Navigating the 3D Printing Design Process
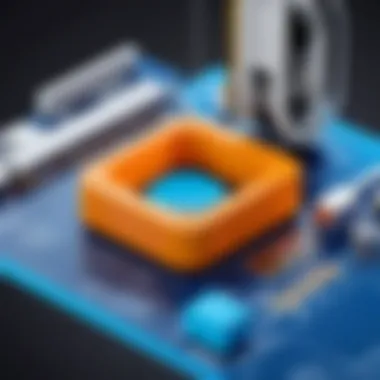

Intro
The rapid evolution of technology has changed the landscape of many industries, and 3D printing stands out as a transformative force. From healthcare to architecture, this innovation has unlocked possibilities that were once the realm of science fiction. It's not just about making items; it's a whole new way of thinking about design and production.
In this article, we take a detailed look at the design process behind 3D printing. Each step in this journey is essential, whether you’re a creator at heart or a tech enthusiast looking to grasp the intricate world of three-dimensional manufacturing. One might wonder, why is understanding this process beneficial? The answer lies in the increasing integration of 3D printing into various sectors, which empowers professionals and hobbyists alike to innovate and solve real-world problems.
This narrative will cover the phases from the spark of an idea to the final touches after printing. We will dive into tools and techniques that enhance creativity while identifying potential challenges that could derail even the best-laid plans. It’s all about guiding you through navigating the complex yet rewarding 3D printing design landscape.
Tech Trend Analysis
Overview of the current trend
Today, the 3D printing industry showcases advancements at a breakneck pace. According to recent reports, the 3D printing market is projected to grow exponentially, often attributed to its application in rapid prototyping and custom manufacturing. The technology is not just getting better; it's becoming more accessible too. With every passing day, hobbyists find more user-friendly printers at lower prices, allowing even those without technical expertise to join the fray.
Implications for consumers
For the average consumer, this shift means access to a treasure trove of personalized products. Want a specific piece of jewelry or a part for a beloved old appliance? The capabilities of 3D printing can make those wants a reality. Furthermore, businesses can now offer tailored solutions that cater specifically to individual customer needs, leading to heightened satisfaction.
Future predictions and possibilities
Looking ahead, one can only speculate where this trajectory will lead. Experts predict that innovative materials will emerge, especially those that are sustainable and eco-friendly. Eventually, 3D printing could even play a role in housing construction, creating everything from furniture to entire homes. It’s an exciting time to keep an eye on this tech!
"The true power of 3D printing lies not just in its ability to produce parts, but in its capacity to democratize design—letting anyone with a computer and a printer become a creator."
Product Reviews
Overview of the product
While the article focuses more on the design process rather than specific products, it’s worth mentioning popular 3D printers that have gained traction among users. For instance, the Prusa i3 MK3 is favored for its reliability, while the Creality Ender 3 stands out for its affordability.
Features and specifications
Each of these models offers unique features. The Prusa i3 MK3, with automatic bed leveling and a robust support community, appeals to beginners and seasoned users alike. Meanwhile, the Creality Ender 3 provides a larger build volume, making it feasible to print larger items.
Performance analysis
Many enthusiasts praise the print quality and ease of use of these machines. However, consumers might find the learning curve steep initially. Being able to tinker with settings can lead to beautifully printed objects but may require patience and trial-and-error.
Pros and cons
- Prusa i3 MK3
Pros: High-quality prints, great support.
Cons: Higher price point. - Creality Ender 3
Pros: Excellent value for money.
Cons: Requires some assembly and modifications for optimal performance.
Recommendation
Both products have merit based on the user's needs. If you are looking for ease and community support, Prusa might be worth the investment. For those entering the field on a budget, the Creality provides a solid starting point.
How-To Guides
Prelude to the topic
Beginning your 3D printing journey can seem overwhelming with countless tools and methods to learn. However, breaking it down step by step can simplify the process, making it more manageable.
Step-by-step instructions
- Conceptualize your design: Start with an idea. Sketch it out or use computer software.
- Choose appropriate software: Programs like Tinkercad or Fusion 360 can assist in building your model.
- Prepare the model for printing: This includes slicing the model using software like Cura.
- Print: Transfer the sliced file to your printer and set it up.
- Post-process: Finish your print. This might involve sanding or painting to enhance aesthetics.
