Revolutionizing Manufacturing with Advanced Machine Vision Technology
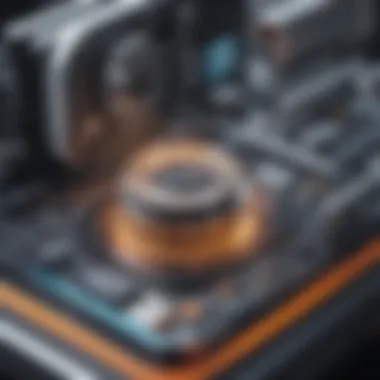

Tech Trend Analysis
Machine vision technology is currently at the forefront of revolutionizing manufacturing processes, with its advanced imaging systems reshaping production facilities worldwide. This innovative technology is enhancing quality control, increasing automation, and boosting efficiency to new heights. Consumers are reaping the benefits of improved product quality and reliability, thanks to machine vision's ability to ensure precision and accuracy in every step of the manufacturing process. Looking ahead, the future predictions for machine vision technology in manufacturing are promising, with further advancements expected to streamline operations and drive unprecedented levels of productivity and cost-effectiveness.
Product Reviews
When it comes to evaluating machine vision technology, it is essential to consider its key features and specifications. These systems typically include high-resolution cameras, intelligent algorithms, and real-time processing capabilities, enabling them to inspect products with unmatched accuracy and speed. Performance analysis reveals that machine vision technology significantly reduces errors and defects, leading to enhanced efficiency and resource optimization within manufacturing facilities. While the pros of machine vision are undeniable, such as improved quality control and increased automation, there are some cons to be mindful of, including initial investment costs and potential system complexities. Overall, a strong recommendation is to integrate machine vision technology into manufacturing processes to reap its substantial benefits and stay competitive in the industry.
How-To Guides
For those interested in leveraging machine vision technology in manufacturing, it is crucial to understand the basics of this innovative tool. An introduction to the topic covers the fundamental principles of machine vision and its applications in quality control and automation. Step-by-step instructions guide users on setting up and calibrating machine vision systems to ensure optimal performance and accuracy. Additionally, tips and tricks offer insights into maximizing the potential of machine vision technology, from selecting the right cameras to fine-tuning image processing algorithms. Troubleshooting guidelines help address common issues that may arise during the implementation and operation of machine vision systems, empowering users to overcome challenges effectively and maintain seamless production workflows.
Industry Updates
Recent developments in the tech industry have highlighted the growing importance of machine vision technology in various sectors. The analysis of market trends indicates a rising demand for advanced imaging solutions to drive efficiency and innovation in manufacturing processes. As businesses and consumers increasingly recognize the value of machine vision technology, its impact on production quality and operational efficiency continues to expand. By staying informed about the latest industry updates and adopting cutting-edge machine vision solutions, companies can gain a competitive edge and meet the evolving needs of the market effectively.
Introduction
In the realm of modern manufacturing, revolutionizing the traditional workflows with cutting-edge technology has become imperative for staying competitive in a rapidly evolving market landscape. Machine Vision Technology stands at the forefront of this transformation, offering a paradigm shift in how quality control, automation, and overall efficiency are approached in production environments. By leveraging sophisticated imaging systems and advanced algorithms, machine vision technology introduces a new dimension of precision and optimization to manufacturing processes, setting a new standard for operational excellence.
Understanding Machine Vision
The Concept of Machine Vision
Machine Vision, at its core, revolves around the utilization of cameras and image processing algorithms to extract meaningful information from visual data. This sophisticated technology enables machines to 'see' and interpret their surroundings, mimicking the capabilities of human vision with unparalleled accuracy and speed. One of the key hallmarks of Machine Vision is its ability to analyze and make decisions based on image data in real-time, a capability that significantly enhances automation and quality control processes in manufacturing settings. While the technology presents diverse benefits such as improved product quality and enhanced efficiency, challenges like complex calibration requirements and high initial setup costs necessitate careful consideration during implementation.
