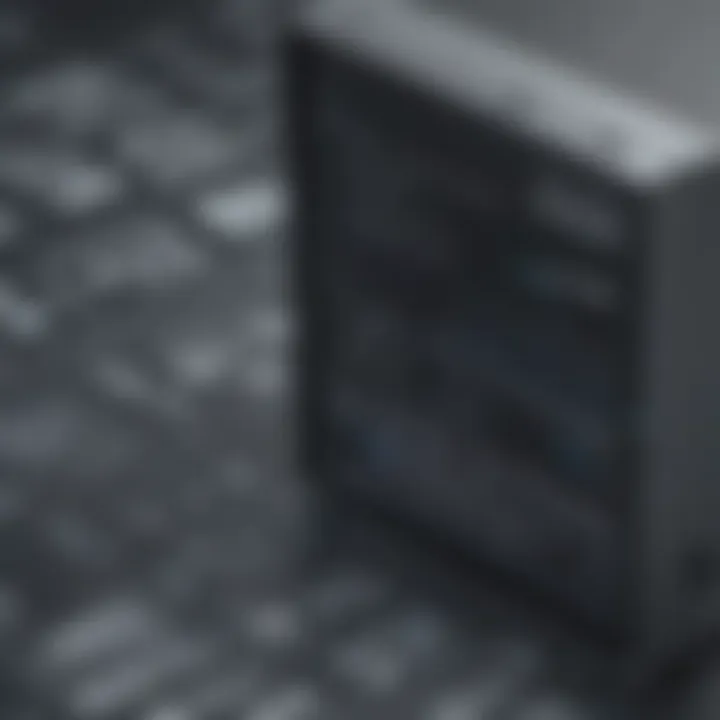
Composites are increasingly used in vehicle body panels to enhance strength, reduce weight, and improve fuel efficiency. Carbon fiber composites offer exceptional strength and impact resistance, making them ideal for automotive applications where safety and performance are paramount. By integrating composites into vehicle body panels, automakers can achieve significant weight savings without compromising structural integrity.
Engine Components
Engine components, such as intake manifolds and cam covers, benefit greatly from composite materials due to their high heat resistance and durability. Composites like carbon fiber reinforced polymers excel in withstanding extreme temperatures and harsh operating conditions, making them a preferred choice for high-performance engines. By incorporating composites into engine components, manufacturers can enhance efficiency and longevity.
Construction Field
Building Materials
Composites are reshaping the construction industry by providing innovative building materials that offer superior strength, durability, and design flexibility. Composite building materials, including fiberglass-reinforced polymers and carbon composites, are replacing traditional materials like steel and concrete due to their lightweight nature and resistance to corrosion. These materials are revolutionizing construction practices by enabling faster construction times and reducing maintenance costs.
Infrastructure Applications
Composites play a vital role in infrastructure applications, such as bridges, pipelines, and storage tanks, due to their excellent strength-to-weight ratio and corrosion resistance. Composite materials ensure structural integrity and durability in various infrastructure projects, making them a preferred choice for demanding environments. By incorporating composites into infrastructure applications, engineers can enhance project longevity and reduce maintenance requirements.
Impact on Job Opportunities
In the realm of modern job industries, the advent of composites has brought about a significant shift in demands and opportunities. The utilization of composites, known for their lightweight nature, durability, and versatility, has created a ripple effect across various sectors. Companies are now seeking individuals proficient in composite technologies to drive innovation and meet the evolving market needs. This shift underscores the importance of understanding the impact of composites on job opportunities, as it not only shapes skill requirements but also paves the way for a new era of specialized roles and responsibilities.
Skill Demand
Specialized Composite Fabrication
Specialized composite fabrication stands at the forefront of skill demands in industries leveraging composite materials. This aspect focuses on the intricate process of crafting composite structures, requiring specialized knowledge in material properties, molding techniques, and quality control. Professionals skilled in composite fabrication play a vital role in ensuring the structural integrity and performance of composite components used in diverse applications. The meticulous attention to detail and precision required in composite fabrication make it a sought-after skill in industries where composite materials are extensively employed.