Tips and tricks
- Always test print small sections when trying new designs.
- Don’t rush through settings; take your time to understand what each does with your print.
Troubleshooting
- If prints are not adhering, check the bed level and surface.
- Streaks may indicate a blockage in the nozzle; cleaning it regularly can help mitigate this.
Industry Updates
Recent developments in the tech industry
Governments and private sectors are heavily investing in upgrading their 3D printing capabilities. More research funds are allocated towards exploring bioprinting, enabling the possibility of printing tissues or organs.
Analysis of market trends
There is a noticeable shift towards eco-friendly filament materials as consumers demand greener options. Innovations like biodegradable filament are gaining traction.
Impact on businesses and consumers
With these developments, businesses that adapt to 3D printing technology can reduce costs, streamline their manufacturing processes, and cater to a more customized consumer base. This is proving beneficial not only for businesses but also for consumers who now enjoy personalized products at their fingertips.
Prelude to 3D Printing
The world of 3D printing stands as a pivotal evolution in manufacturing and design, reshaping traditional approaches across various industries. At its core, 3D printing is not just a technological novelty; it encompasses a multitude of benefits that extend far beyond mere novelty. This article aims to dissect the intricate design process associated with this remarkable technology, illuminating how each phase contributes to the final product.
Overview of 3D Printing Technology
3D printing technology takes digital designs and brings them to life through the layering of materials. It operates on principles that fundamentally differ from conventional additive processes. Rather than removing material from a block, subtractive manufacturing, 3D printing builds items layer by layer, a process known as additive manufacturing. This transformation in manufacturing methods opens doors to complicated geometries and designs that would be otherwise unachievable.
In today’s landscape, various types of 3D printing technologies exist, such as Fused Deposition Modeling (FDM), Stereolithography (SLA), and Selective Laser Sintering (SLS). Each method carries its advantages and is suited for different applications:
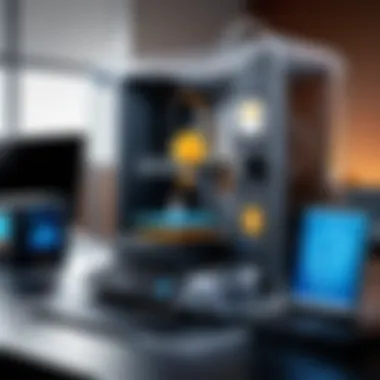

- FDM is widely accessible and perfect for prototyping and educational purposes.
- SLA excels in high-resolution prints, making it a favorite in jewelry and dental industries.
- SLS can handle composite materials, providing strength and durability for functional parts.
The versatility of this technology has resulted in its adoption in sectors from aerospace to healthcare, igniting innovation at every turn.
Importance of the Design Process
The design process in 3D printing is not just a series of steps; it is the backbone that supports the entire production lifecycle. Without a methodical approach to design, the very capabilities of 3D printing could remain underutilized, leading to missed opportunities.
The importance of this design process can be summed up as:
- Precision and Efficiency: A well-thought-out design can minimize errors during printing, saving both time and costs.
- Material Optimization: Designers must choose materials that complement their design objectives, which could drastically affect the final product’s functionality and efficiency.
- Usability and Aesthetics: Effective design extends beyond utility; it includes understanding how the end user interacts with the product.
The iterative nature of design in 3D printing requires constant evaluation and refinement, ensuring that the final product not only meets specifications but also delights its users.
"In design, if you don’t understand the process, you can't hope to mitigate challenges and achieve an optimal outcome."
In essence, the design process is where creativity melds with practicality. Emphasizing its importance leads to products that are both innovative and grounded in reality, further underscoring why a structured approach is vital in the ever-evolving domain of 3D printing.
The Conceptual Foundation
The conceptual foundation of 3D printing is akin to laying down the bedrock for a grand structure. The thought process and aspirations that precede tangible creation form a critical aspect of the design journey. It encompasses understanding the scope of what 3D printing can achieve and aligning that with specific needs and objectives. This phase ensures that the design endeavors are not just whimsical ideas but have a purpose that addresses real-world problems or satisfies a niche interest.
Identifying the Need for 3D Printing
Recognizing the need for 3D printing is the first step in this intricate dance of design. It often begins with a spark - perhaps an inefficiency you've noticed in an existing product or a challenge that seems insurmountable. It's vital to adopt a mindset open to possibilities rather than limitations.