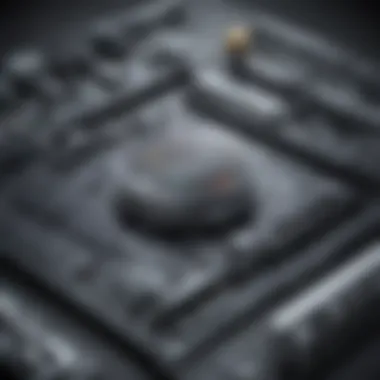
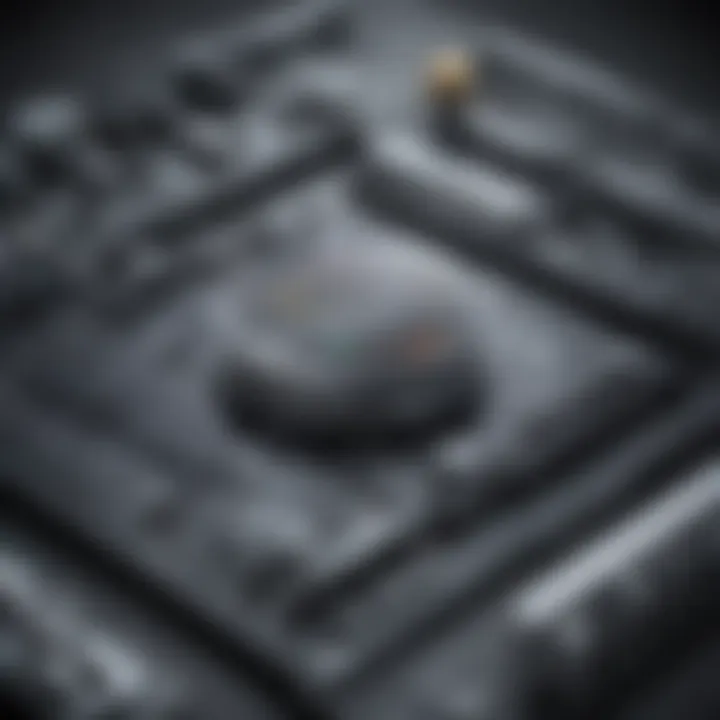
Key Components of Machine Vision Systems
The functionality of a Machine Vision system depends on several critical components working in harmony to capture, process, and interpret visual information. Cameras, lighting sources, lenses, and image sensors constitute the essential hardware elements, forming the foundation for image acquisition in machine vision applications. On the software side, algorithms for image analysis and machine learning play a pivotal role in transforming raw image data into actionable insights. These components synergize to enable tasks such as defect detection, object recognition, and quality assessment with remarkable precision and speed, highlighting the versatility and power of Machine Vision systems across diverse manufacturing domains.
Applications Across Industries
The versatility of Machine Vision technology transcends industry boundaries, finding applications in a myriad of sectors such as automotive, electronics, pharmaceuticals, and food processing. In automotive manufacturing, machine vision systems are instrumental in detecting defects in car bodies, ensuring stringent quality standards are met during production. Similarly, in pharmaceutical industries, machine vision plays a crucial role in verifying the correctness of labels on medication packaging, safeguarding against potential errors. The widespread adoption of Machine Vision across industries underscores its universal appeal and adaptability, emphasizing its status as a game-changer in modern manufacturing landscapes.
The Evolution of Manufacturing
Traditional Manufacturing Practices
Challenges Faced
The challenges faced in traditional manufacturing practices are multifaceted, ranging from inefficiencies in manual inspections to limitations in detecting minute defects. These challenges encompass the need for time-consuming inspection processes, human errors, and the inability to handle large volumes of data effectively. By addressing these challenges, machine vision technology emerges as a viable solution by offering automated, rapid, and accurate inspection capabilities. While traditional methods struggle with consistency and scalability, machine vision systems excel in providing real-time, reliable data insights.
Limitations of Human Inspection
Human inspection in manufacturing processes poses inherent limitations due to factors such as fatigue, subjectivity, and restricted processing speeds. The reliance on human inspectors can lead to inconsistencies in detecting defects, increased error rates, and slower production cycles. Machine vision technology overcomes these limitations by implementing objective, high-speed inspection processes that operate tirelessly without compromising accuracy. By replacing manual inspection with automated systems, manufacturers witness enhanced quality assurance and streamlined operations.
Introduction of Automation
The introduction of automation in manufacturing signifies a paradigm shift towards increased efficiency and reduced labor-intensive tasks. Automation streamlines production operations, minimizes human intervention, and optimizes resource utilization. Machine vision technology aligns seamlessly with automation by enabling intelligent decision-making processes, precise measurements, and adaptive workflows. Through the integration of machine vision systems, manufacturers achieve higher throughput rates, improved product quality, and enhanced operational excellence, marking a fundamental advancement in the manufacturing landscape.
Machine Vision Integration
Machine Vision Integration is a pivotal aspect in the realm of modern manufacturing processes. It encapsulates the fusion of advanced imaging technology into production practices, revolutionizing quality control, automation, and efficiency. By incorporating machine vision systems, manufacturing industries can elevate their operational standards and ensure unparalleled precision in their processes. The integration of machine vision brings forth a new era of technological advancement, streamlining production facilities and enhancing overall output. The synergy between machine vision technology and manufacturing lays the foundation for a more robust and competitive industry landscape.