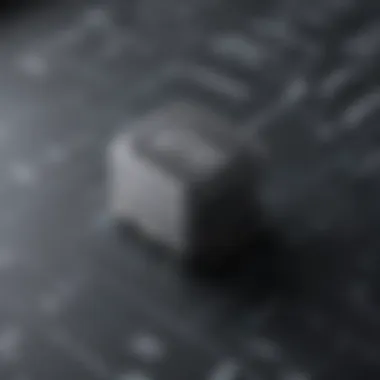
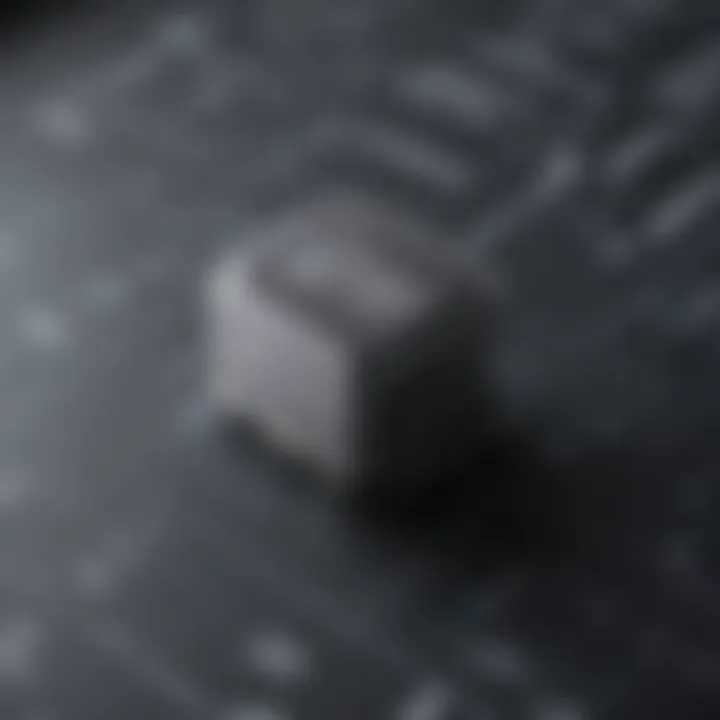
Design Engineering
Design engineering within the realm of composites encompasses the strategic development and optimization of composite structures and components. Design engineers leverage their expertise to conceptualize, analyze, and refine composite designs to meet specific performance criteria. They are tasked with integrating innovative solutions, material selection, and manufacturing processes to achieve optimal results. Design engineering plays a crucial role in enhancing the functionality and efficiency of composite products, making it a key factor in driving technological advancements and pushing the boundaries of composite applications.
Future Trends and Innovations
Composites have become a driving force in modern job industries, propelling the need for continuous evolution and foresight in future trends and innovations. The realm of composites is witnessing a shift towards advanced technologies and materials, shaping the landscape of various sectors. In this article, the exploration of Future Trends and Innovations delves deep into the pivotal changes that composite materials are bringing to industries. The significance of anticipating upcoming trends lies in adapting to new challenges and capitalizing on emerging opportunities. It is vital for professionals in this field to stay abreast of the latest advancements to remain competitive and relevant in a rapidly evolving market. By understanding the trajectory of innovations in composites, professionals can position themselves at the forefront of industry trends.
Automation in Composite Manufacturing
Automation is revolutionizing composite manufacturing processes, driving efficiency, precision, and scalability in production. The integration of automated systems in composite manufacturing streamlines operations, reduces manual labor, and enhances overall productivity. By leveraging robotics, artificial intelligence, and advanced machinery, manufacturers can achieve higher output rates with consistent quality standards. Automation not only expedites production cycles but also ensures minimal errors, resulting in cost savings and improved final product quality. As industries increasingly embrace automation in composite manufacturing, the demand for skilled technicians proficient in operating automated systems is on the rise. Understanding the intricate harmony between technology and manufacturing is crucial for professionals looking to excel in this dynamic landscape.
Advanced Composite Materials
The continuous development of advanced composite materials marks a significant stride towards enhancing product performance and durability. Advanced composite materials offer superior properties such as enhanced strength-to-weight ratios, temperature resistance, and corrosion resilience. By incorporating nanotechnology, carbon fibers, and advanced resins, manufacturers can achieve unparalleled material characteristics that outperform traditional alternatives. The utilization of advanced composite materials opens new avenues for innovation in various industries, driving breakthroughs in aerospace, automotive, and construction sectors. Professionals well-versed in the properties and applications of advanced composite materials are poised to lead the way in unlocking the full potential of these cutting-edge solutions.
Industry Integration
The integration of Industry 4.0 principles in composite manufacturing signifies a paradigm shift towards interconnected, smart production systems. Industry 4.0 integration leverages technologies such as the Internet of Things (IoT), big data analytics, and cyber-physical systems to optimize manufacturing processes. By interconnecting machines, systems, and processes, Industry 4.0 fosters real-time data exchange, predictive maintenance, and adaptive production capabilities. This integration enhances operational efficiency, reduces downtime, and enables agile decision-making in composite manufacturing environments. Embracing Industry 4.0 principles empowers organizations to unlock new levels of productivity, flexibility, and sustainability, shaping the way for the future of composite manufacturing.
Challenges and Opportunities
In the realm of modern job industries, the focus on challenges and opportunities related to composites is paramount. Addressing these aspects ensures the seamless integration of composite materials within diverse sectors. Challenges pose significant hurdles that need innovative solutions for advancement. Meanwhile, opportunities open doors to new possibilities and growth potential. Understanding and navigating through these challenges and opportunities are crucial for organizations utilizing composites in their operations.
Regulatory Compliance
Safety Standards
Safety standards within the composite industry are integral to ensuring the quality and reliability of composite products. These standards encompass stringent guidelines and protocols that guarantee the safety and performance of composite materials. Adhering to safety standards not only enhances the credibility of products but also fosters a culture of safety consciousness within the industry. Emphasizing safety compliance reduces risks, instills consumer trust, and streamlines operational processes. Despite the rigidity of safety standards, their adherence results in products that meet high-quality benchmarks and instill confidence in end-users.
Environmental Regulations
The adherence to environmental regulations is a pivotal aspect of composite production. Environmental regulations dictate the sustainable practices and processes involved in manufacturing composite materials. Emphasizing eco-friendly production methods reduces the carbon footprint and minimizes environmental impact. Incorporating regulations focusing on waste management, emission control, and sustainable sourcing of raw materials ensures a greener approach to composite manufacturing. While adhering to environmental regulations may pose initial challenges, the long-term benefits are immense, contributing to a cleaner and more sustainable ecosystem.