For example, imagine a small workshop that produces custom bicycle parts. The owner notices that many cyclists prefer personalized components tailored to their unique riding styles. Here lies an opportunity to leverage 3D printing technology. The demand for personalization and rapid prototyping has increased drastically across numerous sectors including healthcare, automotive, and consumer goods. Identifying where 3D printing could flourish or fill a gap can define the pathway forward.
Also, consider factors like time, cost, and material availability. Perhaps a traditional manufacturing method is too slow for the desired turnaround or is unable to use sustainable materials. By pinpointing these issues early on, designers can align their innovations with broader industry trends and consumer expectations.
Setting Design Objectives
Once the need is identified, the next logical step is setting clear, specific design objectives. This requires dissecting the goal into actionable elements. What do you want the printed object to do? What are its dimensions? What materials will it be made from? These questions aren't just trivial—they shape the very essence of the design process.
To put it into perspective, if we're designing an adjustable smartphone stand, the objectives might include:
- Stability: The design should hold various smartphone models securely without toppling.
- Adjustability: It should allow users to modify angles for comfortable viewing.
- Aesthetics: A visually pleasing design that complements modern interiors.
- Material Efficiency: Using biodegradable filament to appeal to eco-conscious consumers.
Every goal should be measurable and realistic. This ensures that the end product meets customer expectations while remaining feasible within the available technological constraints.
"A good objective is like a compass; it guides you in the right direction during your design journey."
Phase One: Ideation and Conceptualization
The journey of 3D printing design begins in Phase One: Ideation and Conceptualization. This crucial stage lays the groundwork for everything that follows. At its core, ideation is about generating ideas and exploring their potential before diving deeper into technicalities. Whether you’re a seasoned designer or a newcomer swimming in the waters of 3D printing, this phase is essential. Here, creativity meets practicality, transforming abstract thoughts into concrete concepts.
In this phase, identifying the exact need for a product is vital. It helps establish a clear direction for your design process. Understanding user wants—like comfort, efficiency, or aesthetic appeal— can influence your prototype design significantly. This phase isn’t just about dreaming big; it’s about aligning your ideas symbiotically with real-world requirements.
Another pivotal element of this phase is the advantages derived from a well-executed ideation process. Cultivating diverse ideas not only enhances creativity but also encourages out-of-the-box thinking. It broadens the scope for innovative designs. Moreover, thorough consideration during ideation can save time and resources during later phases, as it minimizes the risk of costly missteps.
Brainstorming Techniques
Effective brainstorming techniques can lead to successful outcomes in the ideation process. Regular brainstorming sessions often serve as a springboard for creative thinking. Here’s how to make those sessions productive:
- Mind Mapping: This visual technique helps in categorizing thoughts and establishing connections between ideas. By branching out from a central theme, you can create pathways leading to unexpected insights.
- SCAMPER Method: SCAMPER stands for Substitute, Combine, Adapt, Modify, Put to another use, Eliminate, and Reverse. Each of these prompts can trigger innovative thinking by asking critical questions about existing designs.
- Role Playing: Stepping into someone else’s shoes might seem unusual, but it actually helps broaden perspectives. By understanding how different users might perceive a design, you can uncover unseen issues or enhancement opportunities.
Implementing these brainstorming techniques not only ignites creativity but also fosters collaboration, as varied viewpoints can lead to an enriched design landscape.
Sketching Initial Designs
Once the ideas start flowing, it’s time to transition from abstract concepts to tangible sketches. This transition is where imagination takes a visual form. Sketching initial designs allows designers to experiment freely.
- Low-fidelity Sketches: Creating quick and rough sketches enables designers to visualize ideas without getting bogged down in details. This step emphasizes fluidity, optimally capturing the essence of the concept.
- Iterative Design: Don’t be shy about revising your sketches! Each iteration should reflect improvements based on feedback and insights gathered during brainstorming sessions. It is perfectly okay to scrap ideas; sometimes the best designs come out of a series of trials and errors.
- Digital Tools: Using software like SketchUp or Adobe Illustrator can complement hand-drawn sketches. These programs can help enhance precision while retaining creative freedom.
"The sketch is not the end, but rather the beginning of a journey; it's where ideas start to breathe and take shape."