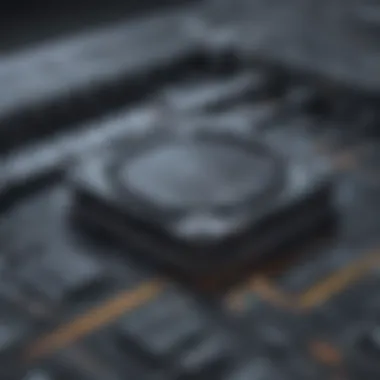
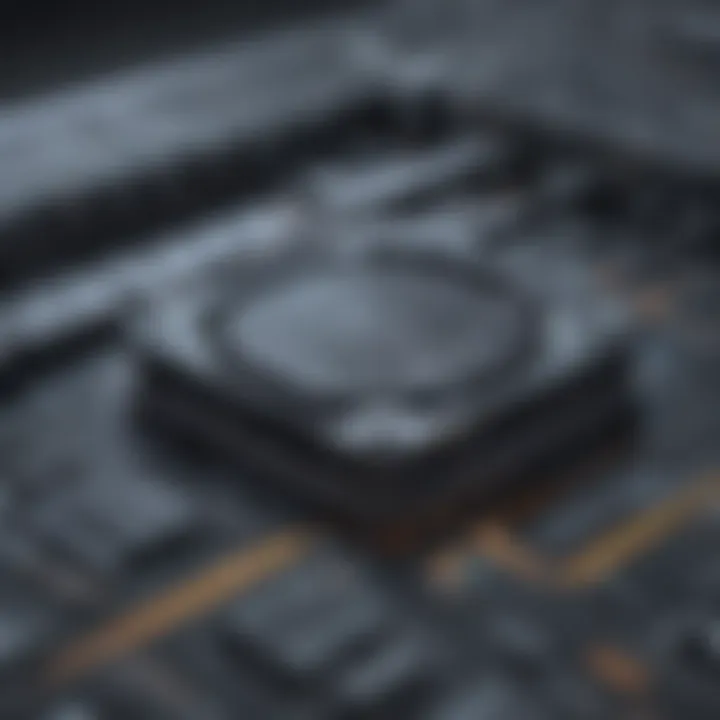
Advantages of Machine Vision
Enhanced Quality Control
Enhanced Quality Control stands as a cornerstone benefit of machine vision integration in manufacturing. This facet emphasizes the heightened level of accuracy and consistency in inspecting and monitoring production processes. By leveraging machine vision for quality control purposes, manufacturers can detect defects, anomalies, and inconsistencies with unprecedented precision. The distinctive feature of Enhanced Quality Control lies in its ability to analyze and assess products in real-time, ensuring adherence to strict quality standards. Despite its advantages, challenges like calibration complexities and software compatibility issues may arise, necessitating careful implementation strategies to maximize its efficacy.
Improved Efficiency and Productivity
Improved Efficiency and Productivity serve as key drivers of adopting machine vision technology in manufacturing. This aspect focuses on the streamlined operations and increased output achievable through automation and data-driven decision-making. Machine vision systems optimize workflow processes, reduce human error, and enhance productivity levels significantly. The defining characteristic of Improved Efficiency and Productivity lies in its capacity to expedite manufacturing timelines and minimize operational bottlenecks. While the benefits are evident, potential drawbacks such as initial setup costs and system maintenance requirements need to be considered for sustainable integration within manufacturing environments.
Cost Reduction Benefits
Cost Reduction Benefits emerge as a compelling advantage of embracing machine vision integration in manufacturing operations. This component underscores the financial efficiencies gained through reduced waste, enhanced resource utilization, and minimized rework expenses. Machine vision technology enables companies to streamline their production lines, minimize material losses, and optimize resource allocation effectively. The unique feature of Cost Reduction Benefits lies in their ability to deliver tangible returns on investment through improved operational performance and resource management. However, challenges related to initial investment costs and employee training initiatives may pose obstacles to reaping the full cost-saving advantages of machine vision implementation.