Gathering feedback at this stage is key. Sharing initial sketches with colleagues or potential users can provide invaluable perspective. This constructive criticism will help refine your design before you leap into the subsequent phases.
In summary, Phase One: Ideation and Conceptualization serves as the fertile ground for innovation and creativity in the realm of 3D printing design. Lay a solid foundation and watch as your concepts grow and evolve into stunning prototypes.
Phase Two: Design Development
In the realm of 3D printing, the design development phase is where ideas start to take shape. This is a critical juncture because what happens in this stage lays the groundwork for everything that follows. During design development, it’s not just about drawing or modeling; it’s about refining concepts, ensuring feasibility, and preparing the designs for the complexities of printing. Without this thorough groundwork, the risk of creating unprintable or ineffective designs leaps dramatically, causing delays and potential financial losses.
One of the most significant aspects of this phase is the ability to visualize the product in three dimensions before it becomes a reality. This not only aids in identifying potential flaws early on but also helps gather feedback from stakeholders—be it team members, clients, or potential users. Strong emphasis on this phase can lead to rapid iterations, minimizing costly mistakes later in the process.
Utilizing CAD Software
Computer-Aided Design (CAD) software is truly the backbone of the design development stage. Tools like SolidWorks, Autodesk Fusion 360, and Rhino have become indispensable for designers. These programs offer advanced features that assist in creating and altering 3D models with precision. With CAD, designers can simulate how a model will function before ever hitting ‘print.’
Additionally, CAD software allows for detailed documentation and easy adjustments. For example, if part of a design doesn’t meet specifications during simulations, tweaks can be made on the fly without starting from scratch. This saves significant time and effort while ensuring that the integrity of the design remains intact.
Moreover, the collaborative capabilities of many CAD programs can resonate well with design teams spread across different geographies. Real-time sharing and editing can help in ironing out complexities in ideas or concerns, creating a more fluid design development process.
Modeling Techniques for 3D Printing
When we talk about modeling techniques, we delve into the methods that transform an idea into a tangible design suitable for printing. Here, a few key techniques stand out.
- Parametric Modeling: This technique involves using parameters to define the features of the model. It allows for easy modifications. For instance, if a user wants a part to be slightly larger or smaller, adjustments can be made without having to redesign the entire model.
- Direct Modeling: In contrast to parametric modeling, direct modeling offers a more intuitive approach. This is particularly useful for designers who prefer to manipulate shapes freely and trial different configurations without adhering to strict parameters.
- Mesh Modeling: For more organic and complex shapes, mesh modeling techniques come into play. While this method can yield intricate designs, it often has to be converted into a solid model suitable for printing, which could involve additional steps.
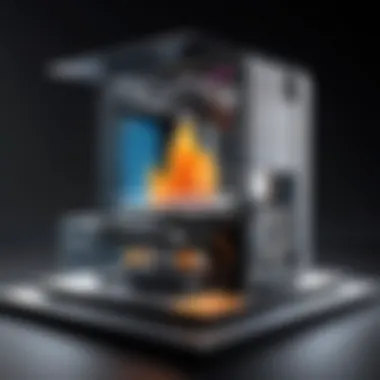

Modeling techniques not only affect the aesthetic appeal of the final product but also influence its structural integrity. Using the appropriate technique based on the intended use of the model can make or break the design’s success in practical applications.
Phase Three: Prototyping
Prototyping stands as a pivotal stage in the 3D printing design process. This phase translates ideas into tangible forms, allowing designers to visualize and assess their concepts before committing to the final product. Prototypes serve multiple purposes: they clarify design intent, enable early detection of potential flaws, and provide a hands-on experience that theoretical sketches simply can't achieve.
The prototyping phase is beneficial not only for refining design but also for gathering feedback from stakeholders or potential users. Such input is invaluable, as it shapes the final outcome, ensuring the product aligns with market expectations. As a whole, the prototyping process fosters innovation and efficiency, allowing designers to iterate swiftly.
Rapid Prototyping Methods
Rapid prototyping is crucial because it introduces various methods that speed up the design process. Techniques like Selective Laser Sintering (SLS), Stereolithography (SLA), and Fused Deposition Modeling (FDM) are prominently used in the industry. These methods vary in their application and materials but all share a common goal: producing functional models quickly.