Challenges and Implementation
Data Processing Complexities
Data Processing Complexities present themselves as a core challenge in the integration of machine vision technology within manufacturing settings. This aspect delves into the intricacies of handling and analyzing vast amounts of data generated by machine vision systems. Manufacturers encounter challenges related to processing speed, data accuracy, and system compatibility when managing data outputs from machine vision applications. The critical characteristic of Data Processing Complexities pertains to the dependence on robust data processing algorithms and software frameworks to derive actionable insights from raw image data. Although data processing complexities may impede seamless integration, innovative solutions like cloud computing and edge computing offer avenues to address these hurdles.
Training Machine Learning Models
Training Machine Learning Models emerges as a critical aspect of implementing machine vision technology in manufacturing workflows. This element revolves around the training and optimization of machine learning algorithms to interpret and classify visual data accurately. Manufacturers invest resources in developing and fine-tuning machine learning models to enhance the accuracy and reliability of quality control processes. The unique feature of Training Machine Learning Models lies in its adaptability and learning capability, enabling continuous improvement of detection algorithms over time. Despite its benefits, challenges such as data labeling requirements and algorithm scalability need to be navigated to ensure successful implementation and sustained performance.
Overcoming Compatibility Issues
Overcoming Compatibility Issues serves as a significant hurdle in the seamless integration of machine vision technology within diverse manufacturing infrastructures. This segment focuses on the coordination and alignment of various hardware and software components to ensure interoperability and functionality. Manufacturers face hurdles related to system integration, software dependencies, and equipment synchronization when deploying machine vision systems. The key characteristic of Overcoming Compatibility Issues lies in the meticulous planning and testing required to achieve cohesive connectivity among disparate technologies. While compatibility issues pose initial complexities, proactive measures like protocol standardization and cross-platform testing can streamline integration and mitigate operational disruptions.
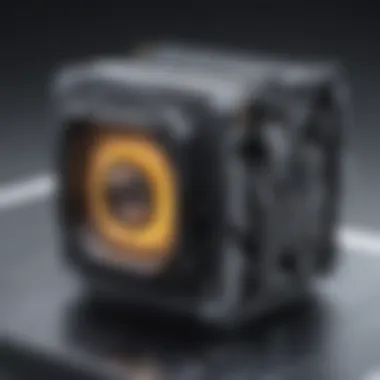
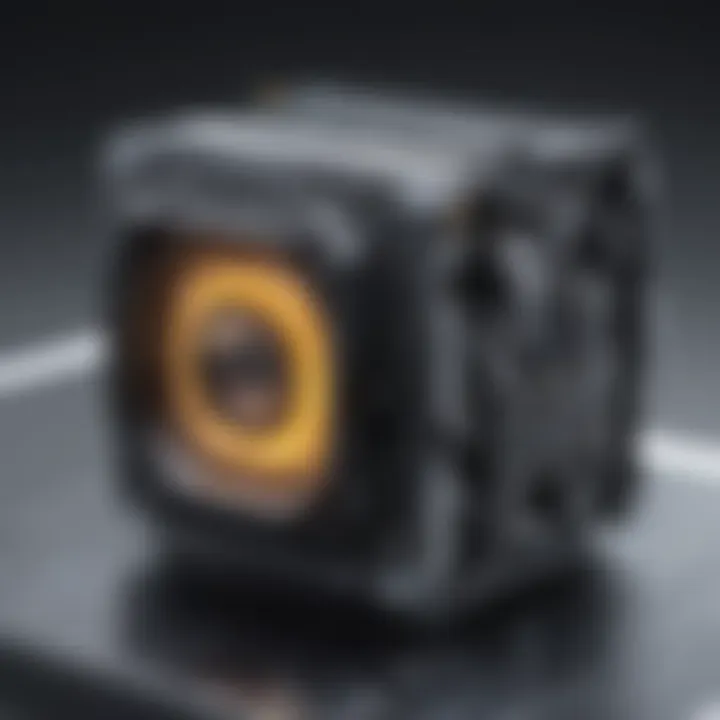
Applications in Manufacturing
In the realm of modern manufacturing, the application of machine vision technology holds significant importance. By integrating machine vision systems into various stages of production, manufacturers can achieve unparalleled levels of quality control, operational efficiency, and cost reduction benefits. One of the key aspects of machine vision in manufacturing is its ability to enhance product quality through precise inspection and identification processes. Moreover, the implementation of machine vision technology enables real-time defect detection and prevention, ensuring that products meet the highest quality standards before reaching the market. Additionally, machine vision systems play a crucial role in streamlining production processes, ultimately leading to improved overall efficiency and productivity levels across different industries.