- Selective Laser Sintering (SLS) uses a laser to fuse powdered materials, making sturdy prototypes ideal for testing durability.
- Stereolithography (SLA) employs ultraviolet light to cure liquid resin into solid forms, providing high-resolution and intricate features.
- Fused Deposition Modeling (FDM) extrudes melted filament to build objects layer by layer, often favored for its accessibility and affordability.
Ultimately, opting for a particular method depends on the project's needs, material specifications, and desired finish. The key is to select a technique that balances speed with accuracy, ensuring the prototype replicates the intended design closely.
Testing and Evaluation of Prototypes
After generating prototypes, the next logical step is rigorous testing and evaluation. Prototypes must be scrutinized against predetermined criteria to ascertain their functionality, aesthetics, and performance.
Testing can encompass various evaluations:
- Functional Testing: Does the prototype serve its intended purpose? This step often involves simulating real-world conditions to expose any weaknesses.
- User Feedback: Involving actual users to provide insights can unveil usability issues not initially considered.
- Design Review: A thorough review helps identify aesthetic and ergonomic discrepancies.
- Material Analysis: Evaluating the physical properties of the prototype ensures it meets expectations regarding durability and flexibility.
A thoughtful testing protocol ultimately refines the prototype, making adjustments as necessary before advancing to the next design phase. In this way, prototyping is not just about creating a model, but about creating a bridge between concept and reality, ensuring the next step in the design process is based on informed decisions.
"Prototypes are the safety net of innovation. They allow failing quickly and learning faster, where every misstep is a step forward."
By understanding the importance and utility of prototyping, designers can ensure the integrity and success of their final products.
Phase Four: Preparing for Printing
Preparation is crucial in the 3D printing process. It’s when ideas begin to take tangible form. This phase marks the transition from digital designs to real-world objects. By understanding and managing the details in this phase, designers can greatly influence the success of the final print.
Slicing the Model
Slicing is a pivotal step in preparing for 3D printing. It essentially translates the 3D model into a set of instructions that a printer can understand, often called G-code. This process involves dividing the model into thin horizontal layers. Here’s why slicing is so important:
- Layer Resolution: Adjusting the height of each layer can directly affect the print's quality. Thinner layers often result in higher-resolution prints, capturing more detail. Conversely, thicker layers can expedite the printing process, which is advantageous when high detail isn’t critical.
- Support Structures: Not all models can stand on their own, especially those with overhangs or intricate designs. In the slicing stage, you can add necessary support structures that the printer will create during the printing process. Doing so is essential to prevent collapse and ensure accuracy.
- Path Optimization: The slicing software decides the most efficient routes for the printer’s nozzle to take. A well-optimized path reduces the time the printer spends moving between areas of the model, which can enhance production speed and, ultimately, efficiency.
When using slicing software, designers have a chance to tweak settings to achieve the best results. Familiarity with different slicing programs, such as Ultimaker Cura or PrusaSlicer, and their unique features will empower users to better prepare their models for printing.
Material Selection
The materials chosen for 3D printing can make or break a project. Material selection requires careful consideration of mechanical properties, cost, and desired aesthetics. Here are some key points to ponder:
- Types of Materials: Common options include PLA, ABS, and PETG, each with unique characteristics. For instance, PLA is known for its ease of use and eco-friendliness; however, it lacks heat resistance compared to ABS.
- Application Suitability: The intended use of the printed object is vital. A prototype may require a different material than a functional part. Understanding the end-use scenario will guide the selection process.
- Compatibility: Not all materials work well with every printer. It’s essential to ensure that the chosen material is compatible with the specific 3D printer being used.
The material not only influences the final object's durability but also its visual appeal. A professional approach to material selection can lead to objects that not only perform well but also look the part.
In closing, Phase Four is about laying the groundwork for a successful print. Careful slicing and informed material selection can lead to a smoother printing process and a more polished final product. Ultimately, this preparatory work pays dividends as the project transitions into the next phase.
Phase Five: The Printing Process
The printing phase is where the conceptual foundation laid out in earlier stages comes to life. This is the moment when digital designs take tangible form, showcasing the power of 3D printing technology. Understanding the printing process is crucial, not only for achieving desired outcomes but also for ensuring that the project meets its intended purpose and adheres to previously set objectives.
This phase consists of several key elements. First and foremost, selecting the right type of 3D printer is fundamental. Each printer offers different capabilities, speeds, and materials to work with, shaping the final product's quality and functionality. Following that, it’s essential to monitor the print job continuously. This act plays a pivotal role in mitigating potential mishaps, ensuring that the process is on track and the desired results are achieved.
Types of 3D Printers
Understanding the various types of 3D printers available on the market is not only beneficial but necessary for making informed choices. The most common types include:
- Fused Deposition Modeling (FDM): This is perhaps the most prevalent type of 3D printer. FDM printers work by extruding thermoplastic filament, layer by layer, until the object is complete. They are user-friendly and suitable for beginners because they are generally affordable and widely supported.
- Stereolithography (SLA): SLA uses a laser to cure liquid resin into solid parts. This method allows for highly detailed prints with smooth finishes. However, the resins often require post-processing, like washing and curing, to achieve their final properties.
- Selective Laser Sintering (SLS): This technology employs a powerful laser to fuse small particles of plastic, metal, or ceramic powders into a solid structure. SLS is excellent for complex geometries and functional parts. However, SLS printers tend to be more expensive and require specialized materials.
- Digital Light Processing (DLP): Similar to SLA, DLP uses light to cure resin. The key difference is that DLP projects an entire layer at once, which can lead to faster print times compared to SLA.
Each type of printer offers distinct advantages and disadvantages, making it vital to assess them against project requirements. If precision is key, for instance, SLA might be the best bet. If cost-effectiveness is more critical, FDM could be the way to go.
Monitoring the Print Job
Once the printer is selected, the job’s monitoring begins and cannot be overlooked. Throughout the printing process, attention must be paid to various conditions that can influence the outcome:
- Temperature Control: Printers must maintain optimal temperatures to avoid warping materials or causing adhesion issues. Monitoring temperature sensors is a critical part of the job.
- Print Resolution: Different print settings, like layer thickness, affect the print quality. Ensuring the printer is set to the desired resolution beforehand saves both time and resources.
- Tension on the Filament: For FDM printers, checking the tension on the filament feed is important. Too much slack can lead to under-extrusion, making the final product weaker than intended.
- Print Speed: Balancing speed with quality can be tricky. Faster speeds can result in less fidelity, while slower speeds provide more detail. It's essential to find a comfortable pace that meets the project objectives.
"Proper monitoring during the 3D printing process not only saves time and material but also reduces frustrations later in the workflow."
- Environmental Conditions: External factors like humidity or dust can also affect print quality. Ideally, 3D printers should be in clean and climate-controlled settings to produce the best results.
Phase Six: Post-Processing Techniques
Post-processing is a crucial phase in the 3D printing design process, acting as the bridge between raw filament and the finished product. Many overlook this step, thinking that once the printer has done its job, the work is complete. However, the quality of the end result can greatly depend on what happens after printing.
Indeed, post-processing not only improves aesthetics but also enhances the physical properties of the models. Certain techniques can correct minor imperfections, provide additional strength, or prepare objects for specific uses. Let us dive into two fundamental aspects of this phase: removing supports and clean-up, as well as finishing methods for achieving enhanced quality.
Removing Supports and Clean-Up
When 3D models have overhangs or intricate geometries, support structures are a necessity during printing. These supports, while vital for maintaining structure during the printing process, often can leave behind remnants that may spoil the final look of the object.
Key Steps to Removing Supports:
- Observation: First, assess where the supports are placed. Some models may have supports embedded in complex areas, making them harder to remove.
- Tools: Use tools like pliers, cutters, or specially designed support removal tools to carefully detach these supports without damaging the print. For finer details, a craft knife can be helpful.
- Cleaning: After support removal, clean the model thoroughly. This could involve washing it with soap and water or using isopropyl alcohol to remove any leftover residue.
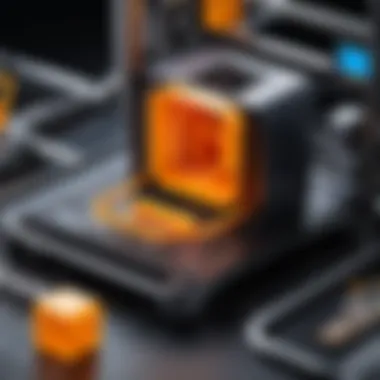

Performing this clean-up ensures that the base of the model is smooth and ready for the subsequent finish.