Quality Assurance
Defect Detection and Prevention
The segment of defect detection and prevention within quality assurance processes is of paramount importance in modern manufacturing settings. Utilizing advanced machine vision algorithms and image processing techniques, manufacturers can accurately identify and eliminate defects in products at early production stages. The key characteristic of defect detection and prevention systems lies in their ability to detect minuscule discrepancies in products that are often undetectable by the human eye. This proactive approach not only ensures the consistent quality of manufactured goods but also minimizes waste and rework costs. Although the implementation of defect detection and prevention systems requires initial investment in technology and training, the long-term benefits in terms of improved product quality and customer satisfaction are substantial.
Precision Inspection
Precision inspection, another crucial aspect of quality assurance in manufacturing, revolves around the meticulous examination of product components to ensure adherence to rigorous quality standards. Machine vision technology plays a pivotal role in enabling high-precision inspection tasks that are essential for verifying the accuracy and integrity of complex parts and assemblies. The inherent advantage of precision inspection lies in its ability to detect even the slightest deviations from specified tolerances, guaranteeing the flawless performance of the final product. While precision inspection systems offer unmatched accuracy and repeatability, they often require sophisticated setup and calibration processes to achieve optimal results.
Part Identification
Part identification, a fundamental function of machine vision technology in manufacturing, involves the automated recognition and classification of individual components within a larger production context. By employing machine learning algorithms and pattern recognition techniques, manufacturers can streamline the assembly process by accurately identifying various parts with speed and precision. The unique feature of part identification systems lies in their capacity to handle vast datasets and varying part geometries without compromising accuracy or efficiency. While the automated part identification process offers significant benefits in terms of reducing manual labor and minimizing errors, it may require continuous refinement and adjustment to adapt to evolving production requirements and new part configurations.
Challenges and Future Prospects
In the realm of machine vision technology, delving into the challenges and future prospects is paramount to understanding the evolution of manufacturing processes. The intricacies of data analysis pose a significant hurdle, demanding attention and innovative solutions for seamless integration. Handling large data sets within machine vision systems requires precise calibration and sophisticated algorithms to ensure accurate outputs. The ability to process vast amounts of data efficiently is a key characteristic of handling large data sets, influencing the overall quality and reliability of manufacturing operations. While this aspect presents complexity, it also offers enhanced insights and optimizations for production processes.
Integration with AI algorithms marks a major stride in optimizing machine vision systems for streamlined performance. By fusing artificial intelligence with machine vision technology, manufacturers can achieve greater precision and automation in their processes. The synergy between AI algorithms and machine vision enhances decision-making capabilities and facilitates real-time adjustments to ensure quality standards are met consistently. However, balancing the integration of AI algorithms with machine vision systems demands careful considerations to harmonize operations effectively.
Ensuring data security within the realm of machine vision is of paramount importance to safeguard sensitive information and maintain operational integrity. The robustness of data security measures directly impacts the reliability and trustworthiness of machine vision applications. Implementing stringent protocols and encryption mechanisms fortifies data protection, preserving the confidentiality of critical production data. While prioritizing data security adds layers of complexity to machine vision systems, it instills confidence in stakeholders and strengthens the foundation of digitized manufacturing processes.
Emerging Technologies
The emergence of advanced technologies within the machine vision domain propels manufacturing industries towards unprecedented efficiencies and capabilities. Advancements in deep learning revolutionize how machine vision systems interpret and process visual data, elevating accuracy and performance standards. The core characteristic of advancements in deep learning lies in its capacity to adapt and learn from complex data patterns, enabling enhanced predictive analytics and anomaly detection. Embracing deep learning technologies in machine vision amplifies the accuracy and reliability of inspection tasks, driving sharper insights and operational optimizations.
Enhanced sensor technologies play a pivotal role in enhancing the sensory capabilities of machine vision systems, elevating sensing precision and adaptability. The key characteristic of enhanced sensor technologies lies in their heightened sensitivity to capture subtle variations and nuances in visual data. By integrating advanced sensors into machine vision setups, manufacturers can achieve unparalleled control over inspection processes and mitigate potential errors effectively. Despite the nuanced advantages of enhanced sensor technologies, calibration and maintenance are essential to sustain optimal sensor performance tailored for diverse manufacturing applications.
The integration of augmented reality into machine vision applications heralds a new era of immersive experiences and enhanced visualization for production environments. Augmented reality overlays digital information onto physical spaces, offering real-time guidance and contextual data for more informed decision-making. The unique feature of augmented reality integration lies in its ability to superimpose virtual elements onto real-world scenarios, empowering operators with interactive insights and operational clarity. While augmenting reality enriches user experiences and enhances situational awareness, achieving seamless integration with machine vision systems necessitates intricate calibration and interface optimizations.