Finishing Methods for Enhanced Quality
Once your model is stripped of unwanted supports and cleaned up, it’s time to explore finishing techniques that take your 3D print from basic to brilliant.
Popular Finishing Techniques:
- Sanding: Applying sandpaper can smooth out rough edges and surfaces. Start with a coarse grit and gradually progress to finer grits. This step requires patience, as rushing can lead to damage.
- Painting: An attractive paint job can elevate the model. Use acrylic paints for ideal adhesion, and remember to apply a primer for an even coat. For a professional finish, consider airbrushing.
- Coating: Seal your print with a clear coat or resin. This can add shine and protect the surface from wear and tear. For functional parts, a coating might also enhance water resistance and durability.
- Polishing: For certain filament types, such as PETG or PLA, polishing can yield a glossy, glass-like finish. This is particularly useful for decorative pieces.
Every finishing method has its advantages, and the choice often depends on the intended use of the model. For example, aesthetics may be paramount for art pieces, while durability would be prioritized in functional parts.
"Post-processing is not just about making something look pretty; it’s about elevating the utility and lifespan of the creation."
Common Challenges in the Design Process
The journey through the 3D printing design process is not without its hurdles. Understanding these common challenges adds a significant layer of insight for anyone trying to navigate this intricate landscape. Each phase of design may encounter obstacles that can impede progress and, at times, lead to costly setbacks. Awareness of these issues enhances the preparedness of designers and helps in mitigating risks associated with 3D printing projects.
In this section, two primary challenges will be addressed: design limitations and material constraints. Both highlight critical aspects that influence the overall success of a 3D printing project.
Design Limitations
When embarking on the design process, one must grapple with various design limitations that can restrict creativity or functionality. Not every idea can be materialized as a physical object. Technical factors such as:
- Anatomical constraints of the object itself,
- The specifications of the 3D printer being used,
- Software capabilities often dictate what is feasible.
For example, intricate designs with interlocking parts might not print successfully due to clearance issues. Designers are often left wanting more from their creations but must adhere to the realities of technology.
"A design may flourish in concept, but the real test lies in its ability to exist in the physical world."
Moreover, there’s a delicate balance to strike between complexity and functionality. A highly complex design might not only prove difficult to print but could also affect the durability and usability of the final product. It’s not uncommon for designers to undergo multiple iterations, narrowing down to simpler forms that work better within the confines of printing technology.
Material Constraints
The choice of material fundamentally affects what can be achieved in 3D printing, thus introducing material constraints into the design equation. Each material comes with its distinct properties—strength, flexibility, weight, thermal resistance, and how it interacts with different printing techniques.
- For example, trying to create a lightweight structure using a material that’s inherently heavy could lead to functionality issues.
- On the other hand, some materials may not endure the post-processing techniques needed for enhancement, ultimately compromising the object's integrity.
A prime example could be the contrast between PLA and ABS. While PLA is often chosen for its ease of use, it may not hold up in high-heat conditions like ABS. This necessitates a thorough examination of material options to ensure suitability for the intended application.
Thus, one must be mindful of how constraints related to materials will shape the design. A designer's ability to adapt to these limitations is crucial. Every challenge presents an opportunity for innovation—creative solutions can lead to groundbreaking designs that push the boundaries of what is possible in 3D printing.
In summary, recognizing and understanding the common challenges within the 3D printing design process prepares designers for the complexities they might face. With strategically crafted designs and judicious material selection, they can navigate these obstacles effectively.
Future Trends in 3D Printing Design
The world of 3D printing is ever-evolving. With the rise of technology, new trends and advancements shape the design process, offering possibilities that were merely a dream not too long ago. Understanding these future trends is not only crucial for those in the industry but also for anyone keen on leveraging 3D printing capabilities for their projects. This section will dive into two key areas of interest: advancements in software and tools, and sustainable practices.
Advancements in Software and Tools
The realm of 3D printing design sees software tools constantly improving. Designers are witnessing powerful advancements that streamline the workflow and enhance overall efficiency.
- User-Friendly Interfaces: Software like Autodesk Fusion 360 and Tinkercad has increasingly prioritized user experience. This shift allows even non-experts to create complex designs with ease.
- Integration with AI: Artificial intelligence is becoming a game-changer. For instance, some applications now automatically suggest design improvements based on user input, reducing the guesswork traditionally involved in the design process.
- Cloud-Based Collaboration: Tools that allow for real-time collaboration over cloud platforms are gaining traction. Designers from different backgrounds can now work together seamlessly, sharing their insights and improving designs collaboratively.
“The expansion of software capabilities is vastly improving how 3D printing is approached, enabling innovative designs and faster production cycles.”
The professionals in the field must stay updated on these advancements to maximize creative potentials and efficiency. Knowing the best tools can make or break the design experience. Thus, simplifying processes allows for greater focus on creativity and innovation.
Sustainable Practices in 3D Printing
Sustainability is no longer just a buzzword; it is an essential consideration in modern design practices. As environmental concerns loom larger, 3D printing is taking steps to become more eco-friendly.
- Biodegradable Materials: The industry is seeing the introduction of materials like PLA (Polylactic Acid), which comes from renewable resources. By utilizing these alternatives, designers can significantly reduce the carbon footprint of their projects.
- Recycling Strategies: Innovative companies are exploring ways to recycle used filament. For example, some printers are compatible with materials that can be melted down and repurposed, decreasing waste.
- Energy-Efficient Printing: Advancements in printer designs often lead to lower energy consumption during the printing process. With efficient mechanical functions and updated firmware, the operation costs decrease, leading to a more sustainable setup.
Furthermore, the growing emphasis on life cycle analyses ensures that designers consider not just the end product but the materials and processes from beginning to end. This approach opens the door for more responsible design decisions.
As we look ahead, embracing modern software, coupled with sustainable practices, paves the way for a more efficient and environmentally friendly approach to 3D printing design. The future is not just about adapting but evolving to meet the demands of an increasingly conscientious world.
Finale
In wrapping up this exploration of the 3D printing design process, it’s crucial to recognize its integral role in the evolution of various fields, particularly in manufacturing, healthcare, and architecture. This journey from conceptualization to realization is not just about producing a tangible item; it’s a testament to innovation and creativity in a way that traditional methods often lack. Leveraging the unique capabilities of 3D printing, designers can push boundaries, allowing for custom solutions that meet diverse needs with greater precision.
Reflecting on the 3D Printing Design Process
Reflecting on this process reveals multiple layers of complexity that should not be overlooked. Each phase serves a vital purpose, contributing to the final outcome. For instance, ideation and preliminary design lay the groundwork, ensuring that objectives align with practical possibilities.
Moreover, discussion surrounding the need for prototyping and testing stands at the forefront of successful design, as it underscores the trial-and-error method that often leads to breakthrough solutions. This iterative approach means that designers must remain flexible, ready to adapt their vision based on findings from each prototype iteration.
To illustrate:
- Ideation Techniques: Diverse brainstorming methods enrich the creative pool.
- Prototyping: Allows for real-world feedback, critical for fine-tuning the final design.
- Material Selection: Ultimately affects the durability and functionality of the design, calling for careful consideration in the early stages.
As important as these phases are, understanding them in context highlights another aspect: the collaboration that often occurs across disciplines. Engineers, designers, and manufacturers working hand in hand leads to better outcomes.
The Importance of Continuous Learning
The rapidly changing landscape of technology, particularly in 3D printing, necessitates a mindset geared toward continuous learning. For design professionals, keeping pace with advancements in materials, software, and printing techniques is not optional—it's essential.
Now, consider these points:
- Emerging Technologies: Innovations such as multi-material printing diversify potential applications.
- Sustainability Trends: Knowledge of eco-friendly materials impacts material choices and design approaches.
- Software Developments: Mastering new CAD tools can streamline workflow, enhancing efficiency.
Continuous education isn’t just workshops. It encompasses engaging with community resources, from forums on Reddit to industry discussions on platforms like Facebook. Understanding current trends equips designers to make informed decisions, optimizing not only their work processes but also the environmental footprint of their designs.
Ultimately, the inclusivity of continual learning fosters a culture of adaptability, making it possible to tackle challenges that the evolving world of 3D printing continues to present. This approach ensures that designers not only keep abreast of new information but also cultivate a richer skill set that can lead to pioneering advancements in the field.